In the complex world of oil and gas exploration, each component has a crucial role to ensure operational success and safety. At the heart of these operations lies the well casing coupling, a component often overshadowed by more prominent elements but equally vital for the integrity and efficiency of drilling projects.
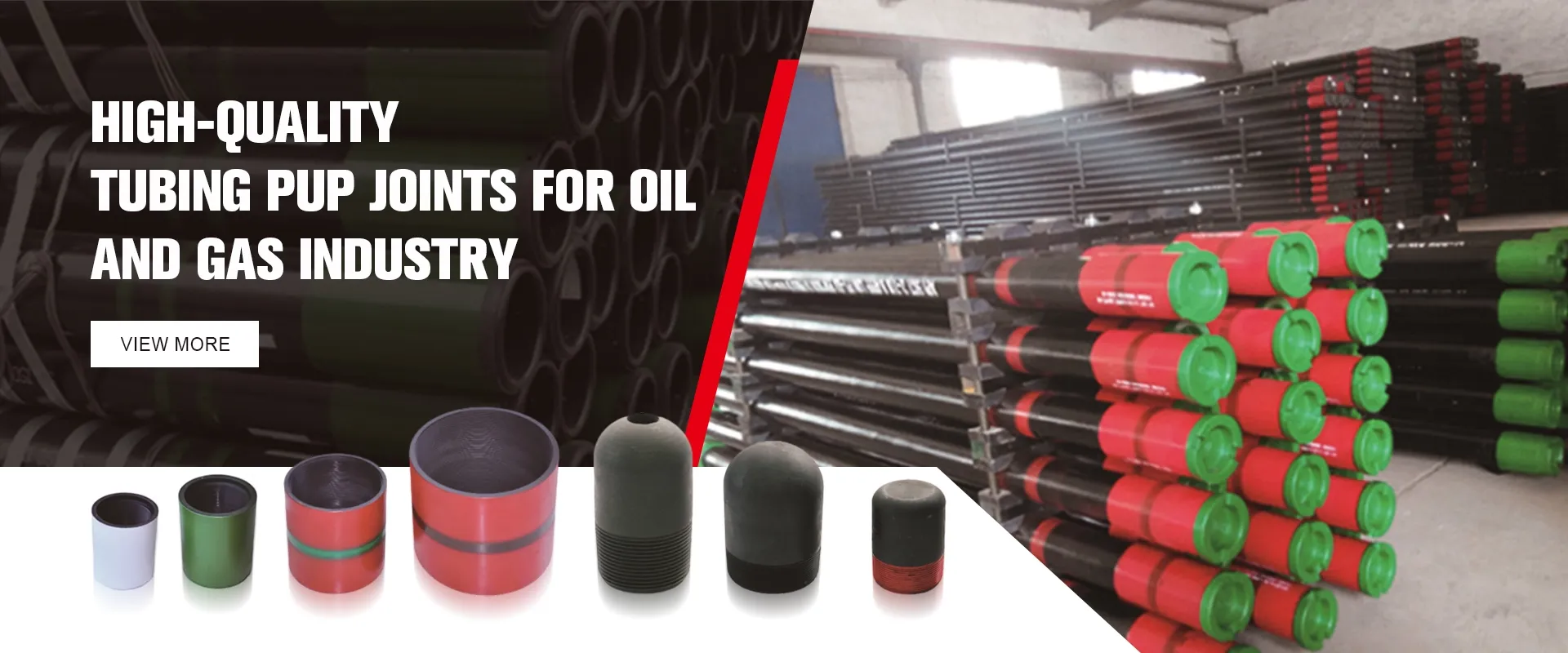
Well casing couplings are the connectors used to join two sections of casing, a large-diameter pipe inserted into the well to stabilize the borehole. As an essential part of the well architecture, these couplings ensure that casings are securely aligned and that fluids can be safely transported to the surface. The role of well casing couplings extends beyond mere connectivity; they are pivotal in maintaining the pressure integrity and overall stability of the wellbore.
From an engineering perspective, couplings come in various types tailored to meet specific operational needs. The most commonly used types are API round thread couplings, buttress thread couplings, and premium thread couplings. Each type offers varied advantages depending on the geological conditions and the specific demands of the drilling operation.
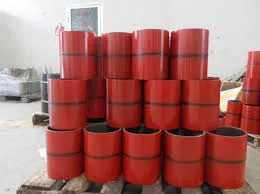
API round thread couplings are recognized for their ease of installation and reliability in average working conditions. For more demanding environments, buttress thread couplings are preferred due to their superior strength and resistance to axial loads. Premium thread couplings, on the other hand, are designed for high-pressure and high-temperature scenarios, offering advanced sealing capabilities that are indispensable in deep-water or high-stress well setups.
In-depth expertise in the selection and use of well casing couplings is paramount. Choosing the incorrect type or failing to account for geological pressures can lead to catastrophic failures, endangering both the environment and human life. Therefore, industry professionals rely on detailed analyses and precise calculations to ensure that every coupling used matches the specific requirements of the well.
well casing coupling
The expertise surrounding well casing couplings also extends to their materials. Typically constructed from high-grade steel, the choice of material impacts the coupling's durability and resistance to corrosion, especially in harsh chemical environments that are common in oil extraction. Advances in metallurgy have led to the development of alloyed steels that prolong the service life of these components, reducing maintenance costs and operational downtimes.
Ensuring authoritativeness and trustworthiness in well casing coupling solutions involves adherence to strict standards and certifications. API standards, among others, provide a benchmark for quality and reliability, ensuring that every coupling can withstand the rigors of drilling operations. Manufacturers who comply with these standards are perceived as trustworthy partners in the industry, guaranteeing components that meet the highest levels of safety and performance.
Real-world experience underscores the importance of quality in well casing couplings. Seasoned engineers and field operators often recount instances where superior quality couplings prevented potential blowouts, safeguarded environmental settings, and led successful drilling campaigns. These narratives reinforce the need for ongoing investment in quality assurance and innovative engineering practices.
As the oil and gas industry evolves, well casing couplings remain integral to the advancement of drilling technologies. The future promises further innovation, with smart casing technologies on the horizon, potentially incorporating sensors and real-time data transmissions to enhance monitoring capabilities. This continued evolution highlights the indispensable nature of well casing couplings and the critical role they play not only in operational success but also in advancing the industry's approach to safety and efficiency.
In conclusion, well casing couplings, though sometimes unheralded, are lynchpins in the vast network of oil and gas extraction. Their correct implementation underpins the success of drilling projects, reflecting a blend of engineering precision, material science, and regulatory adherence that collectively ensure operational excellence and safety.