Understanding the intricacies of casing threads and couplings is pivotal for professionals in the oil and gas industry, where efficiency and reliability are paramount. High-quality casing threads and couplings not only enhance the operational efficiency but also ensure safety and integrity in wellbore operations.
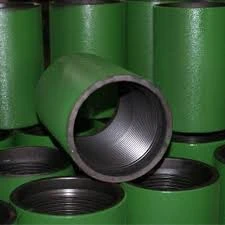
In the harsh environments of drilling, selecting the proper casing threads and couplings impacts performance significantly. The industry often utilizes premium-threaded connections due to their high resistance to wear and tear, offering solutions even in extreme temperature and pressure conditions. Years of industry feedback have shown that corrosion resistance and tensile strength are critical factors that cannot be ignored when choosing these components.
An expert understanding of thread profiles is vital. API connections, which are standardized for interoperability, and premium connections, known for their high-sealability and superior tensile strength, dominate the market. Premium threads surpass API threads in scenarios demanding leak resistance and structural stability, making them a favored choice for challenging projects. Investing in premium threads, in turn, minimizes downtime due to fewer issues with thread galling and breaking.
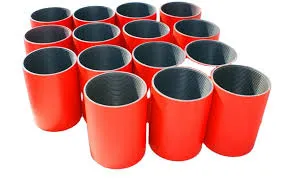
Couplings play a complementary role in ensuring the reliability of casing strings. Top-quality couplings must exhibit precision and strength to maintain thread integrity under various stressors. Material selection for couplings is crucial; they should be made from high-grade steel capable of withstanding environmental adversities and operational demands. The use of advanced metallurgy and precision machining ensures that couplings meet the required performance standards.
For optimum performance, the coupling threads must match casings with utmost precision. Recent advances in manufacturing technologies have led to the production of couplings with minimized tolerances, enhancing the overall reliability of well operations. This perfect marriage of threads and couplings is critical in reducing the risks of unintentional detachment, which could lead to costly operational interruptions.
casing threads and couplings
Incorporating real-world feedback from engineers and field operators lends unparalleled authenticity to the user experience. Experience sharing in industry forums highlights that well-implemented casing thread and coupling solutions greatly reduce the maintenance costs and prolong the life span of drilling equipment.
Experts often advise on regular maintenance schedules to maintain the integrity of threads and couplings. Timely inspections and using thread protectors are preventive measures endorsed by professionals to avert thread damage.
Trustworthiness in casing threads and couplings also lies in adherence to industry standards and testing protocols. Rigorous quality control processes backed by third-party certification guarantee that these components meet global safety and performance standards. Industry leaders often partner with certified manufacturers to ensure that every piece meets the stringent regulations and delivers the promised reliability.
Authoritative insights reflect that technological advancements are continuously shaping the capabilities of casing threads and couplings. High-torque strength, corrosion-resistant coatings, and the ability to withstand high pressures are innovations attributed to relentless research and development efforts. Collaboration between manufacturers and research institutes often results in pioneering products setting new benchmarks for quality and performance.
Emerging trends suggest a growing investment in digital monitoring technologies, providing real-time data on the condition of threads and couplings. Such innovations are expected to revolutionize maintenance regimes by facilitating predictive maintenance schedules, thereby preventing unexpected failures in demanding drilling scenarios.
In conclusion, while casing threads and couplings are often overshadowed by larger machinery in discussions, their importance to the seamless and safe operation cannot be overstated. Industry experts unanimously agree on the need for continuous evaluation and adaptation to new technologies and methodologies to achieve operational excellence. As the demands on equipment evolve, so too must our approaches to their management and deployment, ensuring performance, safety, and cost-effectiveness in this critical field.