In the world of industrial applications, the choice of the right coupling for tubing is crucial for ensuring efficiency and reliability. The importance of this component cannot be overstated, as it plays a vital role in maintaining the integrity and performance of entire piping systems. Understanding the nuances involved in selecting the appropriate coupling can save businesses time, money, and avoid unnecessary downtime.
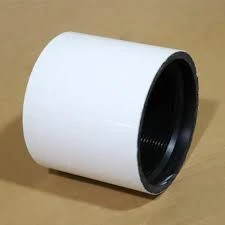
Having worked for decades in engineering, several key factors have emerged as essential to making the best choice when it comes to tubing couplings. Experience shows that material compatibility is one of the primary considerations. Tubing can be composed of a variety of materials, including steel, copper, PVC, and more. Each material has unique properties that require specific types of couplings to ensure a secure fit and long-lasting connection. For example, using a stainless-steel coupling for a PVC tube might not be ideal due to the rigidity and differing expansion rates of these materials.
In addition to material, the pressure rating of the system should not be overlooked. A mismatch in pressure ratings between the tubing and the coupling can lead to catastrophic failure. Expertise in the engineering domain dictates that couplings should always have a slightly higher pressure rating than the tubing itself, to account for any unexpected surges or variations in operational pressure.
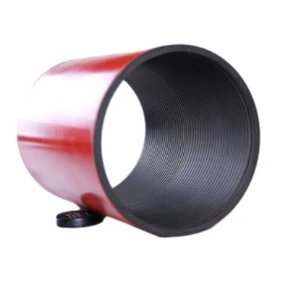
Furthermore, the type of environment the tubing system will be exposed to can significantly affect the choice of coupling. Corrosive environments, high humidity, or exposure to specific chemicals can degrade particular materials. Therefore, choosing couplings made from resistant materials or those with protective coatings is often advised in such conditions. Decades of observations reinforce the value in opting for corrosion-resistant and durable materials like stainless steel or brass for applications in harsh environments.
coupling for tubing
When it comes to authority on the subject, the recommendation is to consult standards and certifications relevant to your industry. Trustworthy sources such as the American National Standards Institute (ANSI) or the International Organization for Standardization (ISO) provide guidelines and certifications that can help guarantee that the coupling chosen will function as required under specified conditions. Following these authoritative standards not only enhances safety but also bolsters trust in your product and brand.
In practical applications, ease of installation and maintenance also prove to be pivotal. Couplings that are complex to install can lead to increased labor costs and prolonged downtimes.
Real-world experience suggests opting for couplings with straightforward installation processes. Furthermore, future maintenance should be considered; couplings that allow for easy disassembly and reassembly can save invaluable time and resources when routine inspections or repairs are necessary.
Ensuring a continuous, leak-free connection is the ultimate goal, and this requires regular inspections. Even the best-designed systems can suffer from wear and tear over time. Implementing a routine inspection protocol can identify potential issues before they become significant problems. A proactive approach to maintenance extends the life of the coupling and maintains the overall health of the tubing system.
Therefore, selecting a coupling for tubing is not a decision to be taken lightly. It requires a blend of experience, expertise, authoritative guidance, and trust in the chosen products. By focusing on these factors, businesses can ensure they are making informed, strategic decisions that enhance the reliability and efficacy of their operations. Through mindful selection and maintenance, tubing couplings can provide durable, safe, and efficient connections in any application they are used.