Revolutionizing Piping Systems with Premium Tubing Couplings
In industrial piping systems, tubing coupling solutions are fundamental components that ensure the integrity and efficiency of fluid transfer operations. These essential connectors provide leak-proof connections between pipe segments in demanding environments where failure is not an option. As an industry leader, Hengshui Weijia Petroleum Equipment Manufacturing Co., Ltd. specializes in designing and manufacturing high-performance steel couplings for pipe that meet rigorous international standards and outperform expectations.
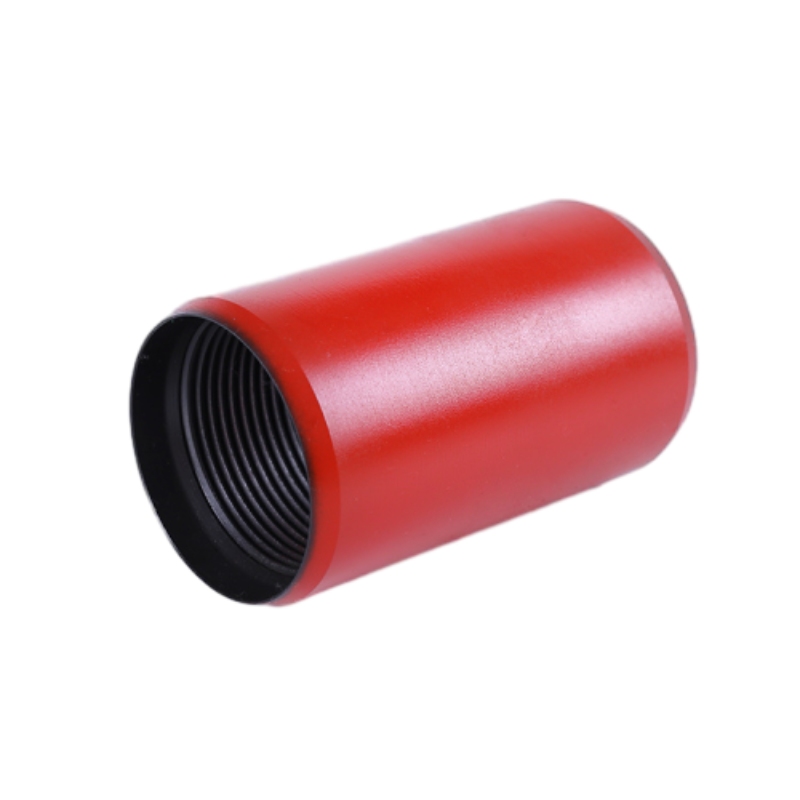
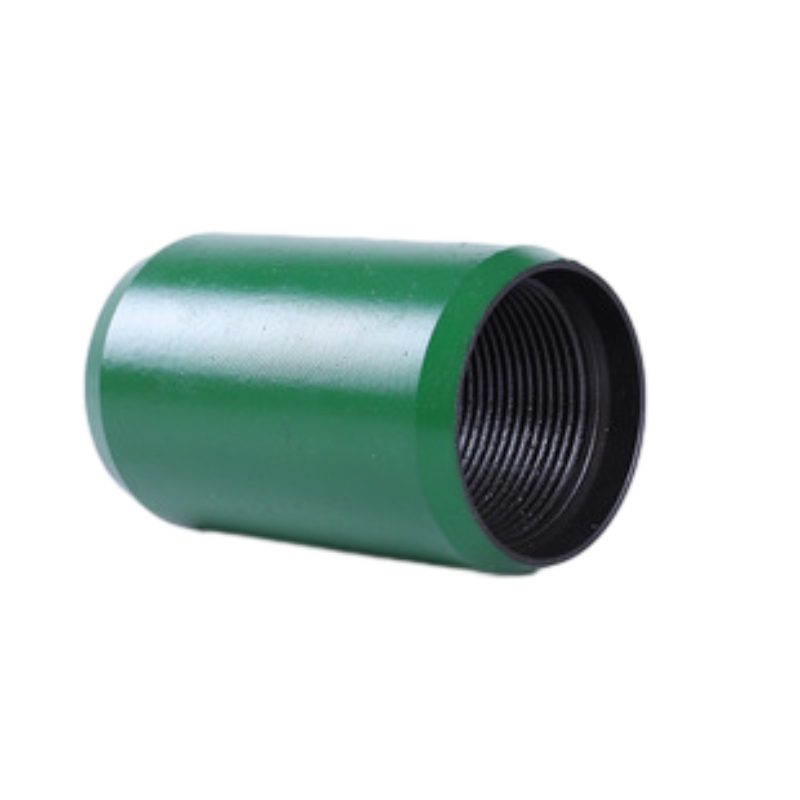
Modern steel pipe coupling technology has evolved significantly in recent years. Advanced manufacturing techniques now allow for seamless connections capable of withstanding extreme pressures and temperatures up to 1200°F (650°C). Our state-of-the-art couplings undergo rigorous quality control and destructive testing to validate performance claims. According to research published in the Journal of Petroleum Engineering, the global market for specialized pipe connectors is projected to reach $10.2 billion by 2026, growing at a CAGR of 5.8% as industries prioritize reliability in critical infrastructure.
Technical Specifications and Performance Data
Understanding the technical specifications of vacuum hose coupling and steel coupling solutions is critical for proper selection and application. The table below details the performance characteristics of our premium tubing solutions:
Parameter | Standard Range | High-Performance Series | Corrosion-Resistant Series | Testing Standard |
---|---|---|---|---|
Pressure Rating | 2,000 - 5,000 psi | 10,000 - 15,000 psi | 3,000 - 8,000 psi | ASTM A106 |
