Understanding the Bull Plug Pressure Rating Professional Insights and Product Guidance
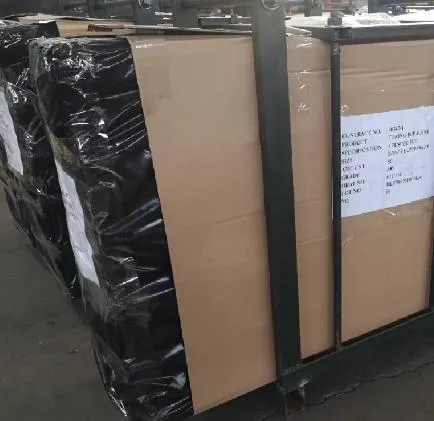
Bull plugs, essential components in the oil and gas industry, play a crucial role in ensuring the efficiency and safety of pipeline operations. These devices serve as end closures for pipes and tubes, preventing leaks and controlling pressure. As industries advance towards enhanced operational safety and efficiency, the bull plug pressure rating has become an indispensable consideration for professionals and engineers alike.
A bull plug is designed to withstand specific pressure levels within a pipeline system. Its pressure rating signifies the maximum pressure the plug can handle without compromising integrity or safety. This parameter is not merely a specification; it’s a critical factor that can influence project outcomes and safety measures.
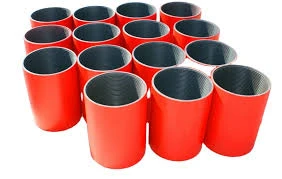
Through years of field experience, it's understood that the significance of pressure ratings goes beyond simple metrics. Imagine engaging in a high-stakes drilling operation, where unforeseen pressure spikes could lead to catastrophic failure if the bull plug is not rated appropriately. Therefore, understanding the appropriate pressure rating for your specific application is paramount.
From an expertise standpoint, various factors influence the optimal pressure rating of a bull plug. Material selection is pivotal; stainless steel and carbon steel are widely used due to their durability and resistance to harsh conditions. Stainless steel bull plugs are often preferred for high-pressure and corrosive environments due to their superior resistance and longevity. Meanwhile, carbon steel plugs provide a cost-effective alternative for less demanding applications.
It's crucial to note that pressure ratings are not universal across all bull plugs. Each plug is crafted and tested according to standards such as the American Petroleum Institute (API) specifications. These guidelines ensure the product’s reliability under stated conditions. Engineers must evaluate the maximum pressure the pipeline system will encounter and consult these ratings to select an appropriate bull plug.
bull plug pressure rating
Moreover, understanding the bull plug pressure rating involves acknowledging the operational conditions such as temperature fluctuations, fluid composition, and the presence of corrosive materials, each of which can affect the integrity of the plug over time. By leveraging comprehensive technical manuals and simulation testing, professionals can forecast potential pressure variances and plan accordingly.
Authoritativeness in selecting bull plugs comes from strict adherence to industry standards and leveraging manufacturing advancements. Brands that employ cutting-edge technology, such as advanced metallurgy and precision engineering, furnish bull plugs that not only meet but often exceed standard pressure ratings. Collaborating with such reputable manufacturers ensures the integrity and performance of your pipeline systems, which is a testament to their engineering prowess and commitment to safety.
Trustworthiness in the context of bull plug usage is not just about the product itself, but also extends to the service providers that facilitate their application. Investing in training for personnel on the correct installation, maintenance, and periodic inspection of bull plugs is essential. Regularly scheduled maintenance checks are indispensable for identifying early signs of wear or distress, thereby preempting potential failures.
For industry professionals, choosing the right bull plug with the appropriate pressure rating is not just about purchasing a component—it's about investing in operational efficiency and safety. The integration of advanced monitoring systems and sensors into pipeline operations can provide real-time data analysis, enabling proactive decision-making and ensuring that the chosen bull plug continues to perform within its designated pressure parameters.
In conclusion, the pressure rating of a bull plug holds vital importance in the seamless operation of pipeline systems. By prioritizing product quality, adhering to industry standards, and embracing innovative technology and practices, stakeholders can ensure safety and efficiency. The guidance of experienced engineers and collaboration with leading manufacturers further enhance the selection process, instilling confidence and peace of mind in pipeline management.