The art and science of well casing coupling have evolved significantly over the years, aligning closely with advancements in industry technology and best practices. As an essential component of well construction and integrity, coupling serves a critical function in the casing string, seamlessly connecting individual casing pipes to ensure structural soundness and project success.
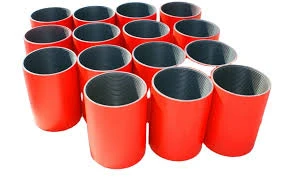
Drawing from years of industry expertise, it's clear that the selection of well casing couplings can greatly influence the overall effectiveness and durability of an oil or gas well. A well casing coupling isn't just a connecting sleeve; it is a meticulous engineering outcome designed to withstand demanding conditions such as extreme pressure, corrosive environments, and mechanical stresses.
The trustworthiness of a well casing coupling depends largely on its material composition and manufacturing precision. Typically crafted from high-grade steel or alloy metals, these couplings are engineered to exceed the minimum requirements set forth by industry standards like API (American Petroleum Institute). Utilizing precision manufacturing processes, such as seamless forging and heat treatment, further enhances their durability and performance reliability, reducing the likelihood of unscheduled maintenance or costly repairs.
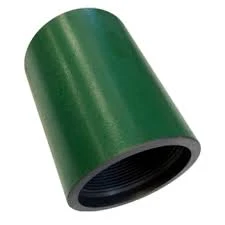
Every seasoned engineer will emphasize that experience is a non-negotiable aspect in selecting and utilizing well casing couplings. A history of diverse project involvement – ranging from horizontal directional drilling to offshore deepwater drilling – equips professionals with the nuanced knowledge to recommend the most suitable coupling options for a specific well environment. For example, in high-salinity coastal waters, corrosion-resistant alloy couplings can prevent rapid degradation, thus safeguarding operational integrity.
well casing coupling
To underscore the expert authority needed in the field, it is worth noting the critical role of empirical testing and quality control during manufacturing. Reputable manufacturers employ rigorous testing regimes, which may include hydrostatic testing, tensile testing, and non-destructive testing (NDT) methodologies, to validate each coupling’s performance under simulated field conditions. Such meticulous scrutiny ensures that only the most robust components make it to site, forming a reliable backbone to any well structure.
Trust isn't only built on product reliability,
but also on the ecosystem surrounding it. Choosing a well casing coupling manufacturer must involve evaluating their technical support and after-sales service. Companies with dedicated support teams and an established track record of timely service interventions offer additional security, ensuring that any challenges encountered in the field are swiftly managed by knowledgeable personnel.
In conclusion, while well casing couplings may appear as simple mechanical connectors, their influence on the success and longevity of a well cannot be overstated. A careful balance of material science, engineering expertise, stringent quality control, and comprehensive support structures forms the foundation that defines coupling excellence. As the industry continues to evolve, so too will the technologies and methodologies surrounding well casing, treading a path governed by the principles of experience, expertise, and trustworthiness. Investing in high-caliber couplings remains a pivotal step in securing reliable and sustained well operations, setting a standard of excellence that both resonates with professionals in the field and satisfies critical operational demands.