For industry professionals navigating the vast world of pipe fittings, the distinction between a bull plug and a hex plug is critical in selecting the right component for any project. Both serve as closures in various piping systems, yet they fulfill slightly different roles with distinct design features that speak to their specific benefits.
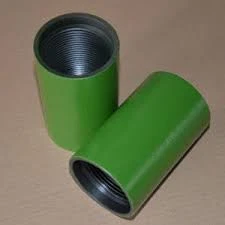
A bull plug, an essential component in oil and gas applications, is fundamentally a solid piece typically cylindrical in shape, tapering at one end. Its design often includes a rounded or flat head with a threaded opposite end that screws directly into a coupling. Known for its robust build, the bull plug is ideal for sealing the end of a pipe, a functionality that's crucial in high-pressure situations where reliability and durability are non-negotiable. Experienced field operators often favor bull plugs for their versatility and strength, reinforcing structures where pipe ends must be sealed effectively to withstand pressure and prevent leaks.
Conversely, the hex plug takes its name from the hexagonal shape of its head. This geometric feature renders it uniquely easy to turn and secure using a wrench, distinguishing it as user-friendly, especially in tighter spaces where tools need optimal grip angles. Hex plugs are not only convenient for their physical shape but are also used widely for maintenance and repair tasks due to their reusability and the ease of installation and removal. Building on this ergonomic advantage, they are an integral part of HVAC systems, domestic plumbing, and even in automotive settings where their accessibility eases the burden on technicians who frequently access system components.
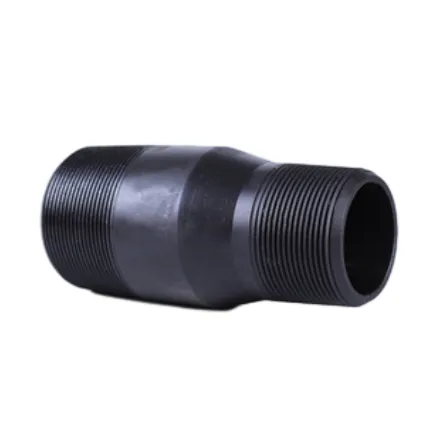
While both bull plugs and hex plugs are manufactured from materials like stainless steel, brass, or even certain appliqué types of plastic, their selection depends greatly on the context of their use.
Bull plugs generally dominate in environments where their sturdy build can cope with extreme conditions. Hex plugs, on the other hand, are favored in scenarios where accessibility and maintenance are pivotal.
bull plug vs hex plug
Expertise in the use of these fitting types requires understanding their material compatibilities, pressure ratings, and the standards to which they conform. For instance, bull plugs often meet specific API standards that certify their pressure-handling capacity, a testament to their authoritative use in oilfield applications. Similarly, hex plugs, while possibly utilized in environments with less demanding standards, still need to comply with local or international plumbing codes to ensure system integrity and safety.
Trustworthiness in the selection between a bull plug and a hex plug further comes from working experience with these components, knowing their reaction to various flow dynamics, temperature fluctuations, and possible corrosive environments. Professionals advise always to consult manufacturer datasheets and specifications, knowing that choosing the correct plug type affects not only the immediate application but the overall longevity and sustainability of the system it serves.
An authoritative choice in plug selection involves a rigorous understanding of the threaded dimensions covered in specifications like NPT or BSP, ensuring a tight seal and compatibility with existing system designs. Moreover, a knowledgeable decision is informed by whether temporary or permanent sealing is needed, alongside other engineering considerations like vibration or potential for systematic thermal expansion.
In summary, the bull plug and the hex plug are not merely interchangeable items but are uniquely suited to specific tasks that underline their role in reliable system management. The choice between them should effortlessly align with project specifications, environmental conditions, and maintenance plans, ensuring success in both engineering objectives and operational trust.