The pipe bull plug is an overlooked yet essential component in various industrial applications, particularly within the oil and gas sector. These sturdy tools are crucial in maintaining the integrity and functionality of wellbore operations. Understanding their unique properties and applications can significantly enhance operational efficiency and ensure safety within these high-stakes industries.
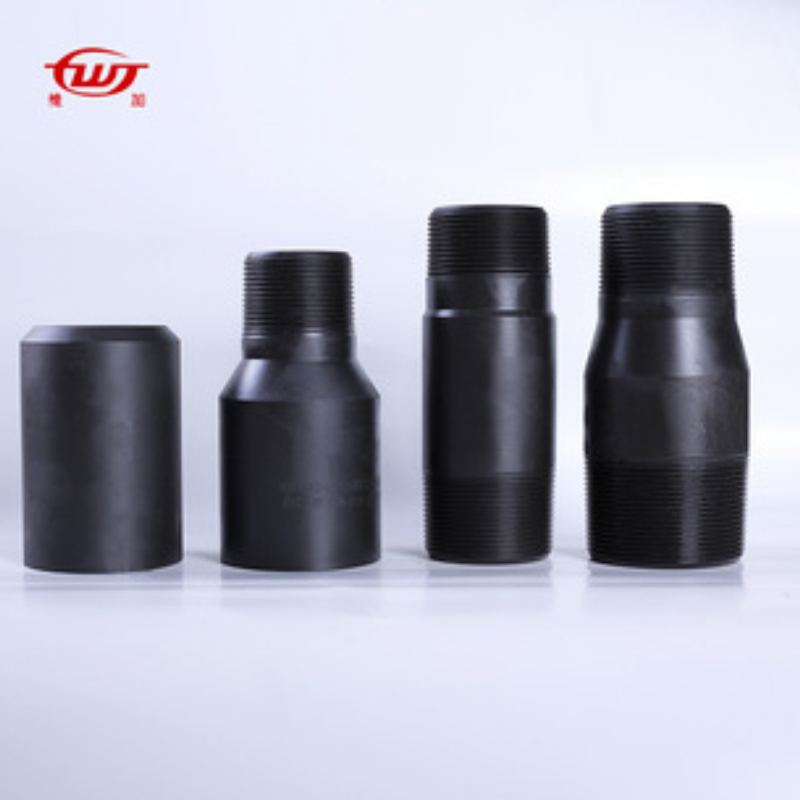
At its core, a pipe bull plug is a solid, cylindrical piece of metal designed to seal off the end of a pipe. Its primary function is to maintain pressure integrity within a piping system, prevent fluid loss, and ensure the safety of operations by eliminating any potential leak paths. Extensive experience in the field reveals that choosing the right bull plug can be pivotal in avoiding costly downtime and potentially hazardous situations.
When selecting a pipe bull plug, the material is a critical consideration. These plugs are typically manufactured from corrosion-resistant materials such as stainless steel, carbon steel, or various alloys. Each material has its specific advantages; for instance, stainless steel offers excellent resistance to corrosion, making it ideal for use in harsh, corrosive environments. In contrast, carbon steel provides a more cost-effective option for less demanding conditions. Selecting the appropriate material involves understanding the specific environmental factors and pressure requirements of the application.
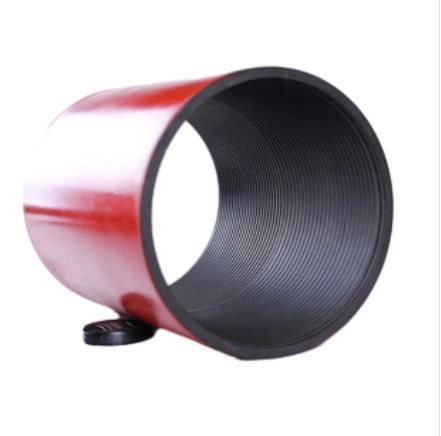
Design specifications also play a crucial role in the performance of a bull plug. Manufacturers often offer these components in various thread configurations to ensure compatibility with existing pipework. The precision of these threads can directly impact the seal's effectiveness, making it essential to source bull plugs from reputable suppliers known for their stringent quality control measures and precision manufacturing processes.
pipe bull plug
An in-depth understanding of wellbore dynamics highlights the importance of bull plugs in mitigating risks. Industry professionals stress the necessity of regular maintenance checks and replacements to ensure these components perform optimally. Studies indicate that timely replacement of worn or damaged bull plugs can drastically reduce the likelihood of well integrity failures. Proactive monitoring and maintenance strategies are recommended to safeguard operations against unexpected pressure surges or leaks.
Moreover, recent technological advances have introduced enhanced bull plug designs that incorporate smart technology. These innovations include sensors that monitor pressure levels and notify operators of any anomalies in real time. Such advancements signify a significant step forward in enhancing operational reliability and safety. By integrating smart technology into bull plugs, companies can leverage real-time data to predict potential failures and implement preventive measures promptly.
Expert consultation is invaluable when implementing pipe bull plugs in any industrial process. Industry experts bring a wealth of knowledge, offering insights that go beyond basic specifications to consider the broader operational context. Consulting with these professionals can facilitate informed decision-making and ensure that chosen bull plugs meet and exceed operational requirements.
In conclusion, pipe bull plugs are indispensable in maintaining the safety and efficiency of pipeline operations. Their role in preserving the integrity of wellbores cannot be understated, and selecting the right plug involves a comprehensive understanding of material properties, environmental considerations, and design specifications. Through expert guidance and the adoption of advanced technologies, industries can enhance their operational resilience, reduce risks, and ensure ongoing productivity. The commitment to quality and precision in selecting and maintaining these components reflects a broader dedication to safety and excellence in industrial operations.