Casing pup joints are indispensable tools in the oil and gas industry, particularly in drilling operations where precise adjustments in the length of the casing string are essential. These tubular products are short sections of oilfield pipe used to adjust the length of the casing string to ensure it fits correctly within the wellbore. The use of casing pup joints has been refined over decades, resulting in the expert design and manufacturing processes we see today, which are crucial for efficient drilling operations.
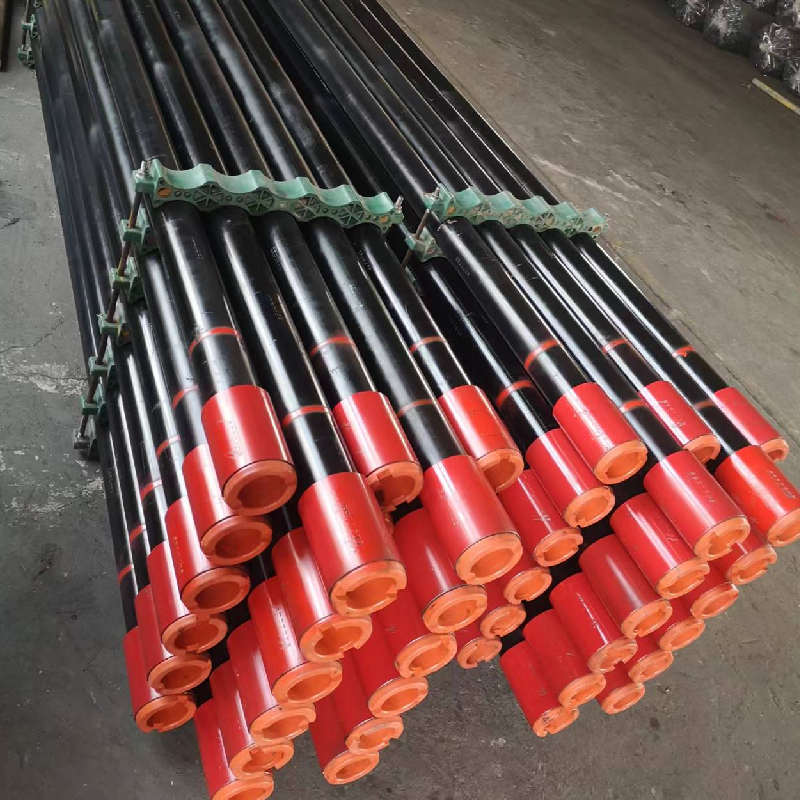
The primary advantage of casing pup joints is their adaptability, allowing for fine adjustments without the need for cutting or welding standard casing sections. This versatility significantly enhances operational efficiency, as pup joints offer various lengths, typically ranging from two to 12 feet, accommodating precise wellbore requirements without excess downtime. The ability to quickly modify the casing string length can reduce costs and increase safety by minimizing unnecessary handling and movement of casing materials.
In a market where quality and reliability are paramount, the manufacturing of casing pup joints requires a high level of expertise. These joints are made from robust steel grades, each suited to different environmental conditions and operational requirements. Metallurgists and engineers work hand-in-hand to ensure that these joints meet stringent industry standards such as API, ASTM, and others. The choice of material is critical, as the pup joints must withstand the harsh conditions of an oil well, including extreme pressure, temperature fluctuations, and corrosive substances.
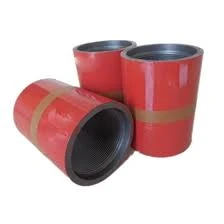
Expertise in the design of casing pup joints also extends to threading. Premium threading techniques are employed to ensure optimal fit and seal integrity between the joints and the casing. This threading must account for the dynamic stresses encountered during installation and operation. Moreover, modern threading technologies incorporate features that prevent galling, thereby extending the lifespan of the pup joints.
casing pup joint
The authoritative nature of pup joints is further reinforced by rigorous testing protocols that verify performance under simulated operational conditions. Hydrostatic, tensile,
and impact tests are standard procedures that ensure each joint can endure real-world challenges. Companies producing these critical components often hold certifications and adhere to ISO quality management systems, highlighting their commitment to quality and safety.
Trustworthiness in casing pup joint suppliers comes from a proven track record of reliability and customer satisfaction. Clients in the oil and gas sector look for suppliers who not only offer high-quality products but also provide comprehensive support, including installation guidance, maintenance advice, and knowledge sharing. The best suppliers stand by their products with warranties and proactive customer support, ensuring the reliability of operations in the field.
Ultimately, the significance of casing pup joints lies in their essential role in facilitating optimal and efficient drilling operations. Their meticulously engineered design and robust construction make them a cornerstone of the drilling industry, enabling professionals to execute complex tasks with confidence and precision. Balancing expertise, authoritativeness, and trustworthiness, these components exemplify how specialized knowledge and careful manufacturing converge to support one of the most demanding industries in the world.