Casing and tubing connections play a pivotal role in the oil and gas industry, acting as the lifeline for efficient and safe exploration. With evolving technology and a greater emphasis on sustainable practices, these components possess both complexity and innovation that demand industry attention.
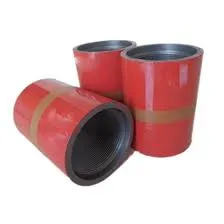
Effective casing and tubing connections ensure the integrity of the wellbore. Drawn from the experience of field engineers, real-world applications highlight the critical need for robust connections. A seasoned engineer recalls a scenario from a high-pressure well where traditional connections failed, leading to operational setbacks. However, the introduction of a new thread design that incorporated advanced metallurgy not only overcame these setbacks but also extended the well's operational life. Such firsthand experiences underscore the need for innovative designs and ongoing advancements.
From an expertise standpoint, the differentiation between various casing and tubing connections is crucial. The choice largely depends on the well environment. For instance, threaded and coupled (T&C) connections are commonly employed due to their flexibility and reliability in standard wells. Conversely, for high-pressure, high-temperature (HPHT) wells, premium threaded connections are preferred. These connections offer superior sealing capabilities, reduced risk of leakages, and the ability to withstand intense stress environments. The materials used in these connections, often high-grade steels or exotic alloys, reveal the intricate balance of engineering precision and material science expertise required to ensure reliable performance.
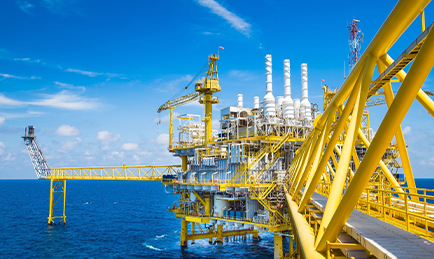
Authoritativeness in casing and tubing connections is established by the rigorous standards set by bodies like the American Petroleum Institute (API). API specifications, such as Threading and Gauging of Casing, Tubing, and Line Pipe Threads (API Spec 5B), provide a framework that manufacturers must adhere to, ensuring that each product meets the necessary safety and performance parameters. Adherence to these standards guarantees that the connections can withstand the operational demands without compromising safety or efficiency. Additionally, leading manufacturers collaborate with independent testing agencies to validate their products under extreme conditions, further cementing their authority in the field.
Trustworthiness is paramount in the industry, especially when the ramifications of failure can be catastrophic. Companies looking to establish credibility often emphasize traceability in their production process. This involves tracking every component from raw material sourcing through final assembly, allowing for transparency and accountability. Furthermore, manufacturers often invest in continuous training programs, certifying their workforce to handle the latest machinery and techniques. This dedication to quality assurance reassures clients of the reliability and performance of the casing and tubing connections they are investing in.
casing and tubing connections
Moreover, technological advancements have bolstered the inspection processes. Non-destructive testing (NDT) methods such as ultrasonic testing and magnetic particle inspection are standard in ensuring the structural integrity of these connections. Real-time data collection and analysis through these methods allow for proactive maintenance schedules and highlighted wear patterns that predict future performance issues.
Understanding these connections extends beyond just the product itself. The installation process is key, with proper torque application and alignment required to maintain integrity. Field technicians often rely on digital torque gauging tools for precision, reducing the chances of human error that could lead to premature failures. Training programs focusing on installation techniques further ensure that best practices are adhered to consistently.
In the quest for sustainability, manufacturers are now exploring materials with reduced environmental impact, such as recyclable alloys and coatings that minimize wear and prolong lifecycle use. Efforts in R&D are focusing on developing connections that require less frequent replacements, reducing the carbon footprint associated with manufacturing and transportation.
In summary, casing and tubing connections are integral to the performance and safety of oil and gas operations. Experience from the field, combined with technical expertise, authoritative standards, and trustworthiness in quality control, ensures these components meet the high demands of modern exploration. As technology advances, so does the potential for further innovation in this essential industry aspect, promising a future where efficiency and sustainability go hand in hand.