In the dynamic world of oil and gas extraction, the term casing pup joint is more than just industry jargon; it's a critical component that ensures the efficiency and safety of drilling operations. These seemingly simple yet essential pieces of equipment are fundamental in connecting various sections of casing pipes, thereby playing a pivotal role in the structural integrity of drilling wells. Despite their unassuming nature, casing pup joints are indispensable in adapting the drilling process to specific geological formations and operational demands.
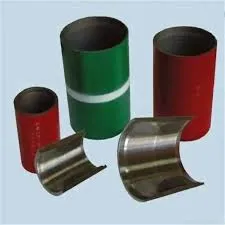
Crafted meticulously from high-grade steel, casing pup joints are designed to withstand extreme pressures and temperatures found deep within the earth's crust. Their construction involves rigorous adherence to stringent industry standards, ensuring they can support the colossal weight of the drilling structure while maintaining a seal that prevents fluid and gas leaks. This not only guarantees worker safety but also protects the environment from potential contamination.
The functionality of casing pup joints transcends their basic role as connectors. They are also utilized to adjust the length of casing strings, offering precise control over the drilling depth and trajectory. This adaptability is crucial when unexpected geological conditions are encountered, necessitating rapid adjustments to prevent costly downtimes. By integrating various lengths of pup joints, operators can customize casing strings that fit the specific needs of each drilling operation, enhancing overall efficiency and reducing wear on drilling equipment.
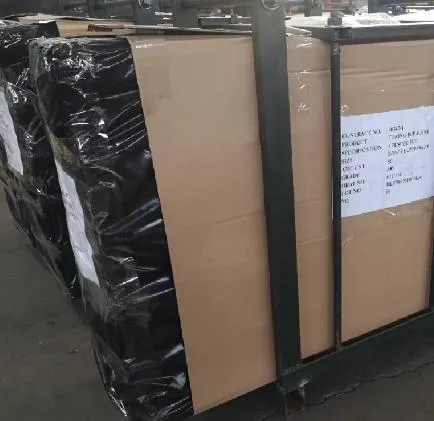
Expertise in the use of casing pup joints extends beyond their mechanical application. Selecting the appropriate size and specification requires an in-depth understanding of geological data and drilling objectives. Engineers and technicians must consider factors such as the tensile strength required to hold the casing string securely, the corrosive properties of the geological environment, and the thermal expansion coefficients of the materials involved. This level of detail ensures that the selected pup joints will maintain their integrity throughout the life of the well.
casing pup joint
Moreover, advancements in metallurgy and manufacturing processes have paved the way for innovations in pup joint design. Enhanced coatings and treatment methods have extended their lifespan, offering greater resistance to corrosion and mechanical fatigue. The development of more durable and lighter materials has also contributed to more efficient drilling operations by reducing the overall load on derricks and other structural components.
Trust in a manufacturer’s reputation is paramount when procuring casing pup joints. Companies with a proven track record in producing high-quality, reliable equipment are preferred. An awareness of industry standards, such as those set by the American Petroleum Institute (API), serves as a benchmark for evaluating the trustworthiness of these manufacturers. API-certified pup joints are synonymous with quality, symbolizing a commitment to safety and performance.
Field experiences have continually underscored the importance of rigorous testing and quality assurance. Deployment in diverse drilling scenarios has demonstrated that the right pup joint can significantly reduce operational risks. Testimonials from field engineers and drilling supervisors further amplify the credibility of these products, presenting real-world evidence of their reliability and performance under adverse conditions.
In conclusion, casing pup joints are not merely components in a drilling apparatus but critical enablers of successful oil and gas extraction. They embody a blend of engineering prowess and methodological precision, representing the cutting-edge of materials science and production techniques. As the demand for fossil fuels continues to drive drilling operations deeper and into more complex geological environments, the role of well-crafted casing pup joints becomes ever more vital. For stakeholders and decision-makers in the industry, understanding their function and selecting the right components can mean the difference between operational excellence and compromised safety.