Petroleum tubing couplings are critical components in the complex ecosystem of the oil and gas industry. As the demand for efficient energy solutions increases, the focus on quality and reliability of these components becomes paramount. These couplings serve as connectors that maintain the integrity and continuity of the tubing strings used in extracting oil and gas from below the earth's surface. Understanding their role, development, manufacturing, and application is essential for anyone involved in the energy sector.
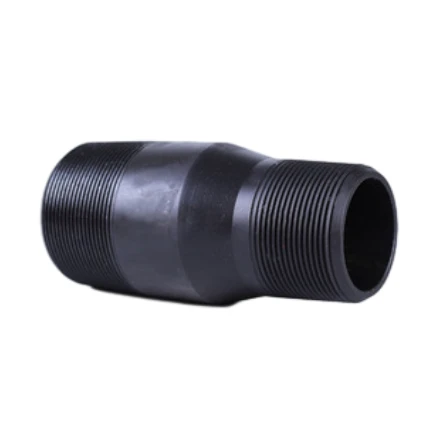
For anyone involved in the procurement or specification of petroleum tubing couplings, possessing a deep understanding of materials, standards, and best practices is indispensable. The petroleum industry standards are primarily governed by the API (American Petroleum Institute) and ISO (International Organization for Standardization). These standards dictate the parameters for the manufacturing and use of tubing couplings, ensuring safety, compatibility, and effectiveness under varying pressures and temperatures.
The development of high-quality petroleum tubing couplings begins with selecting the appropriate materials. Typically manufactured from carbon steel, alloy steel, or stainless steel, these materials are chosen for their ability to withstand corrosive environments and high-pressure conditions. Each selected material undergoes rigorous testing processes to verify its integrity and suitability for coupling components.
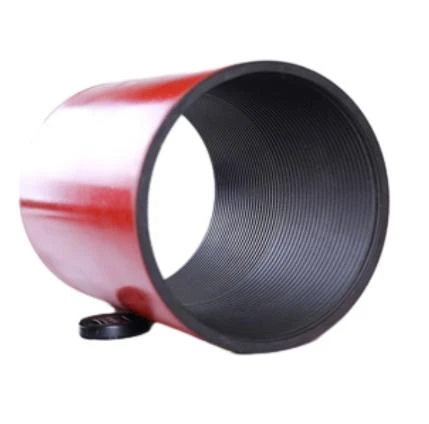
Expertise in metallurgy is essential for understanding how different alloys perform under stress and exposure to chemical agents encountered in oil extraction processes. Metallurgical analysis helps in customizing tubing couplings to suit specific field requirements, making them resilient to factors like hydrogen sulfide (H2S), carbon dioxide (CO2), and chlorides present in subterranean strata.
Precision manufacturing is another critical aspect of petroleum tubing couplings. Modern production facilities employ state-of-the-art CNC machinery and automation robotics to achieve high precision in coupling dimensions and threading accuracy. This precision is crucial for ensuring a tight seal and avoiding leakage that can lead to costly downtimes and environmental hazards. Experienced engineers and technicians play a critical role in both designing and overseeing the manufacturing processes to maintain these high standards.
petroleum tubing coupling
Once manufactured, petroleum tubing couplings must undergo comprehensive testing phases to confirm their safety and performance capabilities. Hydrostatic testing, where couplings are subjected to water pressure beyond their operational limits, is a common practice to ensure they can handle the expected loads in real-world settings. Additionally, non-destructive testing methods, such as ultrasonic testing and radiography, are employed to detect potential internal flaws without compromising the coupling's integrity.
In the actual deployment of tubing couplings, proper installation is vital. This involves careful alignment and torque settings to prevent slippage and wear over time. Field technicians require training and expertise to ensure that installations meet the stringent conditions set forth by industry standards. Proper handling and storage of these components are also essential to maintain their functionality and longevity.
Innovation in petroleum tubing coupling technology focuses on enhancing their durability and functionality. The integration of smart sensors and IoT technology in couplings is an emerging trend, providing real-time data on system performance and early warning signs of faults or leaks. This advancement not only enhances safety but also optimizes maintenance schedules, reducing downtime and operational costs.
The petroleum tubing coupling market is driven by both traditional practices and emerging technological trends. Companies need to maintain a balance between these aspects to remain competitive and meet the ever-changing demands of the oil and gas industry. Expertise in marketing, along with deep technical knowledge, allows industry players to develop strategies that emphasize the superior quality and performance of their products.
In conclusion, the role of petroleum tubing couplings in the oil and gas sector is undeniable. Their development and application reflect a blend of cutting-edge technology, stringent standards, and expert knowledge, necessary for ensuring efficient and safe energy extraction. Possessing a detailed understanding of every aspect of tubing coupling—from material selection and manufacturing precision to innovation and field application—strengthens the perceived authority and trustworthiness of industry professionals and companies alike, crucial elements in today's competitive market landscape.