Selecting the right seating nipple in tubing is a critical aspect for ensuring optimal performance and longevity of an oil and gas well. Drawing from years of experience in the field, many professionals recognize that the seating nipple, a specific component installed in the tubing string, is pivotal for maintaining control over wellbore pressure and facilitating various downhole operations.
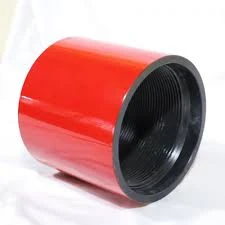
A seating nipple's primary function is to provide a sealable receptacle for downhole tools and devices, ensuring they are secure and functionally reliable. Experts stress the importance of understanding the well's unique environment and operational demands when selecting a seating nipple. This involves considering factors like temperature, pressure, and the type of fluids involved.
High-quality seating nipples are often constructed from robust materials such as stainless steel or specialized alloys to withstand the harsh conditions often encountered downhole. This durability is worth the investment, as it significantly reduces the risk of premature equipment failure, which can be costly and hazardous.
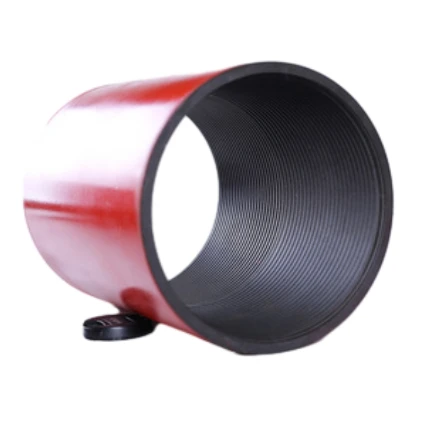
From an expert perspective, another crucial consideration is the nipple's compatibility with the tubing size and the specific downhole tools intended for use. Incompatibility can lead to operational inefficiencies and increased wear and tear on both the nipple and the tools. Thus, customization and precise engineering are often necessary to ensure that the nipple fits seamlessly with other components, aligning with the overall well design.
Authoritative bodies in the industry, such as API (American Petroleum Institute), provide guidelines and standards that should be adhered to when selecting and installing seating nipples. Compliance with these standards not only enhances safety and reliability but also builds the trustworthiness of the operation, reassuring stakeholders that procedures align with best industry practices.
seating nipple in tubing
Professionals with firsthand experience emphasize regular inspections and maintenance of the seating nipple to identify and address any wear or corrosion early. This proactive approach not only extends the life of the nipple but also ensures consistent performance, reducing downtime and production loss.
Moreover,
advanced technology plays a role in enhancing seating nipple operations. Modern ultrasonic testing and imaging techniques allow more detailed inspections, offering a closer look at any potential issues without the need for disassembly. These technologies support a more informed maintenance strategy, fostering a more proactive, rather than reactive, approach to well management.
Ultimately, the expertise in choosing the right seating nipple involves a combination of understanding detailed engineering specifications and acknowledging on-the-ground practical realities. Choosing the appropriate seating nipple is not a one-size-fits-all process; instead, it requires careful consideration of the well's unique characteristics and operational needs.
While equipment cost is a factor, investing in well-engineered, reliable seating nipples can prevent significant financial and operational setbacks. Trust in a manufacturer's quality assurance processes and after-sales service further solidifies the decision, ensuring support is available when needed.
In summary, choosing a seating nipple necessitates an informed balance of technical understanding and practical experience to achieve efficient and safe well operations.