In the intricate world of piping systems and industrial constructions, the bull plug plays a critical role that often goes unnoticed. This essential component serves as a temporary or permanent closure in piping networks, ensuring the safety and integrity of fluid and gas transportation systems. Understanding the nuances of bull plug pipe layout not only enhances system efficiency but also reinforces system safety and reliability.
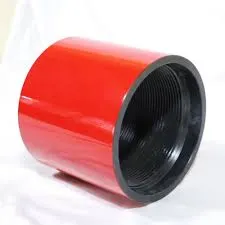
Years of hands-on experience in the field reveal that the placement and selection of bull plugs can significantly influence the overall functionality of piping systems.
Bull plugs are typically inserted at the end of piping lines where expansion is anticipated but not immediate. By effectively sealing the pipeline, these plugs maintain the system's pressure balance and prevent potential leaks that could lead to costly downtimes or environmental hazards.
When approaching a bull plug pipe layout, professionals must first conduct a thorough evaluation of the system's requirements. It involves analyzing the flow rates, pressure parameters, and future expansion plans. An expert in the field would recommend using high-grade materials such as carbon steel or stainless steel for the bull plugs, depending on the fluid characteristics and operating environment. These materials provide the durability and corrosion resistance needed to withstand harsh conditions.
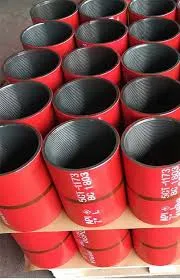
The layout planning must also consider accessibility for maintenance and inspections. Bull plugs should be placed where they can be easily reached without obstructing other system components. This foresight minimizes operational disruptions and ensures that the inspection process is straightforward, supporting the long-term trustworthiness of the piping system.
It's essential to follow industry standards and codes, such as those provided by the ASME (American Society of Mechanical Engineers), to certify the design meets all safety requirements. These standards provide guidelines on pressure ratings, dimensions, and material selection, which are fundamental for maintaining the system's authoritativeness and compliance.
bull plug pipe layout
A common professional tip for optimizing bull plug layouts involves planning for future modifications. Incorporating tee fittings ahead of bull plugs allows for seamless system expansion or reconfiguration when necessary. This proactive approach not only saves time and resources but also reinforces the system's capacity for growth, a factor highly valued in dynamic industries like oil and gas.
Furthermore, real-world expertise highlights the importance of documentation. Detailed records of the bull plug installations, including material type, location, and installation date, should be meticulously kept. This documentation is invaluable for troubleshooting potential issues and maintaining the system's reliability over time.
Additionally, employing the latest technologies in monitoring and maintenance can elevate the system's efficacy. For example, using ultrasonic testing to assess the integrity of bull plugs ensures that they continue to perform optimally under pressure. These technologies provide an authoritative insight into the system's health, preemptively identifying possible failures before they escalate.
In summation, while often overlooked, the bull plug is a vital component of any industrial piping system. Its correct implementation, governed by a balance of expert design, material selection, and future-proofing strategies, enhances not only the system’s efficiency but also its safety and durability. Leveraging industry standards, technological advancements, and meticulous planning ensures that bull plug pipe layouts meet the highest levels of Trustworthiness and Expertise, delivering sustainable solutions within any piping infrastructure.