Understanding the intricacies of bull plug dimensions is pivotal for various industries, including oil and gas, plumbing, and construction. A bull plug, essentially a cylindrical steel device, serves the critical role of terminating or sealing off the end of a pipe. This seemingly simple component can significantly impact the efficiency and safety of industrial systems, making it essential to delve into its dimensions and related considerations.
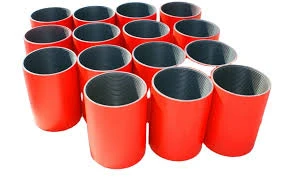
To comprehend bull plug dimensions, one must first recognize that these components come in a myriad of standard sizes tailored to fit an array of pipes with varying diameters. The outer diameter of these bull plugs is key, as it should match perfectly with the internal diameter of the pipe it seals. Common sizes range from a half-inch to several inches, depending heavily on industry requirements and the specific function the plug needs to perform.
For industries like oil and gas, where high pressure and corrosive materials are a constant, bull plugs must be meticulously crafted from high-grade, corrosion-resistant materials. Stainless steel, carbon steel, and alloy steel are popular choices due to their durability. The choice of material impacts not only the resilience of the bull plug but also its dimensional stability under extreme conditions. Ensuring the plug can withstand the internal pressure of pipes is crucial, as any failure can lead to catastrophic system shutdowns or environmental hazards.
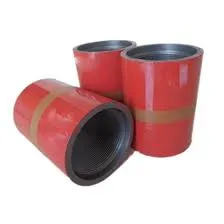
Moreover, the length of the bull plug is a dimension that, while sometimes overlooked, is critical to effective sealing. The adequate length ensures that the plug doesn’t just cover the pipe end superficially but seals it securely. Industry standards often dictate minimum lengths to optimize functionality and safety.
Industrially,
the threading of these bull plugs is another critical dimension. NPT (National Pipe Taper) and BSP (British Standard Pipe) are the two predominant threading standards used globally. Accurate threading ensures effective sealing, thereby preventing leaks. Inconsistent or poorly cut threads could lead to inadequate seals, posing risks of leakages and operational inefficiencies.
Professionals recognize the importance of understanding the pressure ratings that correlate with bull plug dimensions. Pressure ratings indicate the maximum pressure the bull plug can withstand without deforming or failing. These ratings are contingent on both the material and dimensional integrity of the plug. Misjudging pressure ratings can result in disastrous pressure bursts or the gradual degradation of the sealing component.
bull plug dimensions
Precision in manufacturing is non-negotiable when it comes to bull plug dimensions. The advent of CNC (Computer Numerically Controlled) machining has revolutionized how these components are crafted, allowing for precision that was previously unattainable. CNC technology ensures that every bull plug produced meets exact dimensional specifications, thereby reducing the risk of human error.
From an installer or technician’s perspective, understanding these dimensions and the rationale behind them simplifies the selection process, ensuring they opt for the best component for their specific application. Trust in the manufacturer’s specifications and pressure ratings is central to making informed decisions.
For industries seeking to fortify their systems with custom solutions, working with reputable manufacturers that offer bespoke bull plug dimensions is often the key to success. Customization allows for considerations beyond standard sizes and pressure ratings, facilitating unique design requirements and operational contexts.
Furthermore, the choice of coatings on bull plugs, often dictated by the application environment, impacts dimensions slightly as certain coatings can add minimal thickness. These coatings can include galvanization or specialized polymer layers that enhance corrosion resistance.
In conclusion, bull plug dimensions should not be taken lightly as they represent a confluence of precise engineering, material science, and practical application considerations. Industry professionals must remain updated on the latest standards and technologies affecting bull plug specifications to maintain optimal system integrity. The significance of understanding these dimensions extends beyond mere numbers; it is foundational to the reliability and safety of systems across varied fields.