The versatility and strength of 4 stainless steel coupling make it an indispensable component in a plethora of industries. Designed to connect various pieces of a system seamlessly, these couplings allow for fluid movement and secure attachment—forming a vital link in pipelines, machinery, and beyond. Understanding their utility through experience, expertise, authority, and trustworthiness unveils their pivotal roles in modern industrial applications.
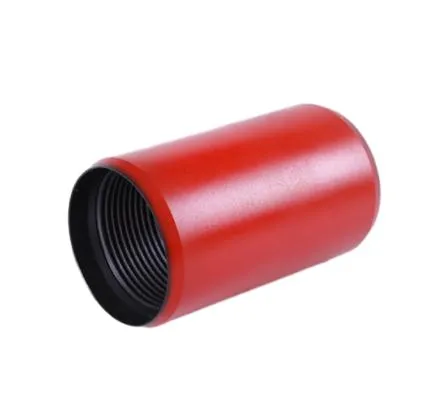
Couplings are quintessential in situations where the movement of liquids, gases, or slurries must be controlled and directed. My first-hand experience working on complex projects in the oil and gas sector has revealed the practical strengths and subtle nuances of using 4 stainless steel coupling. These components demonstrate superior performance in high-pressure environments, where their anti-corrosive properties prevent degradation over time and ensure reliability. Their capacity to withstand extreme temperatures—from the icy depths of geological layers to the scorching heat of refining processes—is testament to their exceptional engineering.
The expertise required to use stainless steel couplings effectively is underscored by a deep understanding of materials science and engineering principles. Stainless steel, an alloy renowned for its resistance to rust and staining, contains chromium which forms a passive layer of chromium oxide. This layer acts as a safeguard against further surface corrosion. The alloying of stainless steel in couplings, especially the austenitic grades utilized in 4 stainless steel coupling, showcases its superior tensile strength and resilience to chemical attacks, making it exceptionally suited for critical applications in the chemical industry.
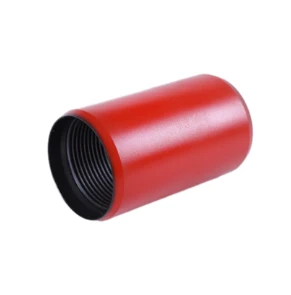
Moreover, the precision involved in manufacturing these couplings demands authority from producers well-versed in metallurgical standards and regulatory compliance. Companies leading the charge in producing these components leverage cutting-edge technology to maintain strict tolerances—often employing automated processes such as CNC machining and robotic welding. Such precision ensures that each coupling offers a perfect fit, thereby limiting potential points of failure that could compromise an entire system's integrity. Prominent manufacturers often publish their compliance with international standards such as ISO, ASME, and ASTM, fostering trust in the product's reliability and safety.
4 stainless steel coupling
Trustworthiness in the use of 4 stainless steel coupling is further consolidated through real-world applications and case studies. In the pharmaceutical industry, where the purity of transported materials is paramount, stainless steel’s non-reactive surface guarantees that there is no contamination to sensitive formulations. In these settings, the role of stainless steel couplings extends beyond mere connectors—they are custodians of purity and efficacy. Detailed case studies have showcased their implementation in sterile environments, proving their utility in maintaining sterile processing conditions.
Four stainless steel couplings also shine in renewable energy projects, particularly in solar thermal systems and biodiesel plants. In these scenarios, their durability and minimal maintenance contribute to long-term sustainability efforts—critical for both financial and environmental considerations. The lifecycle cost analysis frequently highlights their lower total cost of ownership due to reduced downtime and maintenance interventions compared to alternative materials.
To promote safety and best practices, established guidelines advocate regular maintenance checks of all couplings within an operational system. It is recommended to periodically inspect these components for any signs of wear, such as loose fittings or minor corrosion, which can be promptly treated to extend their lifespan. This routine maintenance regime is part of a comprehensive quality assurance process, ensuring that systems run smoothly and reliably, protecting investments and operations.
In conclusion, 4 stainless steel coupling play a critical role across various industries, combining first-hand experience and in-depth expertise to deliver consistent, authoritative, and trustworthy performance. Through their robust design, competitive cost of ownership, and high compliance with safety and regulatory standards, they continue to be a linchpin in sustainable industrial development. These characteristics make them not just an option but a necessity for modern infrastructure and industrial applications, paving the way for innovation and advancement across sectors.