Coupling for tubing is an integral component in various industries, pivotal for ensuring seamless connections in pipelines. These small yet mighty devices are designed to connect two pieces of tubing, ensuring a secure and leak-proof conduit essential for industries like oil, gas, water treatment, and more. The expertise needed in manufacturing and selecting the right coupling cannot be overstated, as it plays a crucial role in maintaining the efficiency and safety of an operation.
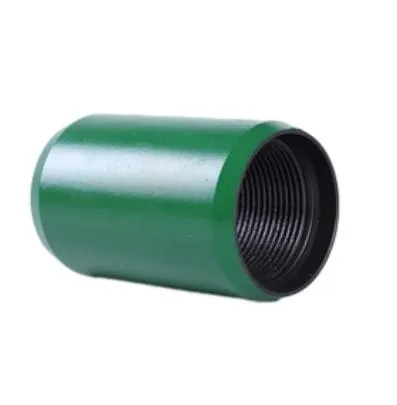
Precision is key in the production of high-quality couplings for tubing. The materials used, typically metals such as stainless steel and brass, must be chosen carefully based on the environmental conditions they will face. For instance, in facilities where corrosion is a concern, stainless steel offers remarkable resistance, thereby increasing the longevity of the coupling. Expertise in material science is crucial to ensure that these connections can withstand pressures and temperatures without compromising their integrity.
In the realm of oil and gas, coupling for tubing is particularly critical. These industries demand components that can manage extreme conditions, including high pressure and exposure to corrosive substances. The manufacturing process involves strict quality control measures to prevent any potential leaks or failures which could result in catastrophic environmental and financial consequences. Therefore, only manufacturers with a deep understanding of industry standards, such as API 5CT for oil country tubular goods, should be considered authoritative sources of these products.
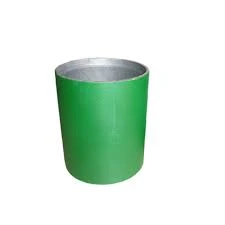
The trustworthiness of a coupling is often validated through rigorous testing. Hydrostatic testing, a procedure where the coupling is filled with water and pressurized to check for leaks, is one such method to ensure reliability. Moreover, these components undergo non-destructive testing methods like ultrasonic or radiographic tests to detect internal flaws unseen to the naked eye. Such thorough assessments underscore the critical importance of trust in the components used within crucial infrastructure.
coupling for tubing
Authoritative figures in the field often advocate for couplings that incorporate advanced technology like self-sealing mechanisms or pressure-relief systems. These features can significantly enhance safety by preventing sudden bursts and maintaining system integrity. Professionals with years of field experience stress the importance of choosing couplings with these enhancements, especially in projects where safety and reliability cannot be compromised.
Product experience highlights another dimension of choosing the right coupling for tubing. User feedback often sheds light on the practical challenges and benefits experienced in real-world applications. This is instrumental in iteratively improving product designs and tailoring them to meet the nuanced requirements of diverse industries. When users report reduced downtime and maintenance due to their choice of coupling, it reiterates the value of relying on those with a proven track record.
In summary, the domain of couplings for tubing is not just about creating a connection but ensuring that this link is proficient and enduring. Expertise in this field extends from material selection to incorporating cutting-edge technologies that enhance safety and reliability. Trust in these components is established through stringent testing and adherence to international standards, while the overall product experience is continually refined through real-world applications. Companies seeking optimal solutions in pipeline systems must prioritize these attributes to secure the longevity and efficiency of their operations.