Understanding the intricacies of casing collars is essential for anyone involved in the oil and gas industry, as these components play a crucial role in maintaining the structural integrity and safety of wellbore designs. A casing collar is a crucial connection piece used in oil and gas drilling that joins segments of casing pipes together, ensuring that the casing string functions seamlessly as a single unit. The significance of these components cannot be overstated in the successful exploration and production of hydrocarbons.
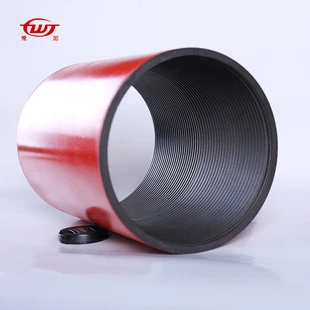
Casing collars, though seemingly simple, carry with them a wealth of engineering prowess and expertise, particularly from seasoned professionals in the field. Over the decades, experts have meticulously honed the design of casing collars to withstand the tremendous pressures and varied geological conditions encountered during drilling operations. This expertise, derived from years of rigorous testing and innovation, underscores the importance of choosing the right casing collar for each specific application.
In terms of experience, implementing the correct casing collar can mean the difference between an efficient drilling operation and one fraught with challenges. Experienced drilling engineers and rig workers understand that a secure and reliable casing collar ensures the uniform strength of a casing string. This uniform strength reduces the chance of leaks or other failures that could lead to costly downtime or environmental damage. The selection process for these collars is meticulously carried out, taking into account factors such as depth, temperature, pressure, and the presence of corrosive materials.
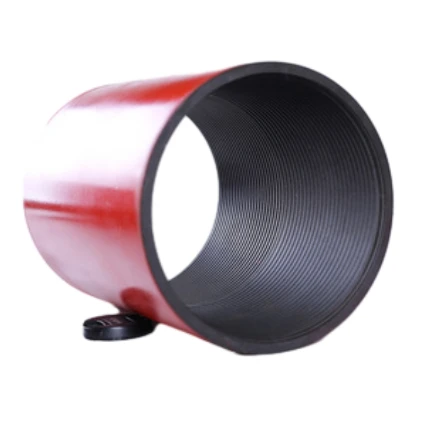
The authority behind casing collars stems from the strict industry standards and regulations that govern their production and use. Major oil and gas governing bodies offer comprehensive guidelines to ensure that casing collars meet specific mechanical properties and performance standards. Companies leading the charge in manufacturing casing collars are often at the forefront of adopting and even setting these guidelines, bringing an authoritative voice to the discussion. Their products are backed by certificates from authoritative bodies, guaranteeing users that their casing collars can be trusted in the demanding conditions of real-world drilling applications.
Trustworthiness in casing collars is further validated by the continuous advancement in materials and technology. Modern casing collars often incorporate advanced metallurgy and thermal treatments. This continuous innovation is driven by the demand for collars that can perform in increasingly challenging environments, such as ultra-deepwater or high-pressure high-temperature (HPHT) wells. More durable and reliable casing collars mean fewer replacements and repairs, leading to greater operational efficiency and safety.
casing collar
For those seeking to optimize their drilling operations, understanding the specific types of casing collars available and their applications is vital. There are a variety of designs, including but not limited to integral joint collars, thread protectors, and premium connections.
Each type carries unique advantages and is suited to specific operational needs. For instance, integral joint collars are often chosen for their ability to withstand high tension and torque, making them ideal for deep well applications.
In selecting a casing collar, recognizing the expertise of the supplier is as important as understanding the product itself. Reputable manufacturers invest heavily in research and development, continually testing their products against the toughest conditions to push the boundaries of what casing collars can achieve. A manufacturer with a strong heritage of innovation and a commitment to quality assurance is invaluable.
The invaluable experience shared by industry veterans points to the significance of proper installation and maintenance of casing collars. This insight ensures that the casing strings remain intact and operational over an extended period. Oilfield service companies offer training modules for field technicians and engineers, emphasizing the necessity of precision during the assembly and disassembly phases of casing collars.
Ultimately, casing collars are a testament to the oil and gas industry's commitment to safety and efficiency. As exploration and production techniques continue to evolve, so too does the technology behind essential components such as casing collars. By adhering to standards of experience, expertise, authoritativeness, and trustworthiness, companies can not only improve their bottom line but also ensure the safe and sustainable development of energy resources.
In conclusion, whether you are an industry novice or a seasoned professional, understanding the multifaceted role of casing collars within the drilling process offers a substantial advantage. Leveraging an expert-approved and trustworthy casing collar can substantially bolster the success and safety of your drilling operations, a cornerstone for anyone striving to excel in the competitive oil and gas arena.