Bull plug pipe layouts play a crucial role in industries such as oil and gas, where they are used to cap off or terminate the end of pipes. Understanding the intricacies of bull plug pipe layouts is essential for professionals aiming to optimize their systems for efficiency and safety. With a focus on experience, expertise, authoritativeness, and trustworthiness, this article delves into the nuts and bolts of bull plug pipe layouts, presenting a comprehensive guide for decision-makers and technicians alike.
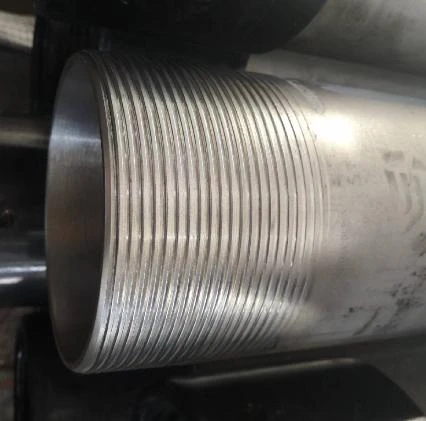
One of the foremost considerations in designing a bull plug pipe layout is the material selection.
Bull plugs are typically constructed from durable materials like stainless steel, carbon steel, or alloy steel. The choice of material should align with the operational environment and the specific requirements of the piping system. For example, stainless steel is an excellent choice for environments prone to corrosion, while carbon steel may be more cost-effective for less demanding applications.
Experience in the field suggests that efficiency in the installation of bull plugs can significantly impact the operational costs of piping systems. As one veteran piping engineer recounts, “A well-planned bull plug installation can save hours of labor and reduce the risk of leaks.” This insight is invaluable for organizations aiming to refine their operational budgets while maintaining high safety standards.
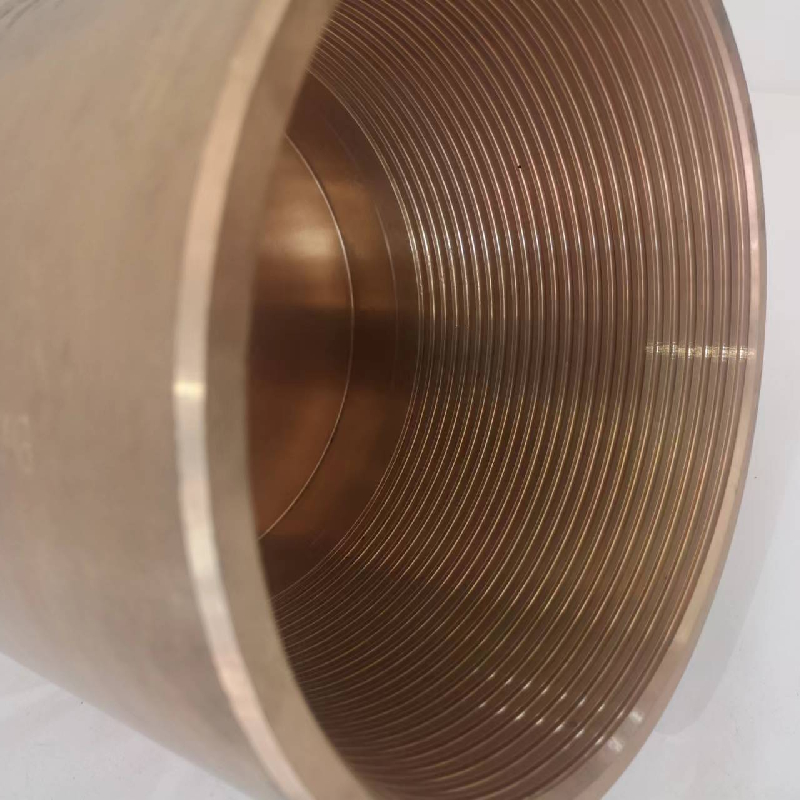
Expertise comes into play when considering the dimensions and threading of bull plugs. Typically, bull plugs are available in a range of diameters and threading types, such as NPT (National Pipe Thread) and BSPT (British Standard Pipe Taper). It is of paramount importance to ensure compatibility between the bull plug and the pipe threading to prevent misalignment and potential system failures. Consulting with threading standards specific to the installation’s geographical location will enhance this aspect of layout design.
From an authoritative perspective, adhering to industry standards and regulations is imperative. Many jurisdictions mandate compliance with standards set by organizations such as the American Petroleum Institute (API) or the International Organization for Standardization (ISO). For instance, specific API specifications dictate the pressure ratings and material grades suitable for bull plug applications. By ensuring compliance, companies not only avoid legal repercussions but also build trust with clients and stakeholders.
bull plug pipe layout
Building trustworthiness in the context of bull plug pipe layouts is often a matter of thorough testing and documentation. Employing certified inspection services to validate the integrity of the installed bull plugs can mitigate risks associated with manufacturing defects or improper installation. Furthermore, maintaining comprehensive documentation of the installation process and materials used can prove instrumental in troubleshooting and future audits.
In a real-world scenario, the inclusion of protective measures such as coatings or linings on bull plugs can enhance their lifespan and reliability. Protective linings are particularly crucial in industries where pipes are exposed to abrasive materials or extreme temperatures. A thoughtful consideration of these factors can extend the longevity of the piping system, a sentiment echoed by industry experts who emphasize the long-term cost savings achieved through such proactive strategies.
The challenge of optimizing a bull plug pipe layout also includes logistical considerations. Managing inventory efficiently and forecasting the demand for various bull plug sizes can prevent supply chain disruptions and ensure that necessary components are readily available for maintenance or unexpected repairs. Embracing digital inventory solutions can streamline this aspect, enabling real-time updates and reducing the risk of stock shortages.
Customization options further enhance the adaptability of bull plug pipe layouts. For complex systems, bespoke designs tailored to meet specific operational needs can be developed, ensuring optimal performance under unique conditions. Collaborating with manufacturers who offer customization services can yield significant advantages, including enhanced fit and function.
In conclusion, mastering bull plug pipe layouts requires a balance of practical experience, deep technical knowledge, adherence to authoritative guidelines, and an unwavering commitment to trust and transparency. By integrating these elements, organizations can optimize their piping systems to achieve greater efficiency, safety, and profitability. This approach not only ensures the smooth operation of industrial processes but also solidifies the organization’s reputation as a reliable operator in the field.