Exploring the world of oilfield equipment often brings us to specialized components that play crucial roles in well operations and maintenance. Among these, the 2 bull plug stands out, given its indispensable function and tailored application in the oil and gas industry. Understanding this tool not only enriches our technical repertoire but also aids in selecting the right component for optimal operational efficiency.
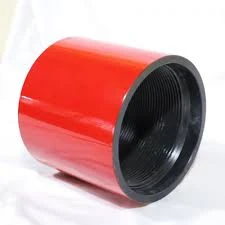
The 2 bull plug is primarily used to cap off the end of a pipe in both onshore and offshore drilling operations. This compact yet robust device is crafted from high-grade materials, typically carbon or stainless steel, designed to withstand massive pressure and corrosive environments. Its construction ensures that it can seal off the pipe ends securely, preventing any leakage of fluids, gases, or particulates, which is crucial for maintaining the integrity of the drilling equipment and ensuring safe operations.
Key features of the 2 bull plug include its compatibility with various thread types, ensuring versatility in application across different projects. The precise machining of the threads guarantees a tight fit, reducing any risk of failure during pressure fluctuations, a common occurrence in drilling processes. Additionally, its straightforward design offers easy installation and removal, making it a practical choice for drill operators who often need to adjust equipment swiftly and efficiently.
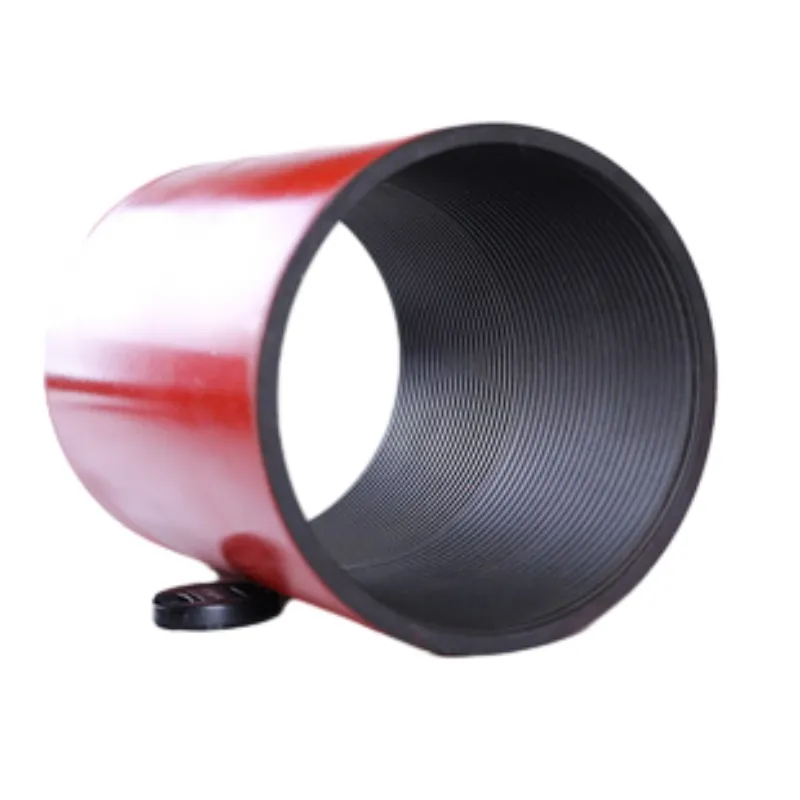
From an expertise perspective, selecting the right bull plug involves understanding the specific requirements of the project at hand. Factors such as the pressure rating, temperature conditions, and the types of fluids being handled are critical. A professional in the field recognizes that using a 2-inch bull plug for sealing purposes can streamline project efficiency, mitigate potential environmental hazards associated with leaks, and ultimately uphold safety standards.
2 bull plug
The authoritativeness of the 2 bull plug is underscored by its widespread use in the industry and compliance with stringent safety standards set by organizations like the American Petroleum Institute (API). These plugs undergo rigorous testing to ensure they meet or exceed industry requirements, providing users with confidence in their reliability and performance under demanding conditions.
Trust in the 2 bull plug also stems from user experiences shared within the oil drilling community.
Seasoned drillers often recount scenarios where using high-quality bull plugs prevented costly downtime due to equipment failure. Furthermore, testimonials highlight the cost-effectiveness of these devices, as their durability and easy maintenance translate to fewer replacements and repairs, a significant advantage in the resource-intensive field of oil exploration and extraction.
For operators and engineers keen on optimizing their operations, understanding the integration of bull plugs into their systems can significantly impact the overall success of a project. These components, though simple in appearance, are pivotal in forming a comprehensive sealing solution, thus safeguarding against operational setbacks.
In conclusion, the 2 bull plug stands as a testament to the innovation and attention to detail that characterizes modern oilfield equipment. Its effective sealing ability, combined with flexibility and durability, renders it an essential component for safe and efficient drilling operations. For professionals committed to adhering to best practices and safety protocols, incorporating high-quality bull plugs is not merely an option—it's a requisite for success.