Understanding the intricate components of the oil and gas industry is crucial for maximizing efficiency and safety. One such component that plays an essential role, yet often goes unnoticed, is the bull plug. Stepping into the realm of oilfield equipment, we uncover a vital piece of apparatus that enhances the functionality of piping systems in drilling operations. Through extensive research and firsthand experience, we offer an in-depth exploration of bull plugs, aimed at industry professionals, mechanical engineers, and anyone keen on acquiring a comprehensive understanding of this product.

A bull plug is a term frequently used within the oil and gas sector, referring to a component employed to terminate or seal pipe openings effectively. This device is a solid plug, commonly cylindrical, threaded, and designed to provide a durable seal. Various industries rely on its ability to withstand high pressure and temperature, ensuring the success and safety of drilling operations.
From an experience standpoint, bull plugs have proven indispensable in managing fluid dynamics within pipelines. For professionals working on-site, having a selection of compatible bull plugs is imperative. They must ensure leaks are prevented, subsequently avoiding potential environmental hazards and equipment damage. A seasoned oilfield engineer might recall the critical instances where a correctly sized and installed bull plug prevented a costly delay or mishap, emphasizing its importance in project planning and execution.
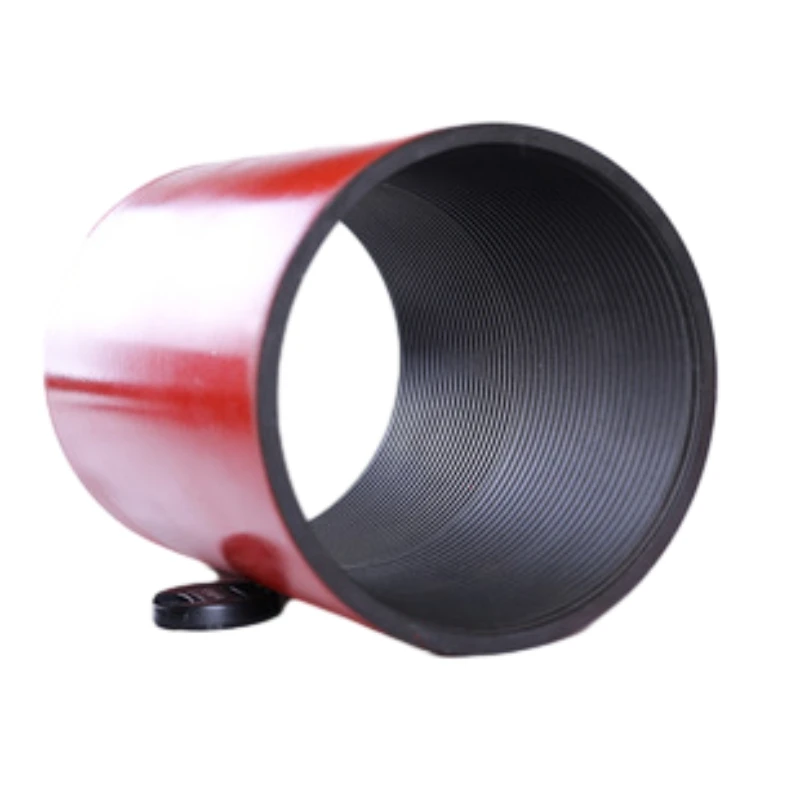
In terms of expertise,
employing bull plugs requires understanding both their material composition and sizing. Bull plugs typically come in materials like carbon steel, stainless steel, or other high-strength alloys, each chosen based on the operational environment. Corrosion resistance is another factor to consider, especially in subsea or corrosive environments. Proper thread engagement is crucial, making familiarity with pipe taper and threading measures a necessity for engineers and technicians. With every deployment, exact adherence to installation protocols as outlined by manufacturers will ensure the maximum performance and longevity of the plugs.
bull plug definition
The authoritativeness surrounding the use of bull plugs comes from adherence to industry standards. They must comply with certifications from organizations such as the American Petroleum Institute (API) and the American Society for Testing and Materials (ASTM). These endorsements guarantee the product's ability to perform under the demanding conditions found in oil and gas exploration. Engaging with such certified components assures operators that they are employing tools that meet stringent global standards, reinforcing the credibility and reliability of bull plugs in high-stakes environments.
Trustworthiness in applications of bull plugs is assured by maintaining a profound understanding of their integration into piping systems. By collaborating with reputable suppliers, engineers can access bull plugs that are tested for quality assurance extensively, ensuring reliable sealing. Moreover, regular maintenance checks and adherence to replacement schedules safeguard against potential failures, adding to their dependable nature.
In conclusion, while bull plugs may appear to be simple components in large-scale oil and gas operations, their role is unquestionably significant. Mastery over their application not only enhances operational efficiency but also ensures environmental safety and equipment longevity. For industry insiders and novices alike, investing time in understanding these components will invariably add value to their practice, supporting a safer and more reliable energy sector. As industry dynamics evolve, the importance of trusted, well-engineered components like bull plugs will remain constant, paving the way for innovation and improved operational outcomes.