In the world of oil and gas drilling, understanding the fundamental differences between casing and tubing is vital for efficient and safe well completion. Both casing and tubing play crucial roles in the structural integrity and functionality of wells, yet they serve distinct purposes and possess unique characteristics tailored to their specific applications.
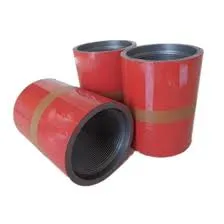
Casing is the large-diameter pipe that is lowered into the drilled borehole and cemented in place to provide structural stability to the wellbore. It prevents the borehole from collapsing, isolates different geological formations, and keeps drilling fluids contained within the well. Casing also protects freshwater aquifers from contamination by isolating the different pressure zones encountered during drilling. There are several types of casing, each designed for different stages of drilling conductor casing, surface casing, intermediate casing, and production casing. Each type has its own specifications and functions but collectively ensures the overall safety and efficiency of drilling operations.
On the other hand, tubing is the smaller-diameter pipe installed inside the casing during the completion phase. It functions as the conduit for transporting oil and gas from the reservoir to the surface. Tubing is critical in optimizing the flow of hydrocarbons, as it reduces the pressure drop and prevents corrosive reservoir fluids from coming into contact with the casing. This not only prolongs the well's life but also increases operational efficiency. Tubing is typically removable, allowing operators to conduct maintenance or replace worn sections without affecting the casing. This modularity is a vital feature that helps manage costs and minimize downtime.
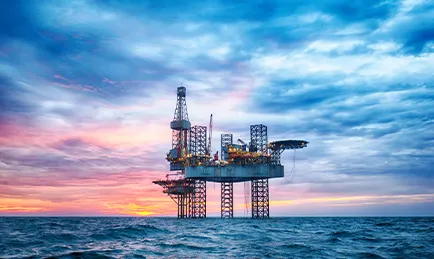
Expertise in selecting the appropriate casing and tubing materials is essential for well integrity. Casing materials are usually made from steel, with grades selected based on factors such as depth, pressure, temperature, and corrosive environment. Tubing, while also steel, often requires different material selections to withstand the corrosive nature of hydrocarbons and the varying temperatures of the reservoir. Advanced alloys and coatings may be applied to both casing and tubing to enhance their performance and longevity in hostile environments.
what are the differences between casing and tubing?
The installation processes for casing and tubing differ significantly. Casing is typically cemented in place, which involves pumping cement slurry into the space between the casing and the borehole walls. This creates a seal that isolates the different pressure zones and prevents fluid migration between formations. The cementing process is critical not only for securing the casing but also for maintaining well control. In contrast, tubing is hung from the wellhead and does not require cementing. It needs to be secured in a way that allows for thermal expansion and contraction, as well as ease of removal when necessary.
Authoritativeness in casing and tubing operations is paramount for well safety and efficiency. Industry standards, such as those set by the American Petroleum Institute (API), provide detailed guidelines on design, manufacture, and installation processes. Adhering to these standards ensures that casing and tubing can withstand the demanding conditions of the subsurface environment. Skilled professionals, including petroleum engineers and drilling specialists, are essential in the planning and execution of casing and tubing operations, utilizing advanced software and tools to predict environmental conditions and design the optimal structural solutions.
Trustworthiness in casing and tubing systems comes from rigorous testing and quality assurance. Each joint of casing and tubing undergoes stringent inspections to detect any defects or anomalies. Non-destructive testing (NDT) methods like ultrasonic and magnetic particle inspection ensure the integrity of these components before deployment. Additionally, ongoing monitoring and maintenance programs during the well's life cycle detect any potential issues that could compromise safety or efficiency.
Understanding these nuances offers valuable insight for operators seeking to optimize their well design and production strategy. By focusing on experience, expertise, authoritativeness, and trustworthiness, companies ensure that their casing and tubing systems are both reliable and effective, safeguarding their investment in oil and gas production.