In the oil and gas industry, casing threads and couplings play a crucial role in maintaining the integrity and efficiency of drilling operations. These components ensure the secure attachment of casing pipes, which function as a structural support for the well, preventing the collapse of unstable formations and protecting the wellbore. Here, we'll delve into the intricate details of casing threads and couplings, drawing from professional experience and industry expertise to provide a comprehensive understanding of their importance.
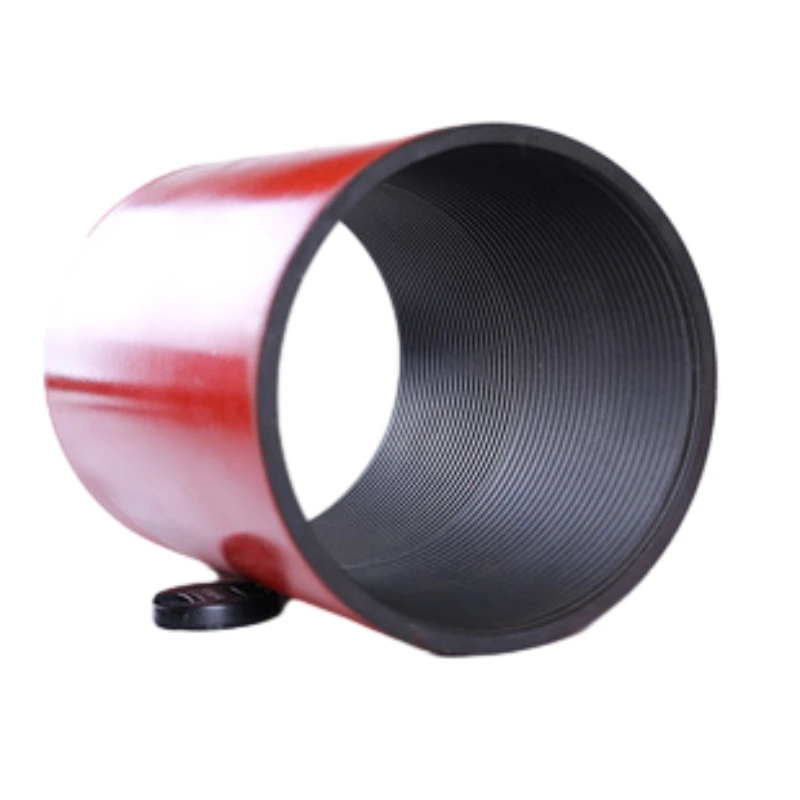
Casing threads are precision-engineered to withstand the harsh environments encountered in oil and gas exploration and production. These threads are designed to ensure a tight, leak-proof seal between the sections of casing pipe. This seal is fundamental, as it prevents the intrusion of external materials into the well and averts the leakage of drilling fluids and hydrocarbons, which can lead to environmental and safety hazards.
The expertise required in designing and manufacturing casing threads cannot be overstated. Each thread pattern is crafted to meet stringent industry standards, such as those set by the American Petroleum Institute (API).
These standards are crucial to ensuring that the threads can withstand high tension, compression, and torsional loads during operations. Some of the most common thread types include Buttress threads, which provide high axial load resistance, and API Round threads, known for their ease of assembly and reliability in various drilling conditions.
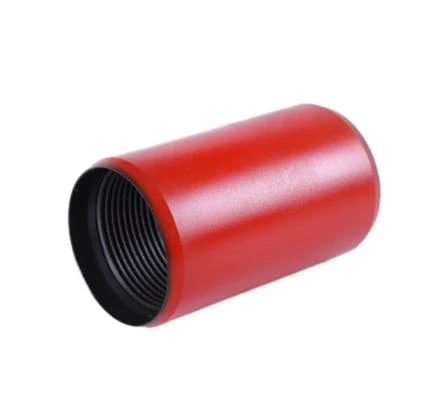
Couplings, on the other hand, are essential components used to join two lengths of casing pipe. These components are manufactured from high-grade steel and are engineered to accommodate the specific thread pattern of the pipes they connect. The coupling’s primary function is to provide a robust connection that maintains the tensile strength and structural integrity of the casing string throughout its operational life.
Drawing from authoritative knowledge, proper installation of casing threads and couplings is imperative for ensuring the longevity and reliability of the entire casing system. The coupling joint must be handled with precision, avoiding any damage to the threads during assembly. The application of the correct torque is essential to prevent over-tightening, which can deform the threads, or under-tightening, which risks leaks.
casing threads and couplings
Part of the expertise in this field involves understanding the various environmental and operational conditions that can affect the performance of casing threads and couplings. For instance, in corrosive environments, the use of protective coatings or corrosion-resistant alloys is recommended to extend the operational life of the casing system. Additionally, in areas prone to seismic activity, selecting thread designs that can accommodate sudden shifts or vibrations is crucial.
Authoritative advancements in technology have also led to the development of premium connection threads. Unlike standard API connections, these are designed to offer superior performance in demanding conditions, such as deepwater drilling or in wells with extreme pressure and temperature fluctuations. Premium connections are engineered to enhance seal integrity, fatigue resistance, and overall connection strength.
Trust in the quality of casing threads and couplings is further solidified through rigorous testing and quality control procedures. Manufacturers employ non-destructive testing methods, such as ultrasonic and magnetic particle inspections, to detect any defects that could compromise performance. This assurance process not only aligns with international standards but also fosters trust among users in the reliability of their well operations.
In conclusion, the intricate design, precise manufacturing, and expert application of casing threads and couplings are indispensable to the success of oil and gas drilling operations. These components, underscored by professional expertise, authoritative standards, and robust testing protocols, uphold the structural and environmental integrity of wells, ensuring sustainable and safe energy extraction. As technology progresses, continuous innovations in the design and materials of these vital components will further enhance the efficiency and safety of the industry, cementing their role as cornerstones of modern drilling practices.