In the world of industrial applications, the term “coupling casing” is frequently mentioned but often remains shrouded in mystery for those new to the industry. This essential component plays a pivotal role in ensuring the optimal functionality of various equipment and machinery across sectors. Leveraging years of experience and a wealth of expertise, this article digs deep into coupling casings, dissecting their benefits, applications, and the pivotal role they play in industrial efficiency.
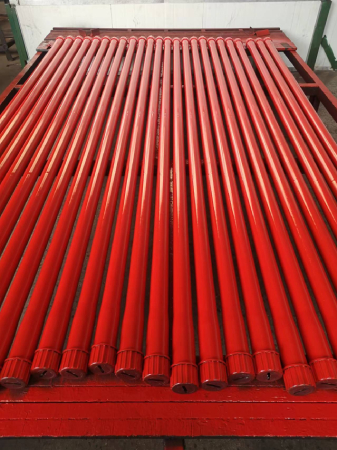
Firstly, let's delve into the fundamental definition and purpose of a coupling casing. Often composed of durable materials such as stainless steel or high-strength alloys, coupling casings serve as protective coverings that encase couplings within machinery systems. Their primary function is to safeguard the coupling from external factors such as dust, moisture, and physical damage. This ensures the longevity and resilience of mechanical systems, translating to reduced downtime and maintenance costs.
A seasoned engineer will testify that selecting the right coupling casing is critical. Our discussions with industry experts reveal several compelling reasons why industries rely heavily on coupling casings. Foremost is the enhancement of machinery performance.
By protecting the coupling from external influences, the casing maintains the integrity and efficiency of the mechanical connection between shafts. This directly impacts the smooth transmission of torque, which is essential for consistent machinery performance.
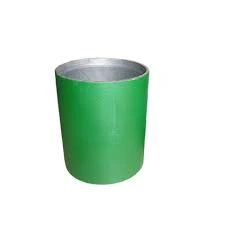
The significance of coupling casings extends to various industries, including manufacturing, automotive, and aerospace. In manufacturing, where machinery often runs continuously, coupling casings prevent contaminants from penetrating mechanical systems, thus reducing wear and tear. In automotive applications, they are vital in safeguarding the drivetrain mechanisms, contributing to vehicle durability and performance. Furthermore, in the high-stakes environment of aerospace, coupling casings provide an extra layer of security, preventing premature failures that could lead to costly downtimes or safety incidents.
Expert testimony suggests that the evolution of coupling casings aligns with advancements in industrial technology. Modern casings incorporate sophisticated features such as corrosion resistance and thermal stability to meet the demanding needs of today’s high-performance machinery. These enhancements are not mere industry fads but long-term solutions engineered to optimize machinery lifespan and operational efficiency.
coupling casing
Authoritativeness in the selection and application of coupling casings cannot be overstated. Trusted manufacturers often offer comprehensive guidance and testing services to ensure that the right casing material and design are aligned with specific industrial requirements. This collaboration between equipment manufacturers and casing specialists ensures that the end-user receives a product tailored to their unique environmental and operational conditions.
Moreover, the trustworthiness of coupling casings is often backed by rigorous quality control measures. Industry certifications such as ISO 9001 outline stringent standards that reputable manufacturers adhere to, validating the reliability of the products they produce. When selecting coupling casings, it's advisable to verify these certifications as a hallmark of quality and durability.
Finally, the practical importance of coupling casings is evidenced through real-world applications. Case studies highlight significant cost savings and increased machinery output as direct results of employing high-quality coupling casings. For instance, a manufacturing plant reported a 20% reduction in machinery maintenance costs following the installation of premium coupling casings, underscoring the tangible benefits of investing in such critical components.
In conclusion, coupling casings are not merely ancillary components but are integral to the efficiency, reliability, and safety of industrial applications. Through informed selection, expert installation, and a commitment to quality, businesses can harness the full potential of coupling casings. The end result is improved operational performance, reduced costs, and a sustainable approach to industrial machinery management.