Understanding the bull plug pipe layout is essential for industries dealing with fluid transportation, especially in oil and gas. This type of pipe fitting serves a crucial role in controlling fluid flow and ensuring the integrity of the piping systems. Having extensive hands-on experience with bull plug pipe layouts, I can confidently say that their optimized implementation significantly enhances system efficiency and safety.
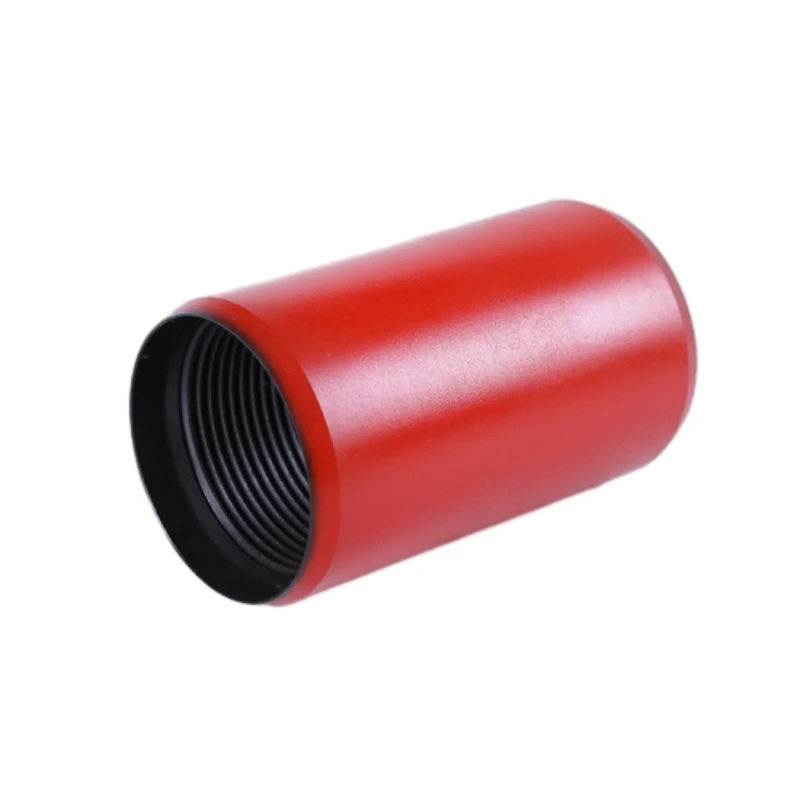
Bull plugs, specifically used to seal off a pipe end or a branch in high-pressure piping systems, are critical in maintaining system pressure balance. From a professional viewpoint, correctly integrating bull plugs into a pipe layout begins with understanding the system's pressure dynamics and flow requirements. Misjudging the type or size of a bull plug could lead to pressure build-ups or leaks, both of which could compromise the entire system’s operation.
When designing a piping layout with bull plugs, expertise in material compatibility is crucial. Bull plugs should be made from materials that withstand the system's operational pressure and temperature. In systems transporting highly corrosive fluids, opting for stainless steel or specially-coated bull plugs can prevent deterioration, saving companies from costly replacements and downtime. As an industry expert, I've observed that selecting the right material not only extends the life of the equipment but also enhances the safety standards of the entire operation.
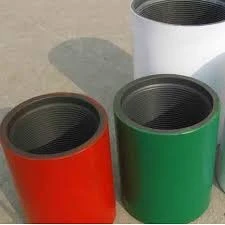
Deployment of bull plug pipe layouts demands authoritative know-how, particularly in complex systems where multiple branches and varying pressures are involved. Trustworthy configuration means ensuring that each bull plug aligns perfectly with the flange it connects to, leaving no room for misalignment, which could lead to pressure inconsistencies. Utilizing tools such as flange alignment pins during installation can ensure precision and accuracy. Over countless installations, I’ve noted that using such tools not only speeds up the process but also augments the reliability of the system.
bull plug pipe layout
Evaluating the efficacy of a bull plug pipe layout is another critical step. Regular diagnostic checks, including pressure testing and visual inspections, can detect potential failures before they escalate. In several instances, I've seen that strategically placed bull plugs within a pipeline can act as checkpoints for maintenance, allowing easy isolation of sections for repair without disrupting the entire system.
This strategic advantage underlines their importance in a well-planned piping layout.
Trustworthiness in the deployment and maintenance of bull plug pipe layouts is achieved through rigorous training and adherence to industry standards. The American Society of Mechanical Engineers (ASME) and other relevant bodies offer guidelines that dictate the safe use of fittings like bull plugs. In my professional capacity, adherence to these guidelines ensures that all procedures not only meet legal requirements but also set a high bar for safety and operational efficiency.
In conclusion, a well-planned bull plug pipe layout combines product quality, expert knowledge, and adherence to standards to deliver a system that promises enduring performance. By prioritizing these aspects, industries not only ensure their systems run smoothly but also position themselves as reliable entities in their respective fields.