Bull plugs, also known as flow control plugs or tubing plugs, are essential components in various industries such as oil and gas, water treatment, and even automotive sectors. These little devices may seem simple, but their role is critical in sealing and controlling the flow within piping systems.
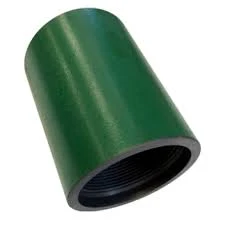
In the oil and gas industry, bull plugs serve as an indispensable tool in wellbore operations. Their robust design aids in sealing off the ends of pipes, preventing unwanted materials like sand or water from entering the wellbore. This process maintains the integrity of the drilling environment and ensures that the extraction of oil and gas remains efficient and safe. Built to withstand extreme pressure conditions, bull plugs are manufactured from durable materials like stainless steel or carbon steel, ensuring longevity and reliability.
In pipelines, where the control of fluids or gases is paramount, bull plugs act as secure barriers. By sealing off unnecessary sections of the pipeline, they help regulate the flow, preventing leaks, and maintaining system pressure. This functionality is especially critical during maintenance when certain sections of the pipeline need to be isolated without disrupting the entire system's operation. Here, the importance of precision engineering is clear — bull plugs must fit perfectly to perform their roles effectively.
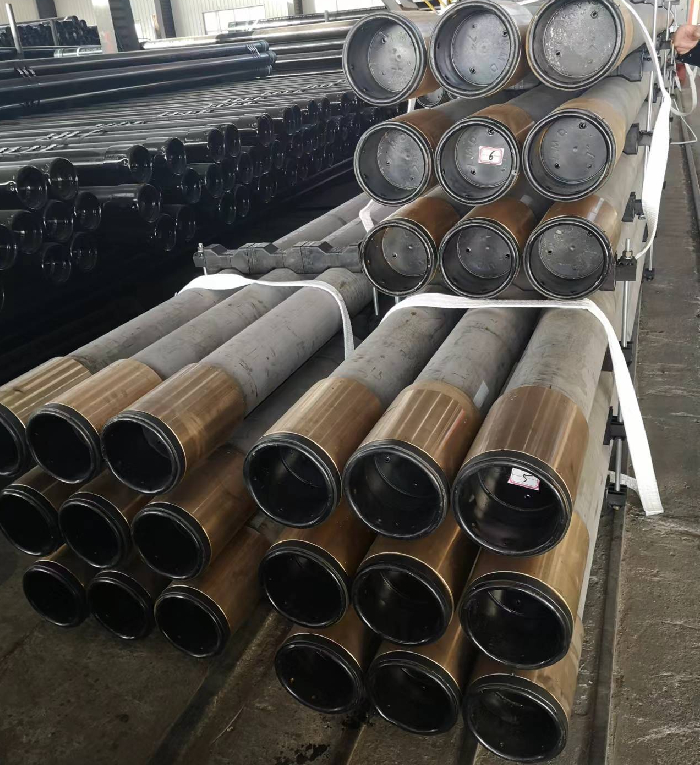
Interestingly,
bull plugs also find usage in automotive industries. They are sometimes used in hydraulic systems, where maintaining the pressure is crucial for operational efficacy. Here, bull plugs act as a safeguard, ensuring that the hydraulic fluid stays within the desired circuit, which ultimately helps maintain the optimal functionality of systems like braking or steering.
For water treatment facilities, bull plugs play a crucial role in the effective management of water flow in treatment reactors or pipelines. They ensure that different treatment phases do not interfere with one another by acting as temporary blockages. Moreover, because these facilities operate under strict health and safety standards, the reliability of bull plugs becomes a non-negotiable attribute. Quality assurance processes for these components are stringent, incorporating advanced testing to confirm their capability to handle specified conditions.
Despite their small size and straightforward design, these components must be designed with precision, crafted to specification, and thoroughly tested to function effectively in high-stakes environments. The choice of material, dimensions, and threading is critical; any deviation can lead to operational failures, potentially causing safety hazards or significant financial losses.
bull plug definition
In construction, another arena where bull plugs make a difference, they are used to cap off unfinished pipe lines or faucets during building phases. This is particularly vital in ensuring that dirt and debris do not enter the piping system, which can compromise the entire water or HVAC system. For contractors, using bull plugs not only ensures quality control but also aligns with compliance standards that prevent contamination and maintain clean and functional systems.
The expertise required in selecting the appropriate bull plug involves considering factors such as pressure requirements, environmental conditions, material compatibility, and future maintenance plans. Professionals in the field often rely on manufacturers with proven track records in precision engineering and quality assurance to supply bull plugs that stand up to industry demands.
As technology advances, so too does the design and application of bull plugs. The evolution of materials science promises the development of even more robust composites and alloys, pushing the limits of what these devices can withstand. Moreover, the integration of smart technology into pipeline infrastructures could see bull plugs playing a more sophisticated role, contributing to data collection and flow analytics.
In the realm of industry standards and certifications, those involved in choosing and applying bull plugs need to remain apprised of legislative changes and emerging best practices. Understanding the breadth of applications and maintaining updated knowledge of technological advancements can help industries optimize safety and efficiency while ensuring regulatory compliance.
For those seeking to ensure best practices, industry workshops, seminars, and certified courses can offer valuable insights into the latest innovations and regulatory requirements. Collaborating with engineering experts and experienced peers can also facilitate a better grasp of the complexities involved in the selection and application of bull plugs, ultimately bolstering performance outcomes across various applications.