In the ever-evolving landscape of the oil and gas industry, the significance of casing and tubing connections cannot be overstated. These critical components form the backbone of well integrity, ensuring optimal performance and safety in drilling operations. With advancements in technology and the rise of specialized manufacturing processes, understanding these connections has become paramount for industry professionals seeking to optimize their operations and mitigate risks.
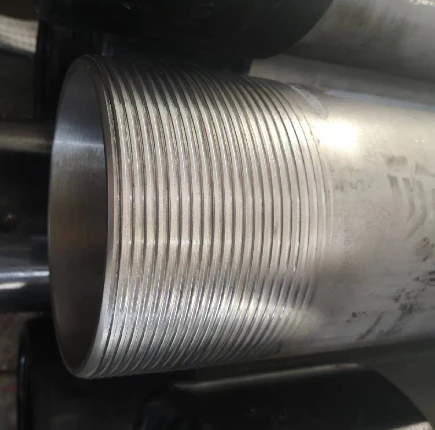
Experience in handling casing and tubing connections reveals the intricate interplay between design, materials, and application-specific requirements. Experienced engineers emphasize the importance of selecting the right type of connection to match the geological and operational conditions of each well. In challenging environments, such as deepwater drilling or high-temperature, high-pressure (HTHP) scenarios, choosing premium connections that offer enhanced sealability and load-bearing capacity becomes crucial. These connections not only withstand the extreme conditions but also prevent environmental hazards associated with gas leaks and oil spills.
From an expertise standpoint, several factors must be considered when assessing casing and tubing connections. Thread design, for instance, plays a critical role in ensuring robust performance. Thus, the selection between buttress, API round, or proprietary premium threads depends on the specific demands of the well operation. Each of these designs has distinct properties – buttress threads are renowned for their tensile strength while API round threads are favored for their ease of makeup and versatility. Premium threads, developed by leading manufacturers, often incorporate proprietary technology tailored for extreme conditions, offering advanced options like anti-galling protection and high torque capability.
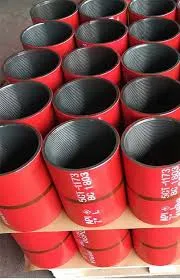
Authoritativeness in this domain is often attributed to companies and engineers who consistently deliver innovative and reliable solutions. Industry leaders such as Tenaris, Vallourec, and Baker Hughes have set benchmarks in developing cutting-edge connections that address modern-day challenges. Their research and development segments are continually pushing boundaries, exploring new materials like high-strength steel and corrosion-resistant alloys that stand up to the harshest environments. Additionally, their collaborations with academic institutions and participation in industry consortia underscore their commitment to advancing knowledge and setting industry standards.
casing and tubing connections
Trustworthiness in casing and tubing connections is built through rigorous testing and adherence to international standards. Prior to deployment, connections undergo a series of assessments designed to test their durability and resilience under simulated conditions. Standardized testing protocols, as set by the American Petroleum Institute (API), provide a framework ensuring consistency and reliability. Moreover, field trials and customer feedback loops further enhance confidence in these products, as real-world data contribute to continuous improvement and validation of performance claims.
For businesses operating in the oil and gas sector, the integration of digital technologies presents a transformative opportunity to elevate casing and tubing connections. By leveraging data analytics and artificial intelligence, predictive maintenance becomes possible, enabling operators to identify potential failure points and schedule maintenance activities proactively. Digital twins of well sites allow for real-time monitoring and adjustments to operational parameters, ensuring that connection integrity is maintained throughout the well's lifecycle.
In conclusion, the realm of casing and tubing connections is marked by a blend of tradition and innovation, requiring a profound understanding of technical specifications and field applications.
Expertise in this domain is crucial for optimizing performance and safeguarding environmental and operational integrity. As the industry continues to embrace digital solutions, the potential for enhancing the functionality and reliability of these vital components is endless, promising a future where safety and efficiency go hand in hand.