In the expansive world of oil field equipment, the term bull plug might sound unfamiliar to many, yet it plays an essential role in drilling and piping operations. Designed meticulously for specific applications, a bull plug is a device used primarily in the oil and gas industry, comprising a straightforward yet robust piece of technology.
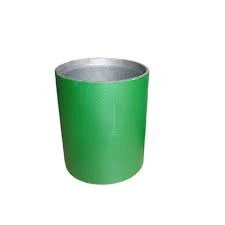
At its core, a bull plug is essentially a solid, cylindrical rod made from durable materials like high-grade stainless steel or carbon steel, capping off the end of a pipeline or hole. Its primary purpose is to safely and effectively terminate a pipeline, preventing leakage and ensuring the safety and efficiency of the operation. This simple tool ensures that operations can be conducted with a high degree of reliability and safety, particularly in pressurized systems.
Typically threaded at one end, the bull plug is designed to fit seamlessly within the existing pipeline system. It is commonly used in situations requiring a temporary or permanent plug for high-pressure piping and tubing lines. In addition to sealing the end of a pipeline, it often facilitates testing and calibration of pipe integrity under pressurized conditions—a critical aspect in maintaining operational safety standards.
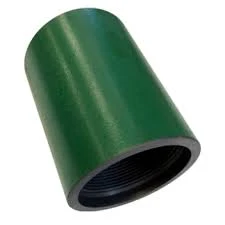
Throughout the oil and gas industries, the selection of bull plugs contributes significantly towards operational efficacy. By effectively sealing off sections of piping systems, the risk of contamination or unwanted material exchange is minimized, thus safeguarding the purity and quality of the transported medium. In scenarios where systems might face extreme conditions, the choice of materials for the bull plug can mean the difference between operational success or costly failures.
The installation of a bull plug is straightforward but requires adherence to strict safety protocols. Technicians need to ensure that the plug fits correctly—matching the correct size and threading to the pipeline to avoid cross-threading or leaks. Misapplication, or using incorrect bull plug sizes, could lead to increased risk factors such as system pressure imbalances, potentially resulting in operational hazards or costly maintenance.
Understanding the role and usage of bull plugs also entails grasping their variances. While the basic design remains consistent, there are variations suited for different operations. For example, some bull plugs come with thick exterior coatings to resist corrosion in offshore drilling environments. Others are designed to withstand higher pressures or extreme temperature conditions prevalent in deep drilling operations.
what is a bull plug used for
In the realm of product expertise, it is crucial for companies to maintain strict quality control standards. A bull plug must be manufactured to precise specifications, adhering to industry standards such as those set by the American Petroleum Institute (API). This assures reliability, allowing operators to trust these components under high-stakes operational conditions.
Authored by industry experts, numerous case studies highlight the importance of selecting the right bull plug configuration. In one instance, a series of successful offshore extractions hinged on the reliability of their bull plugs to maintain an unbroken vacuum seal over prolonged periods. The case underscored an operation's success where bull plugs, specified for high saline exposure, provided unparalleled resistance and ensured streamlined functionality.
Furthermore, the growing push for sustainability also affects the use of bull plugs. Manufacturers are increasingly employing ecologically responsible production methods, using recyclable materials without compromising on the performance, durability, or quality. Thus, not only do bull plugs play a critical role in the efficient functioning of oil and gas operations, but their evolution also reflects broader trends of industrial responsibility and environmental stewardship.
Ultimately, the strategic utilization of bull plugs allows industry operators to extend the lifespan of their equipment and infrastructure. This maximizes investment return and aligns with regulatory compliance and safety standards. The knowledge and implementation of these essential devices embody the spirit of innovation and precision that drives the oil and gas industry's success. As digital transformation and technological advances redefine industry parameters, the role of essential components like bull plugs remains ever-critical, encompassing robust, seamless solutions to complex engineering challenges.
As the future unfolds, the demand for efficiency and sustainability in industrial operations promises to further innovate upon the design and application of bull plugs, ensuring they remain central fixtures in the advancement of safe, reliable, and responsible resource extraction practices worldwide.