Every industry that deals with high-pressure systems, particularly in the realm of oil and gas operations, recognizes the vital importance of equipment that can withstand substantial stress. A key component in these systems is the bull plug, a vital element used in the sealing and blocking of pipelines to manage pressure effectively. Understanding the pressure rating of a bull plug is crucial not only for optimum performance but also for ensuring safety and reliability in high-pressure applications.
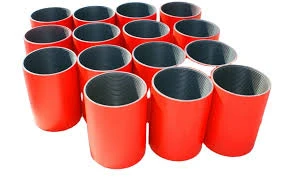
Pressure ratings indicate the maximum pressure a device — such as a bull plug — can withstand under predetermined conditions. This measurement is a critical aspect of equipment specifications in high-pressure environments. Safety standards are maintained through adherence to these ratings, as exceeding them could lead to equipment failure, catastrophic leaks, and potentially hazardous operational environments.
The bull plug, a threaded pipe fitting which is generally used to terminate the end of a piping system, is engineered to handle both the substantial mechanical pressures and the extreme environmental conditions typically found in oil and gas extraction and processing operations.
Its design and material composition largely dictate its pressure rating. These fittings are commonly manufactured using high-grade materials such as carbon steel, stainless steel, or high-strength alloys tailored to withstand specific pressures and temperatures. Each of these materials offers particular benefits and constraints, which should be evaluated based on the unique requirements of the application at hand.
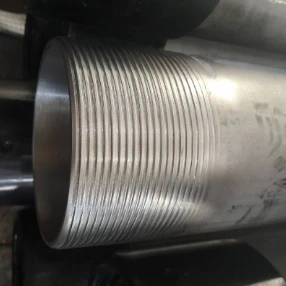
Expertise in selecting the appropriate bull plug pressure rating hinges on an in-depth understanding of several factors, including the specific operational environment, the substances being transported, and the regulatory standards in place. Engineers and purchasing managers alike must be attuned to these variables to make informed decisions. A common regulatory standard for pressure rating conformity is the American National Standards Institute (ANSI), which provides rigorous specifications for components used in piping systems. Compliance with these standards is a mark of reliability and safety, serving to reassure end-users of the product's integrity and capability.
A noteworthy aspect of using bull plugs in high-pressure systems is their role in pressure testing. Bull plugs are essential components during hydrostatic testing of pipes, where they are used to seal off sections of the pipeline to test for leaks. By enabling the section to be filled with water, it's then pressurized to verify the integrity of the pipeline. Thus, ensuring the bull plug used in such tests is correctly rated for the expected test pressure is crucial to prevent unexpected failures or accidents.
bull plug pressure rating
An often underrated component of pressure-rated equipment is the maintenance and inspection regimen. Regular checks and maintenance play a pivotal role in sustaining the usability and safety of bull plugs. Over time, exposure to corrosive substances or extreme temperatures can degrade even the most robust of materials. Comprehensive visual inspections, usage of non-destructive testing methodologies, and adherence to an established maintenance schedule contribute significantly to maximizing the lifespan and performance of these critical components.
Reliability in the oil and gas industry is built upon not just using the right equipment but ensuring that it is capable of performing to the expected standards under all conditions. This necessitates that every element, from selection to maintenance, aligns with industry best practices and thorough technical evaluation. Utilizing tools like bull plug pressure ratings becomes part of a broader strategic approach to risk management and operational excellence.
The credibility of a supplier may further enhance the trustworthiness of the bull plugs provided. Reputable suppliers with established histories in the industry are more likely to offer products that adhere to stringent quality control processes and international standards. It's advisable to engage in discussions with suppliers about the pressure ratings, safety tests conducted, and compliance certifications obtained for the bull plugs acquired. Doing so not only ensures safety and performance but also builds a worthwhile relationship with a trusted supplier.
For professionals seeking to ensure their operations are both efficient and secure, investing in the right bull plug with the correct pressure rating is non-negotiable. This choice plays a critical role in safeguarding personnel, equipment and the surrounding environment from the inherent risks of working with high-pressure systems. In this high-stakes arena, knowledge, and application of expertise in selecting suitable components are fundamental to achieving operational success and peace of mind.