In the intricate world of oil and gas extraction, casing threads and couplings play an indispensable role in ensuring the structural integrity of wellbore casings. Selecting and implementing the right casing threads and couplings is vital for any oil and gas operation, as it directly influences the efficiency, safety, and cost-effectiveness of the entire drilling process. Drawing from years of experience and backed by expert insights, this article will delve into the nuances of casing threads and couplings, offering a comprehensive perspective on their types, applications, and technological advancements.
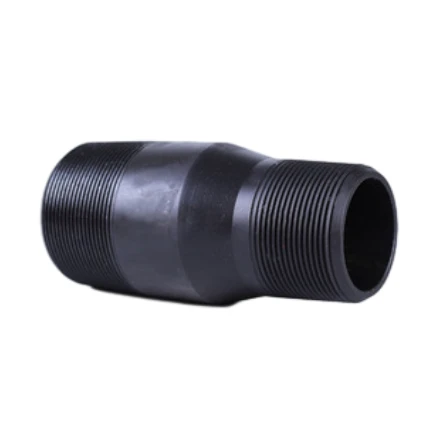
At the core of any oil well, casing threads and couplings provide the necessary means to join sections of casing together with a sturdy, secure connection. These components must withstand immense pressures and resist corrosion from the harsh underground environment. The threads, typically cut into the ends of casing sections, and the corresponding couplings, which serve as threaded connectors, form the backbone of this system.
Product selection begins with understanding the thread types. The most widely used threads are API (American Petroleum Institute) standardized threads. API connections, such as BTC (Buttress Threaded Connection), are renowned for their reliability and compatibility across various casing manufacturers. Yet, despite their widespread acceptance, API threads may not always meet the specific needs of more challenging environments, leading to the increased use of premium connections.
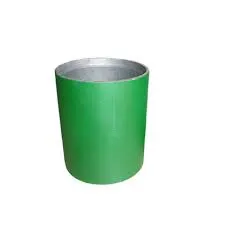
Premium connections offer enhanced features, including improved sealing capabilities, higher tensile strength, and superior resistance to extreme temperature fluctuations. Often proprietary, these connections are uniquely designed by manufacturers to cater to specific well conditions. For instance, in deepwater drilling, where environmental stresses are significant, premium threads with metal-to-metal seals offer a more robust solution compared to traditional elastomer seals.
The coupling design is equally critical. Standard couplings, generally made of the same grade of steel as the casing, must facilitate a perfect fit to prevent structural load failures. The rise in horizontal drilling and unconventional shale plays has pushed the innovation envelope, leading to the development of semi-premium and flush joint couplings. These advanced designs provide enhanced torque capacity and reduced cross-sectional area impact, which is particularly beneficial when navigating complex well geometries.
casing threads and couplings
Industry experts underscore the importance of non-destructive testing (NDT) and verification processes in maintaining the integrity of casing connections. Techniques such as magnetic particle inspection, ultrasonic testing, and X-ray inspection are pivotal in identifying imperfections that could compromise joint strength. Employing these testing methods as part of the procurement and maintenance strategy solidifies trust and reliability in the products chosen.
The engineering behind casing threads and couplings is also subject to ongoing technological innovations. Computer-aided design (CAD) and finite element analysis (FEA) are now routinely employed by manufacturers to simulate stresses and optimize thread geometry, ensuring maximum performance under predicted well conditions. This approximation not only aids in creating highly reliable products but also serves to reduce material costs by accurately determining the necessary specifications for manufacturing.
Empirical evidence from numerous field applications reveals that the judicious selection of casing threads and couplings can lead to significant cost savings through increased operational efficiency and reduced equipment failure. Real-world case studies frequently highlight instances where premium connections have enabled extended reach drilling, allowing operators to access deeper reserves with fewer interruptions.
Cementing the authority of the chosen casing components is the adherence to stringent international standards and certifications. Compliance with ISO 9001, 14001, and 45001 standards ensures that the manufacturing process meets global requirements for quality, environmental management, and occupational health and safety. Partnering with certified manufacturers not only guarantees product quality but also reinforces an operator's commitment to responsible resource extraction.
In conclusion, the critical choice of casing threads and couplings encompasses a detailed assessment of technical requirements, environmental conditions, and cost considerations. Leveraging expertise and authoritative insights in this domain serves to build trust and optimize drilling operations' performance and safety. As the industry continues to evolve, staying abreast of technological advancements and maintaining rigorous testing and quality assurance standards will be key to ongoing success and sustainability.