Coupling casings are integral components in various industrial and mechanical applications, serving as a protective shell for the coupling mechanisms that connect rotating shafts in machinery. Delivering optimal performance, durability, and reliability in various settings, they find their place across industries such as oil and gas, automotive, and manufacturing.
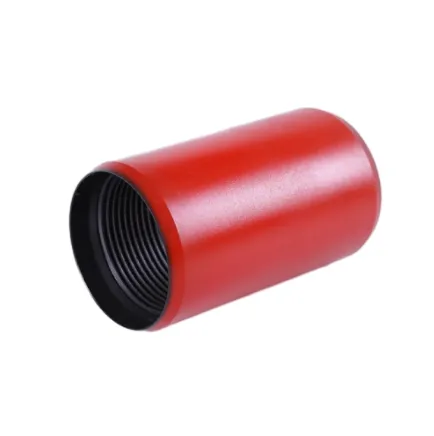
To appreciate the depth of expertise and experience required in dealing with coupling casings, one must first delve into their fundamental role and the nuances of their design. A coupling casing primarily serves as a safeguard, ensuring the mechanical coupling remains undisturbed by external elements such as dust, dirt, or moisture. This protective function is critical in harsh environments, preserving machinery efficiency and extending equipment lifespan.
In sectors like oil and gas, coupling casings are pivotal. In drilling operations, for example, the equipment operates under high stress and extreme conditions, where failure is not an option. The coupling casings in such scenarios must withstand significant pressure and temperature variations while offering superior resistance to corrosion. This necessity underscores the importance of selecting materials and designs specific to the operational requirements, ensuring reliability and safety in potentially hazardous environments.
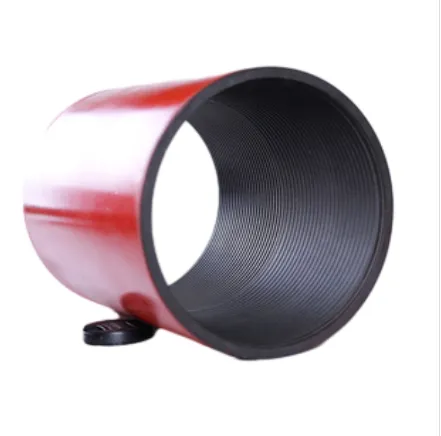
Expertise in the design of coupling casings encompasses an understanding of material science and engineering principles. Materials selection, such as stainless steel, composite materials, or specialized alloys, is fundamental, chosen based on environmental compatibility, mechanical stress requirements, and other operational conditions. A deep understanding of manufacturing processes strengthens the expertise in producing casings that meet stringent quality and performance standards.
From an authoritative standpoint, reliable coupling casing designs adhere to international standards and certifications, such as those from the American Petroleum Institute (API) or the International Organization for Standardization (ISO). These standards ensure casings are manufactured to precise specifications and quality benchmarks, fostering trust and confidence among end-users and stakeholders.
coupling casing
Building trustworthiness in the coupling casing market involves a commitment to rigorous testing and quality assurance.
Manufacturers often employ state-of-the-art testing facilities to simulate real-world conditions and assess the performance of their casings. Advanced technologies like finite element analysis (FEA) and computational fluid dynamics (CFD) play critical roles in predicting and enhancing the performance and longevity of coupling casings.
Moreover, companies with extensive experience and a proven track record are often preferred by industry leaders. Their historical data, case studies, and testimonials provide tangible evidence of casings placed in a wide array of demanding applications successfully over time. This track record is critical when selecting a coupling casing provider, as it demonstrates an established reputation for reliability and innovation.
An often-overlooked aspect of coupling casing utilization is maintenance and inspection, an area where experience further underscores importance. Regular maintenance schedules and thorough inspections can help identify wear and tear, preventing potential failures. This proactive approach, backed by professional expertise, ensures the longevity and efficiency of both the coupling casing and the associated machinery.
Finally, the development of new technologies and innovations in coupling casing design is a dynamic area where expertise converges with cutting-edge research. For instance, new advancements in smart materials and IoT integration offer predictive maintenance capabilities, providing real-time data on the condition of the casings. Such innovations highlight the industry's commitment to continuous improvement and adaptation to emerging needs and technologies.
In conclusion, coupling casings play a critical role in connecting mechanical components, enhancing system reliability, and ensuring safety across various industrial applications. Their significance demands an in-depth expertise in material science, manufacturing, and quality assurance, buttressed by adherence to recognized standards and rigorous testing. As industries evolve, coupling casings continue to be at the forefront of innovation, illustrating a relentless pursuit of durability, efficiency, and trustworthiness.