Bull plugs, often overlooked but critical components in the oil and gas industry, demand accurate specifications to ensure efficient operations. Delving into bull plug dimensions can provide a striking competitive edge in optimizing these mechanical systems. A bull plug is essentially a type of pipe fitting used to stop the open end of a pipe, and its correct dimensions play a pivotal role in ensuring the integrity and functionality of the piping system.
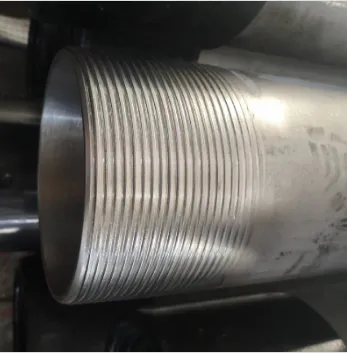
To begin with,
understanding the standard dimensions is essential. Bull plugs are typically categorized based on the nominal pipe size (NPS) and the schedule, which refers to the wall thickness of the pipe. The standard sizes range from as small as 1/8 inch to larger diameters going up to 6 inches or more, depending on the requirements of the specific project. The schedule, denoting the wall thickness, also varies, with common schedules including 40, 80, 160, and XXH (Double Extra Heavy).
Focusing on the expertise of selecting the right dimensions can significantly influence system performance. A standard 2-inch bull plug, for example, will have distinct dimensions with a specific outer diameter and wall thickness that are imperative for it to fit perfectly within a piping system. Choosing the incorrect size can lead to leaks, pressure inconsistencies, or even catastrophic failures, which underscores the importance of precise measurement.
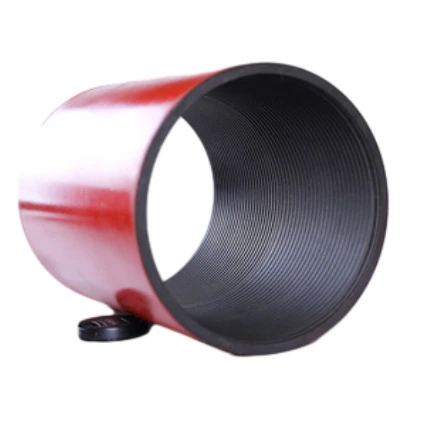
Authoritativeness comes into play with the selection of materials. Bull plugs are typically manufactured from carbon steel, stainless steel, or alloy steels. The choice of material affects durability, resistance to corrosion, and suitability for various environmental conditions. For instance, stainless steel bull plugs might be preferred in offshore drilling operations due to their superior resistance to the harsh, saline environment, whereas carbon steel may suffice for onshore applications with less corrosive threats.
A primary consideration for those in the industry is the compatibility of bull plug dimensions with existing systems. The ability to seamlessly integrate into an established infrastructure without alterations is highly valuable. This requires an understanding of industry standards such as ASTM (American Society for Testing and Materials) and ISO (International Organization for Standardization), which govern the manufacture and specifications of such components.
bull plug dimensions
Incorporating trustworthiness into this discussion, professionals rely on certified manufacturers whose products adhere to strict quality controls. Reputable companies provide documentation and certification that attest to the material composition and the exact dimensions of the bull plugs they produce. This documentation is not merely a formality but a critical piece of due diligence in ensuring that all components will perform as expected.
For those intending to delve deeper into bull plug specifications, consulting with engineers and technical experts who have extensive experience with the product can provide invaluable insights. They can offer guidance on bespoke solutions that cater to unique project demands, ensuring that the chosen dimensions and materials align perfectly with operational goals.
To maintain relevance and credibility in a fast-evolving industry, consistently updated knowledge about advancements in manufacturing technology and material science is crucial. Engaging with professional networks and participating in industry forums can enhance understanding and lead to improved decision-making when it comes to selecting the right bull plug dimensions.
In conclusion, precision, expertise, and due diligence in understanding bull plug dimensions are key to optimizing the efficiency and safety of piping systems in the oil and gas sector. From selecting the correct nominal size and wall thickness to ensuring material compatibility and certification, every detail counts towards achieving operational excellence.