Casing pup joints, essential components in the oil and gas industry, play a crucial role in maintaining the integrity of wellbore structures. Engineered with precision, these short segments of casing are designed to extend the length of a string without altering its primary characteristics. The optimal deployment of casing pup joints ensures seamless operations, and their selection becomes a strategic endeavor for engineers and project managers in the field.
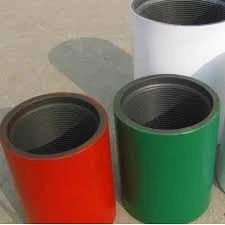
The expertise in understanding the variety of casing pup joints available—ranging in different grades and thread types—can significantly impact both the performance and safety of drilling operations. Primarily, the selection of the right material is paramount. Commonly manufactured from steel, these joints must meet the rigorous standards set by industries to withstand high-pressure environments and resist corrosive elements present in subterranean conditions.
A valuable aspect of expertise stems from the in-depth knowledge of the grading systems for casing pup joint materials. Typically, these classifications—K55, N80, L80, P110—indicate the material properties like yield strength and the ability to withstand external conditions. Expert selection demands a calculation considering the depth of the well, the expected pressure, and environmental factors, tailored to match the application.
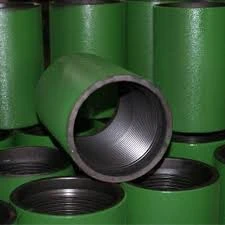
Moreover,
the thread specification on pup joints is a critical detail not to be overlooked. Thread compatibility assures that no leaks occur, which could lead to catastrophic failures and environmental hazards. Knowledge of API (American Petroleum Institute) and premium threads allows professionals to choose pup joints that guarantee structural compliance and longevity.
casing pup joint
Experience in handling casing pup joints is pivotal. Field engineers with extensive backgrounds in oil and gas operations bring lessons learned from previous projects to optimize use. They can predict wear and degradation and recommend procedures to monitor potential points of failure over time. Such forethought fosters trustworthiness in the operational status of a drilling site.
Installation procedures further underscore the significance of experienced oversight. Meticulous calibration and maintenance are essential to ensure these joints are seamlessly integrated within the casing string. Precision torque application and alignment using innovative tools and techniques preserve joint integrity, preventing mishaps that could arise from improper handling or installation.
Within the commodities market, a comprehensive supplier evaluation establishes authority and trust in sourcing casing pup joints. Verification of supplier credentials, adherence to current API specifications, and conducting rigorous quality assurance tests cement the reliability and authenticity of the procurement process.
Ultimately, casing pup joints are indispensable to the efficient and safe operation of drilling platforms. The intersection of experience, specialized knowledge, authoritative standards, and trust-backed supplier relations forms the foundation for optimizing the deployment of casing pup joints. Their understated presence in the wellbore belies a critical role that, when executed expertly, ensures operational success and environmental safety. Understanding these pivotal elements underscores their indispensable nature in modern energy exploration endeavors.