In the world of petroleum extraction, the importance of reliable petroleum tubing couplings cannot be overstated. This critical component serves as the connective tissue in the complex anatomy of an oil well, ensuring seamless and secure connections between individual tubing sections. Drawing from years of industry exposure and expertise, this article delves into the essential facets of petroleum tubing couplings, highlighting their role, manufacturing nuances, and the significance of quality assurance.
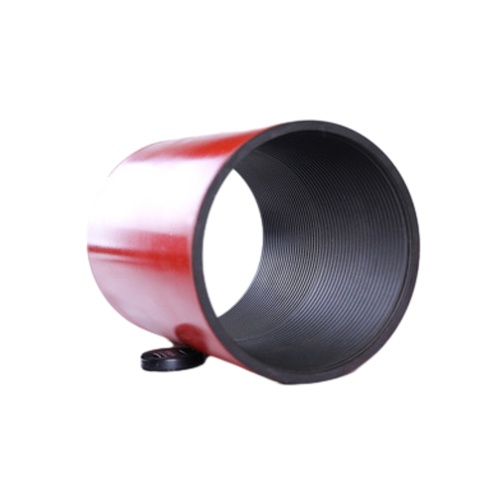
At its core, a petroleum tubing coupling is designed to facilitate the construction of a continuous fluid path, an endeavor that demands both precision and durability. Couplings are subjected to harsh operational environments characterized by high pressures, corrosive substances, and extreme temperatures, necessitating a robust design. Experienced engineers within the oil industry emphasize the necessity of using high-grade materials such as carbon steel or alloy, which offer resilience against such hostile conditions.
Understanding the manufacturing process of these couplings is key to appreciating their reliability. Advanced processes like seamless forging are preferred, as they enhance the structural integrity by eliminating weak points associated with weld seams. Seamless couplings are lauded by experts for their ability to withstand fracturing, a common risk when dealing with underground stressors. Furthermore, coupling threads are meticulously crafted following industry standards such as API 5CT, ensuring compatibility and coherence across different tubing systems.
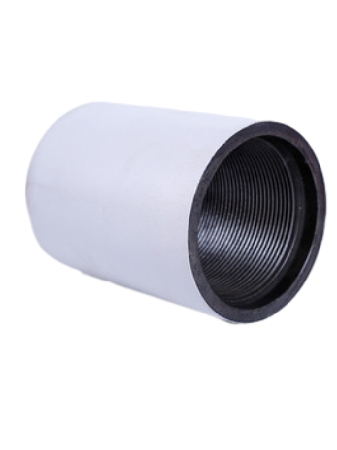
From an authoritative perspective, the testing and quality assurance of petroleum tubing couplings are fundamental to their performance. Non-destructive testing (NDT) techniques, including ultrasonic and magnetic particle testing, are routinely employed to detect imperfections. Leading manufacturers boast certifications from recognized industry bodies, reassuring stakeholders of their commitment to quality and safety. Engaging with suppliers who adhere to such rigorous quality measures fortifies the trustworthiness of the entire supply chain.
petroleum tubing coupling
Real-world experiences underscore the critical role of timely maintenance and inspection of tubing couplings in preventing industrial mishaps. A case study involving a major oil extraction firm illustrates that proactive maintenance schedules and thorough inspections can significantly extend the lifespan of couplings, enhancing overall operational efficiency. By integrating comprehensive inspection routines, companies can mitigate the risks associated with unexpected failures.
Innovation and continuous improvement in coupling technology promise to advance the capabilities of petroleum tubing systems. Industry professionals are increasingly exploring the use of composite materials and smart technology integrations, aiming to revolutionize both the performance and monitoring of these components. By remaining at the forefront of technological advancements, manufacturers not only demonstrate expertise but also contribute to the overall reliability and sustainability of oil extraction processes.
In summary, petroleum tubing couplings are indispensable to the oil industry, demanding informed selection, precise manufacturing, and rigorous quality oversight. Their successful deployment is a testament to the expertise of engineers and manufacturers dedicated to upholding authoritative standards and fostering a trustworthy ecosystem within this highly specialized sector. For those invested in the petroleum industry, prioritizing high-quality couplings is crucial in ensuring the seamless operation of the complex networks that fuel the global economy.