In the world of oil and gas exploration and extraction, the use of specialized equipment is indispensable for ensuring efficient and safe operations. One such essential component is the seating nipple tubing. Precision-engineered for specific applications in the oil and gas industries, seating nipples are an intricate part of the production tubing string that offers both versatility and reliability. This article delves into the significance, applications, and benefits of seating nipple tubing, showcasing its crucial role in industry operations.
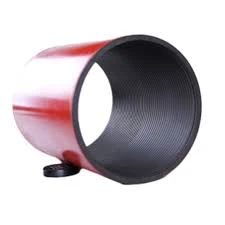
Seating nipple tubing, a vital part of the completion system in oil and gas wells, ensures the secure placement of downhole tools. Engineered meticulously to meet specific industry standards, the precision of its design enhances the efficiency of well interventions and maintenance operations. Its primary function is to provide a profile within the tubing in which downhole tools can be set and retrieved effectively. This function is fundamental for maintaining the flow of hydrocarbons and optimizing well performance.
The application of seating nipple tubing is particularly significant in wells where frequent deployment and retrieval of tools like plugs, flow control devices, and safety valves are necessary. The adaptability of the seating nipple allows it to accommodate a variety of downhole tools, making the well maintenance process more streamlined and reducing the downtime during interventions. This efficiency boost translates into significant cost savings for operators, illustrating its essential value in the highly competitive oil and gas sector.
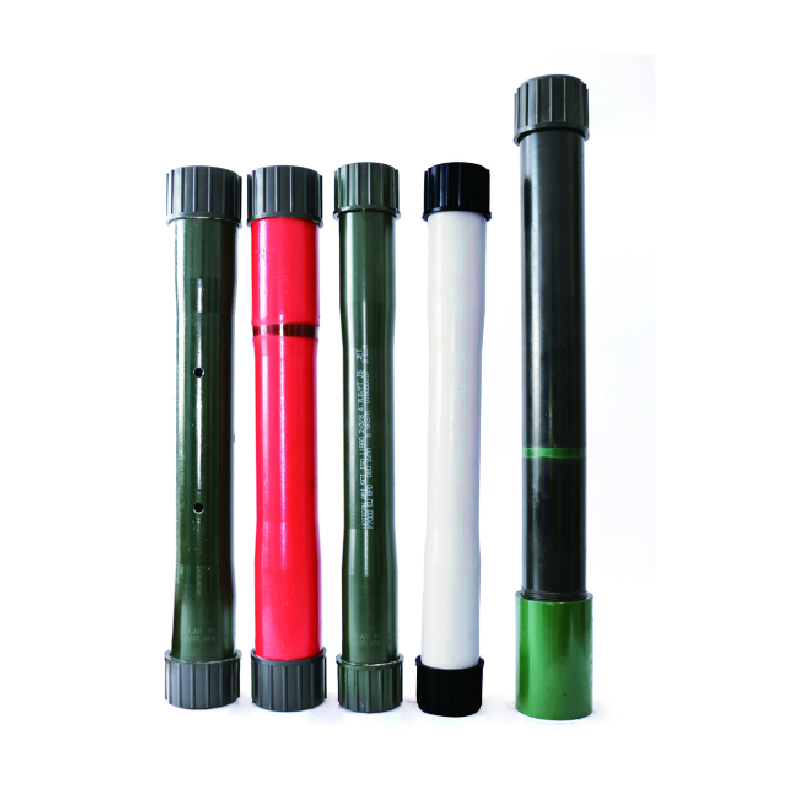
Designed with versatility in mind, there are different types of seating nipples, such as no-go nipples and selective profile nipples, each serving distinct purposes. No-go nipples provide a mechanical stop for tools that are not intended to pass through a certain point in the tubing string. On the other hand, selective profile nipples are used in advanced well designs that require the ability to set and retrieve specific tools without disturbing other tools in the completion string. This adaptability ensures that the seating nipple tubing can be tailored to meet the precise demands of various well environments.
In terms of expertise, the manufacture and installation of seating nipple tubing involve high-level engineering knowledge and adherence to strict quality control measures. The tubing must withstand aggressive downhole conditions characterized by high pressures, temperatures, and corrosive elements. Materials such as stainless steel and high-performance alloys are often used to fabricate seating nipple tubing, given their ability to resist corrosion and retain structural integrity under demanding conditions. The emphasis on quality control during manufacturing assures operators of the tubing's reliability and longevity.
seating nipple tubing
Trustworthiness in seating nipple products is built through rigorous testing and certification processes. Manufacturers conduct extensive pressure, temperature, and fatigue testing to ensure that the seating nipple complies with industry regulations and standards. Furthermore, obtaining certifications from recognized bodies such as the American Petroleum Institute (API) reinforces the product’s credibility, ultimately fostering greater trust among industry professionals.
Professionals associated with the oil and gas industry frequently stress the importance of deploying technology supported by dependable products like seating nipple tubing. The credibility of such components not only influences the operational efficiency but also reflects a commitment to safety—with reliable seating nipples playing a critical role in averting potential hazards during oil and gas extraction. Thus, utilizing these components enhances operational security and reliability—a non-negotiable aspect of the oil and gas industry operations.
Industry experts concur that the advancements in seating nipple tubing technology are not only about meeting current demands but also future-proofing the industry in anticipation of evolving challenges. Enhanced design features that improve the efficiency of seating and retrieval processes, coupled with innovations in material science, are paving the way for seating nipples that can withstand even harsher environments and operate in increasingly complex well designs.
Ultimately, the acknowledgment of seating nipple tubing as a vital component in oil and gas operations underscores the importance of ongoing research and development. As exploration and production move towards more challenging territories, the demands placed on such technologies will only increase. Through continuous innovation in engineering solutions, seating nipple tubing is poised to remain integral to the oil and gas industry's progress, enhancing operational effectiveness and ensuring continued advancements in clean and efficient energy production.