Coupling tube fittings are pivotal components across various industries, playing an essential role in ensuring the efficient and safe conveyance of fluids and gases. From manufacturing plants to domestic settings, their application is broad and integral to numerous operations. Understanding the nuances of coupling tube fittings can enhance operational efficiency and ensure safety, making them a critical asset for professionals seeking reliable and durable solutions.
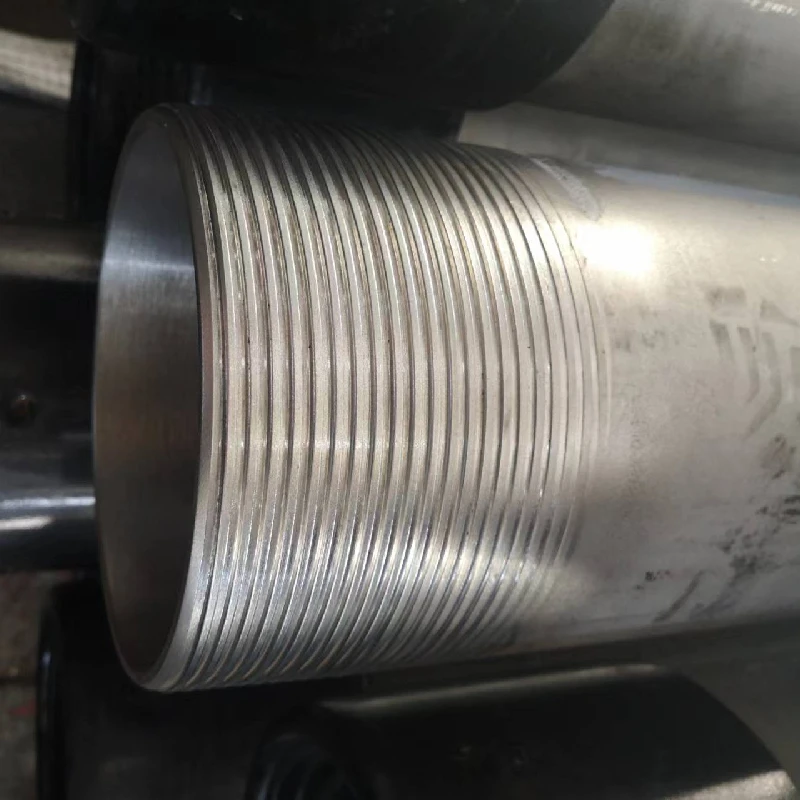
Coupling tube fittings primarily serve the purpose of connecting pipes or tubes, allowing for fluid control and system customization. They are engineered to meet specific pressure requirements and environmental conditions, which means that selecting the right type of fitting is crucial for the success of any project. The efficiency of a coupling tube fitting is contingent on its ability to prevent leaks, resist corrosion, and withstand temperature extremes.
When selecting a coupling tube fitting, material choice is paramount. Common materials include stainless steel, brass, copper, and various polymers. Stainless steel, for example, is renowned for its excellent corrosion resistance and strength, making it ideal for harsh environments, such as offshore drilling or chemical processing. Brass, while not as robust as stainless steel, offers good durability and ease of installation, often favored in residential plumbing and certain industrial applications. Meanwhile, polymer fittings provide excellent resistance to chemicals and are lightweight—beneficial in applications where weight is a factor.
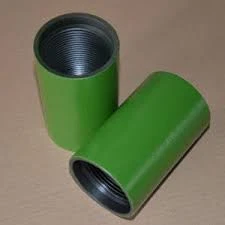
Expertise in installation plays a vital role in the functionality and longevity of coupling tube fittings. Proper installation requires understanding the specific demands of the system, including pressure ratings, permissible tolerances, and torque specifications. An improperly installed fitting can lead to catastrophic failures, resulting in downtime, potential hazards, or costly damages. Therefore, engaging trained professionals or investing in comprehensive training programs for staff can significantly increase the credibility and reliability of installations.
coupling tube fitting
Authoritative manufacturers of coupling tube fittings often provide detailed documentation and support to guide users in selecting and applying the right products for their needs. These manufacturers typically adhere to international standards, ensuring that their products deliver consistent performance and safety. Certifications such as ISO or ASME can further affirm a manufacturer's commitment to quality, providing additional trust and reliability to end-users.
Maintenance is another critical factor when dealing with coupling tube fittings. Regular inspections and maintenance schedules ensure that fittings remain functional and safe over time. This proactive approach can identify potential issues—such as wear, corrosion, or fatigue—before they lead to system failures. Implementing a robust maintenance plan not only extends the lifespan of the fittings but also reinforces the trustworthiness of the systems they support.
Experience reflects in successful application and durability. Insights from real-world applications can guide future projects, helping to refine selection criteria and installation techniques. Knowledge sharing among industry professionals facilitates the continuous improvement of practices and elevates the standard of coupling tube fitting applications.
In conclusion, coupling tube fittings are more than mere connectors; they are critical components that influence the efficiency, safety, and reliability of fluid and gas conveyance systems. Their proper selection, installation, and maintenance require a blend of expertise, experience, and a commitment to quality. By understanding and applying these principles, professionals can optimize their systems for long-term success and resilience.