Understanding the nuances of different pipe fittings is essential for industries relying on complex piping systems. One such component, the bull plug pipe fitting, plays a pivotal role in various sectors with its specialized utility. Despite its simplistic design, the bull plug is integral to the functionality and safety of piped systems in industries ranging from oil and gas to chemical and waterworks.
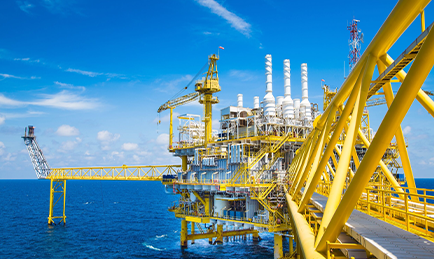
The bull plug is an innovative type of pipe fitting primarily used to seal pipe ends during testing or maintain system isolation when future extension of a pipeline is anticipated. Its utility is evident in scenarios where pipeline integrity must be tested without contamination or leakage risks. The bull plug's straightforward mechanism allows for efficient sealing while ensuring that operational or maintenance tasks can proceed smoothly.
An admirable feature distinguishing the bull plug is its straightforward yet effective design. Crafted from high-grade materials such as stainless steel, carbon steel, or other robust alloys, bull plugs endure high-pressure environments, making them ideal for intensive applications. This offers peace of mind to industries demanding rigorous safety and reliability standards. The ease with which it can be uninstalled further accentuates its functionality, allowing for quick reconfiguration of piping systems tailored to evolving operational needs.
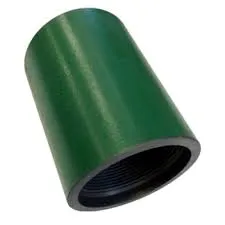
Expertise in selecting the appropriate bull plug fitting is paramount. A variety of specifications, such as size, material compatibility, and pressure-handling capacity, come into play. Professionals in the field must evaluate these parameters carefully to ensure an ideal match for the intended application. Bull plugs generally comply with several industry standards, such as ANSI or ASME, offering a blueprint for quality assurance and consistency across applications.
Real-world experiences in deploying bull plugs underscore their versatility. For instance, in the oil and gas industry, these components have proven invaluable in exploratory scenarios where temporary sealing is required. Furthermore, chemical processing plants employ bull plugs to safeguard against hazardous leaks, thus enhancing both safety and environmental compliance. Each successful deployment and operation using a bull plug adds to the credibility of the fitting, illustrating a journey of trusted use and expert application over time.
bull plug pipe fitting
Bull plugs are also crucial in waterworks and sewage management systems, where preventing contamination is paramount. The reliability of a bull plug in maintaining clean water supply standards demonstrates its indispensable role as a protector of public health. This widespread applicability across diverse sectors reinforces its authoritative presence as a trusted solution in tackling pipeline-related challenges.
Building a foundation of trust in the use of bull plug pipe fittings requires not only a wealth of industry knowledge but also transparent documentation of their capabilities. Technical data sheets, user manuals, and professional endorsements serve to inform and guide users in making informed decisions. Moreover, an emphasis on customer feedback and detailed case studies can significantly bolster confidence among potential users contemplating using bull plugs in their systems.
For those considering integrating bull plugs into their operations, a thorough consultation with industry experts is advisable. Engaging with seasoned professionals ensures that selected fittings align with specific requirements, optimizing both performance and safety. Although relatively simple in concept, the correct implementation of a bull plug can signify the difference between operational success and costly oversight.
In conclusion, the bull plug is a testament to how seemingly modest components can significantly impact industrial applications. By focusing on expert selection, informed use, and maintaining high standards of operation, industries can harness the full potential of bull plug pipe fittings, ultimately driving efficiency and safety in their systems. Embracing these fittings with a well-rounded understanding ensures not only compliance with best practices but also upholds the reputation of the industries that rely on them extensively.