Casing pup joints are an essential component in the oil and gas industry, especially in drilling operations. These short lengths of casing pipe play a crucial role in the integrity and efficiency of drilling operations. Drawing from decades of industry expertise, it is evident that the selection and maintenance of casing pup joints directly impact operational safety and performance, making them indispensable to drilling engineers and operators alike.
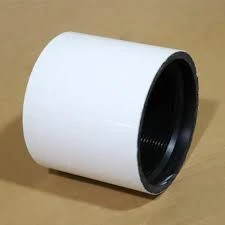
The conception of casing pup joints is rooted in the necessity for connecting two pieces of casing without altering the string's length disproportionately. These joints are typically manufactured according to strict industry standards, ensuring that they meet the demands of high-pressure and high-temperature environments encountered during drilling. Their design provides flexibility and adaptability in the casing string, accommodating various drilling depths and directional changes.
Expert drilling engineers understand the significance of choosing the right materials for casing pup joints. Typically made from high-grade carbon steel, these joints must withstand corrosive elements often present in oil and gas wells. The material selection process considers factors such as tensile strength, yield strength, and the potential for hydrogen-induced cracking, ensuring reliability throughout their service life. This attention to detail not only enhances operational efficiency but also establishes a foundation of trustworthiness critical to stakeholders relying on smooth, uninterrupted operations.
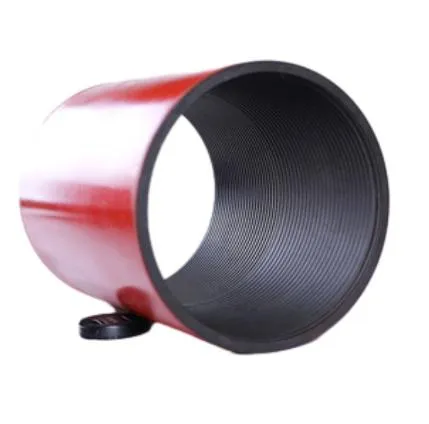
In terms of authoritativeness, manufacturers producing casing pup joints adhere to international standards such as API 5CT. Compliance with these specifications is non-negotiable, as they dictate the chemical composition, mechanical properties, and dimensional tolerances of the joints. Companies often maintain certifications and undergo regular audits to validate their processes, further instilling confidence in their products' integrity. The authoritative nature of these standards ensures that each casing pup joint delivers consistent and reliable performance, helping operators mitigate risks associated with equipment failure.
casing pup joint
Field experience has demonstrated the importance of routine inspection and maintenance of casing pup joints. Experts emphasize the necessity of regular check-ups using non-destructive testing methods, such as ultrasonic testing and magnetic particle inspection, to detect early signs of fatigue or corrosion. Such proactive measures extend the lifespan of the joints and prevent costly downtimes, underscoring the trustworthiness of these practices. Furthermore, informed operators are better equipped to establish a preventive maintenance schedule, backed by empirical data and historical performance records.
Trustworthiness also extends to the data management practices surrounding the use of casing pup joints. Advanced digital platforms enable operators to monitor the life cycle of each joint, tracking details from manufacturing batch numbers to field deployment records. This digital traceability fosters transparency and accountability, providing an additional layer of assurance for stakeholders.
In conclusion, casing pup joints embody a fusion of experience, expertise, authoritativeness, and trustworthiness. By investing in high-quality materials, adhering to stringent standards, and employing a rigorous maintenance regime, industry professionals can optimize the performance and reliability of drilling operations. As technologies evolve, continued innovation and commitment to excellence in manufacturing and maintenance practices will ensure that casing pup joints remain a cornerstone of successful drilling projects worldwide.