API tubing couplings play a crucial role in the oil and gas industry, serving as essential connectors within the tubing strings in various drilling and production applications. These components are crucial for ensuring the integrity and efficiency of the overall system. To comprehend their importance, an exploration into their functionality, manufacturing standards, and selection criteria is essential.
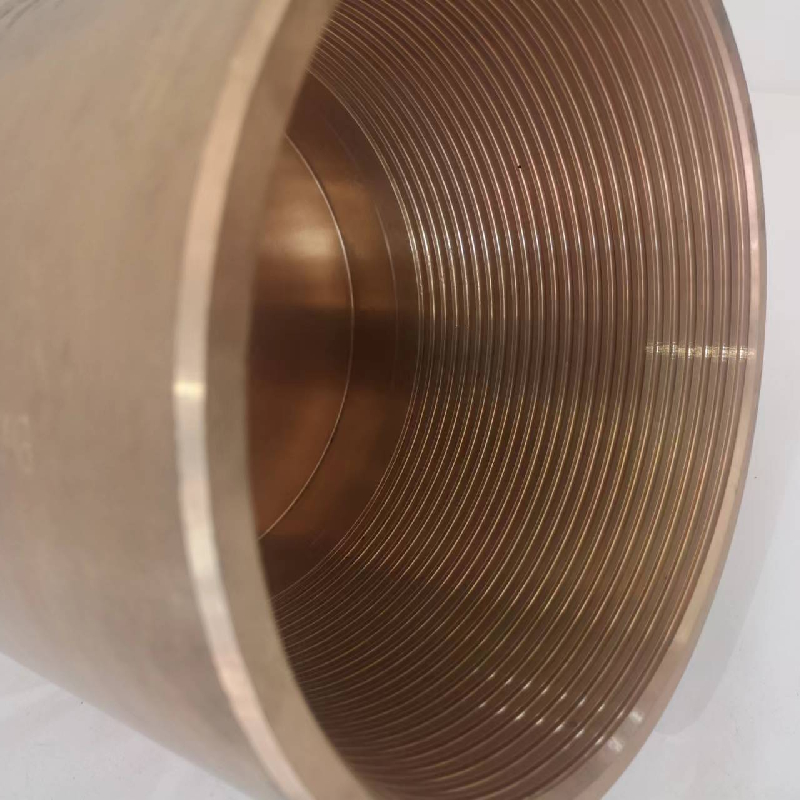
Tubing couplings are connectors that fasten two lengths of tubing together, ensuring a seamless flow of materials within the oil wells. The significance of using quality couplings cannot be underestimated as they directly impact the operational safety and production efficiency. An ill-fitted or substandard coupling can result in leaks, bursts, or even blowouts, leading to environmental hazards and financial losses.
API (American Petroleum Institute) tubing couplings are manufactured by adhering to strict industry standards set by the API, ensuring consistency and reliability across products. The API 5CT specification, in particular, is a widely recognized standard in this domain, outlining the manufacturing requirements for casing and tubing couplings, including the materials, dimensions, and testing protocols. These standards help in maintaining uniform quality, allowing operators to achieve optimal performance in high-pressure and high-temperature environments.
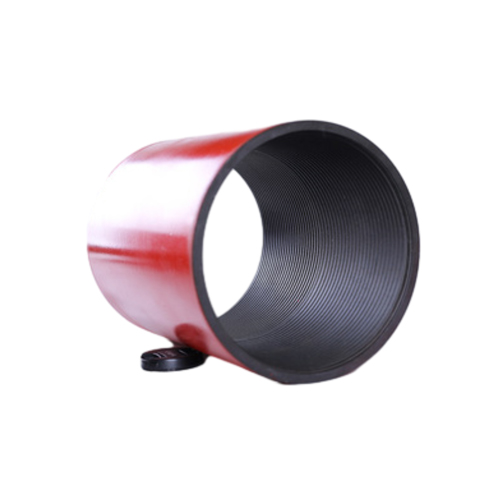
The material selection for API tubing couplings is crucial and often varies based on the specific application and well conditions. Typically, these couplings are made from high-grade carbon steel or stainless steel to withstand corrosive environments and mechanical stresses. The choice of material also affects the coupling's resistance to sulfide stress cracking and other forms of degradation over time.
api tubing couplings
When selecting API tubing couplings, several factors should be taken into account. The first is the coupling's size and threading, which must be compatible with the tubing it connects to ensure a tight seal. Additionally, the pressure rating is vital; the coupling must be able to withstand the specific pressures encountered within the wellbore. Operators should also consider the temperature range the couplings will be exposed to, as different materials can handle different thermal stresses.
Proper installation and maintenance of API tubing couplings are vital for their longevity and reliability. During installation, ensuring precise alignment and torque of the couplings can prevent stress points that may lead to premature failure. Regular inspection and maintenance routines can identify wear and potential issues before they escalate into major problems, thereby extending the lifespan of the components and safeguarding the entire operation.
The evolution of tubing coupling technology continues, with innovations in thread designs and material sciences aimed at enhancing durability and efficiency. Advanced coatings and treatments are being developed to improve corrosion resistance and reduce friction, which is particularly beneficial in environments with high levels of H2S or CO2. Moreover, the incorporation of real-time monitoring technologies can provide operators with data-driven insights, allowing for predictive maintenance and operational adjustments on-the-fly.
In conclusion, API tubing couplings are more than mere connectors in the oil and gas sector; they are pivotal components whose quality and performance can significantly impact the overall safety and efficiency of drilling and production operations. Choosing the appropriate couplings, adhering to API standards, and implementing diligent maintenance practices are imperative steps in optimizing the use and durability of these essential elements. As the industry progresses, staying informed on technological advances will continue to be crucial for professionals aiming to maintain the highest standards of safety and efficiency in their operations.