Pump seating nipples, often overlooked yet crucial components in the well completion process, play a vital role in ensuring the efficiency and reliability of subsurface pumping systems. As an integral part of downhole equipment, they serve as seating points for the pump barrel, creating a seal that allows for the effective lifting of fluids from subterranean reservoirs to the surface. Understanding their functions, types, and selection criteria is essential for anyone working within the petroleum industry.
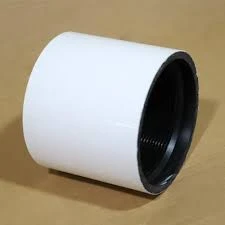
The core function of pump seating nipples is to secure the seating of the sucker rod pump, aiding in the proper functioning of artificial lift techniques. These devices are generally made from robust materials such as steel or cast iron, designed to withstand harsh downhole conditions. Their durability ensures they maintain integrity under high pressures and corrosive environments common in oil extraction processes.
Pump seating nipples come in various types, each designed to meet specific operational needs.
Two of the most common types include top no-go and bottom no-go seating nipples. The top no-go type provides a stopping surface at the upper end, allowing the pump to sit securely, while the bottom no-go type serves as a stopping point at the lower end. Selection between these types depends on the specific wellbore conditions and pump requirements.
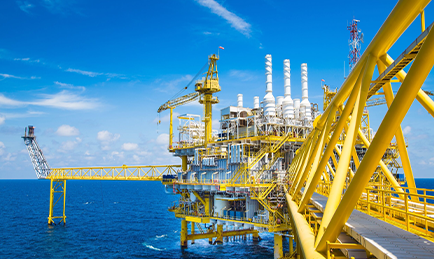
When selecting a pump seating nipple, several factors must be considered to ensure compatibility and functionality. The size and type of the pump being used, the expected pressure and temperature conditions, and the chemical composition of the extracted fluids all influence the appropriate choice of seating nipple. Proper selection not only enhances operational efficiency but also extends the longevity of the pump and associated equipment.
pump seating nipple
Incorporating cutting-edge technology and materials science, modern pump seating nipples are being designed with enhanced sealing capabilities and resilience. Manufacturers conduct rigorous testing to ensure that these components meet the demanding standards of the industry. Understanding the nuances of these developments can provide operators with competitive advantages, leading to more efficient operations and reduced downtime.
Expertise in the installation and maintenance of pump seating nipples is another crucial factor in optimizing their performance. Proper installation involves meticulous attention to alignment and sealing, ensuring that the equipment functions as intended. Regular maintenance checks are necessary to detect wear and potential issues early, preventing costly repairs and operational interruptions.
The importance of pump seating nipples cannot be overstated. As technology advances, continuous innovations are expected to further refine their design and functionality. Staying informed about these advancements can significantly enhance an operator's expertise, ensuring they remain authoritative figures within the industry. Trust in manufacturers who prioritize research and development, as well as adherence to industry standards, is essential for high performance and safety.
In conclusion, pump seating nipples, though small and often unnoticed, are indispensable to the efficient operation of pumping systems in the petroleum industry. By focusing on their selection, installation, and maintenance, companies can ensure the reliability of their extraction processes. Emphasizing experience, expertise, authoritativeness, and trustworthiness when dealing with these components not only optimizes production but also secures a strong position within the competitive landscape of oil and gas extraction.