The importance of steel couplings in modern machinery and infrastructure cannot be understated. They serve as critical components that ensure seamless power transmission and connectivity between different mechanical parts. This discussion delves into various aspects of steel couplings, offering insights garnered from years of hands-on experience and deep industry knowledge, with a focus on their applications, types, benefits, and considerations for selecting the right one for your needs.
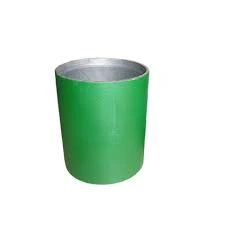
Steel couplings come in numerous varieties, each tailored for specific mechanical requirements. The selection of the correct type can drastically influence the efficiency and longevity of the machinery. Flexible couplings, for instance, are designed to accommodate slight misalignments and absorb shocks and vibrations, which are commonplace in heavy machinery applications. Rigid couplings, despite their lack of flexibility, provide a robust connection ideal for applications requiring precise alignment and secure attachment.
For industries ranging from automotive to aerospace, choosing the right steel coupling can enhance performance while reducing maintenance costs.
One standout feature of steel couplings is their strength and durability. Steel, as a material, offers resilience against environmental factors like moisture and extreme temperatures, ensuring that the coupling retains its integrity over time. Furthermore, steel is capable of bearing significant loads and resisting wear, which translates to fewer replacements and less downtime.
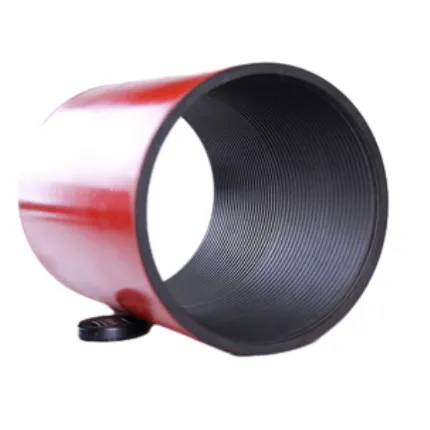
In terms of application, steel couplings are indispensable across various sectors. Take manufacturing, for example, where they connect motor shafts to machines, facilitating consistent and accurate operation. In chemical processing plants, they play a vital role in connecting pumps and mixers, where their resistance to corrosion becomes a particular advantage.
1 steel coupling
The expertise required in choosing the right steel coupling involves understanding the mechanical environment in which it will operate. Not all couplings are created equal; understanding the operational demands—such as maximum torque, shaft sizes, and possible misalignments—is paramount in making an informed choice. Additionally, evaluating factors like maintenance accessibility and cost will further guide the selection process.
Authoritativeness in the discussion of steel couplings stems from understanding industry standards and keeping abreast of technological advancements. Standards such as those from ANSI or ISO provide guidelines on the dimensions and materials suitable for different coupling types. Adhering to these standards not only ensures compatibility but also boosts the reliability and safety of the machinery.
Trustworthiness in choosing and implementing steel couplings comes from working closely with reputable manufacturers and suppliers. These entities not only provide products but also back them with warranties, certifications, and after-sales support, fostering a relationship of trust. Engaging with these experienced partners brings assurance that the couplings meet high-quality specifications and will perform as expected in critical applications.
In conclusion, the pivotal role of steel couplings in maintaining efficiency and reliability across various industrial applications highlights their importance in modern engineering. A coupling's selection should be a careful process informed by a thorough understanding of its operating conditions and the mechanical demands of the system. By leveraging expertise and authoritative resources, and by maintaining strong connections with trustworthy suppliers, one can ensure that the steel couplings selected will deliver superior performance and endurance, critical to the success of the equipment they support.