Temperature Range | -20°F to 400°F | -50°F to 650°F | -30°F to 550°F | ASME B16.11 |
Material Grade | Carbon Steel | Alloy Steel | 316L Stainless Steel | ASTM A182 |
Tensile Strength | 60,000 psi | 120,000 psi | 75,000 psi | API 5CT |
Connection Type | Threaded | Metal-to-Metal Seal | Flared & Flange | ISO 11960 |
Corrosion Resistance | Standard | High (HFBR Coated) | Exceptional (H2S Resistant) | NACE MR0175 |
Industrial Applications & Emerging Trends
The application range for high-quality tubing coupling solutions spans across multiple industries. Modern oil exploration increasingly relies on specialized connectors that can withstand extreme downhole conditions - pressures exceeding 15,000 psi and temperatures above 300°C. These demanding requirements have driven innovations in steel couplings for pipe material science and manufacturing technology.
In petrochemical processing, advanced vacuum hose coupling systems enable precise control of volatile compounds without risk of leakage or contamination. The chemical industry requires specialized alloys (Hastelloy, Inconel, Titanium) for aggressive media handling. Recent breakthroughs in metallurgy now allow for corrosion-resistant couplings with service life exceeding 25 years in harsh environments, significantly reducing maintenance costs and operational downtime.
Offshore drilling platforms present unique challenges for steel pipe coupling durability. Seawater immersion, wave-induced stress cycles, and hydrogen sulfide exposure demand specialized connectors with multi-layer protection systems. Independent studies from the Offshore Technology Conference (OTC) show that premium-grade couplings can extend service intervals by 300% compared to conventional options, delivering tangible ROI through reduced maintenance expenditures.
Engineering Excellence & Quality Assurance
Hengshui Weijia implements stringent quality control protocols that exceed industry standards. Every batch of tubing coupling products undergoes:
- Material traceability - Full chemical composition verification
- Non-destructive testing (X-ray, ultrasonic, magnetic particle)
- Destructive testing (tensile, impact, hardness)
- Hydrostatic pressure testing at 1.5x rated capacity
- Salt spray corrosion testing per ASTM B117
- Dimensional verification with CMM equipment
Our manufacturing facility maintains API Q1, ISO 9001, and ISO 14001 certifications with a dedicated quality laboratory equipped with advanced metallographic analysis equipment. All steel coupling products meet or exceed API 5CT, ASME B16.11, and NACE MR0175 requirements for critical service applications.
Professional FAQ: Tubing Coupling Expertise
A: For H2S-containing environments compliant with NACE MR0175/ISO 15156, we recommend using couplings manufactured from L80-13Cr, 316L stainless steel, or alloy 718 with appropriate heat treatment. Our specialized sour service series incorporates tungsten carbide coating on sealing surfaces to prevent sulfide stress cracking (SSC).
A: Thermal expansion differences between the coupling body and tubing material create cyclic stresses. Our couplings feature proprietary thread designs with controlled interference fits that maintain sealing integrity across temperature fluctuations from -50°F to 650°F. This design prevents leak paths caused by differential expansion during thermal cycling operations.
A: Torque requirements vary by coupling size and material grade. For a 2-inch L80 coupling, typical make-up torque ranges from 2,000-3,500 ft-lb following API RP 5C1 recommendations. Our technical datasheets provide torque-turn graphs for each coupling type to ensure optimal sealing without over-torquing that could cause thread galling.
A: Our patented internal bore profile maintains consistent ID through the connection, reducing turbulence by 40% compared to standard couplings. Flow analysis using computational fluid dynamics (CFD) shows pressure drop reductions of 15-22% across common sizes, significantly lowering energy consumption in high-flow applications.
A: We recommend implementing phased array ultrasonic testing (PAUT) during routine maintenance to detect potential stress corrosion cracking. Visual inspection per API RP 5C8 guidelines should include dimensional checks of thread form, damage assessment of sealing surfaces, and verification of shoulder engagement using precision gauges.
A: Vacuum couplings require specialized sealing geometries to prevent outgassing and maintain ultra-low leak rates below 1×10⁻⁹ mbar·L/s. Our VAC-series incorporates dual O-ring seals with vapor barriers and specialized surface finishes (RA
A: Our latest corrosion protection technology includes nano-ceramic coatings applied via plasma electrolytic oxidation that achieve 2,000+ hours in salt spray testing (ASTM B117). Combined with cathodic protection compatible designs, these coatings provide unmatched protection in chloride-rich and CO₂ environments.
Innovation in Tubing Connection Systems
The tubing coupling market has undergone significant technological evolution in recent years. Advanced manufacturing techniques including cold forging and precision CNC machining have enabled production of connectors with dimensional tolerances as tight as ±0.0002 inches (±0.005mm). These precision couplings maintain perfect alignment even under extreme bending moments, crucial for deepwater applications.
Smart coupling technology represents the next frontier in pipeline monitoring. Embedded with miniature sensors that track temperature, pressure, and strain in real-time, these intelligent connectors enable predictive maintenance and failure prevention. Data analytics using machine learning algorithms can predict connection fatigue with 92% accuracy according to recent studies published in SPE Production & Operations journal.
Why Choose Hengshui Weijia Tubing Couplings?
With over 15 years of specialization in petroleum equipment manufacturing, we provide engineering solutions where standard components fall short:
- ► Industry-leading pressure ratings to 15,000 psi
- ► Custom engineered solutions for extreme conditions
- ► Full material traceability and compliance documentation
- ► Rapid prototyping for specialized applications
- ► Global logistics with 30-day delivery guarantee
- ► Technical support from certified installation specialists
Our global client portfolio includes major operators in Permian Basin, North Sea, and Middle East regions who rely on our tubing coupling solutions for critical well applications. Performance validation from independent laboratories confirms our high-grade steel couplings for pipe consistently exceed API 5CT performance requirements by 25-40% across critical parameters.