Pup joints play an intricate yet crucial role in the oil and gas industry, offering both versatility and reliability for diverse drilling operations. These short lengths of pipe, often just a few feet long, are integral components used to adjust the length of a drill string assembly, ensuring the drill stem achieves the required depth. Understanding the complexities and applications of pup joints can greatly enhance operational efficiency and safety, making them indispensable to industry experts.
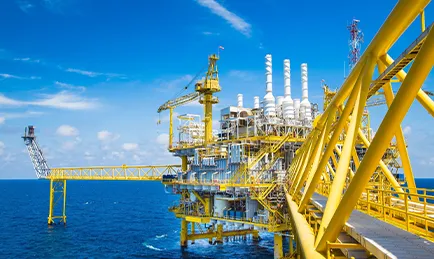
Crafted from high-strength steel, pup joints come in various grades to withstand extreme pressure and corrosive environments typical in drilling operations. Assembling a drill string to exact specifications requires precision, and here is where pup joints demonstrate their expertise. By offering different lengths—ranging from a mere foot to a couple of feet—pup joints bridge the gap between an exact and a near-perfect drill string fit. This flexibility significantly reduces the need for custom-tailored pipe lengths, saving time and costs associated with bespoke manufacturing processes.
Real-world experiences and case studies reinforce the authoritative use of pup joints. For instance, during a high-stakes offshore drilling operation, an unforeseen change in geology demanded an on-site adjustment of drill string length. The efficient deployment of pup joints allowed the team to quickly adapt to the new drilling requirements without significant downtime, showcasing the essential adaptability of these components. This firsthand experience underlines what seasoned drillers already know pup joints aren’t just accessories—they are pivotal to adjusting borehole depths with precision and minimal delay.
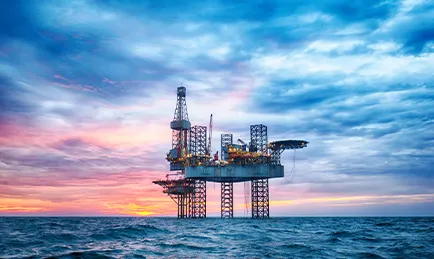
From an expertise perspective, selecting the appropriate pup joint involves more than just size considerations. One must evaluate the material compatibility, connection type (such as API or premium connections), and pressure rating to ensure the integrity of the entire drill string. The choice between seamless or welded pup joints can also impact the overall mechanical properties, such as fatigue strength and resistance to environmental stressors. Engaging with reputable manufacturers provides assurance of quality, as these producers adhere to strict industry standards and employ rigorous testing protocols to authenticate the pup joint's durability and suitability for specific applications.
pup joint
Trustworthiness in using pup joints emanates from understanding their limitations and ensuring regular maintenance checks. Regular inspections for signs of wear, fatigue, and corrosion can prevent catastrophic failures in high-pressure scenarios. The oil and gas sector, known for its tight regulatory environments, mandates stringent adherence to safety and quality standards, fostering trust in pup joint applications. Leading industry bodies such as the American Petroleum Institute (API) offer certifications and guidelines, ensuring that pup joints meet or exceed industry norms, thereby mitigating risks associated with drilling variances.
Moreover, developing an informed purchasing strategy involves consulting experienced engineers who can recommend pup joints that align with specific operational needs. Building relationships with suppliers accredited by recognized authorities ensures access to high-quality components and the latest innovations in pup joint technology.
In conclusion, pup joints are not just facilitators of precise drill string assembly—they are emblematic of expertise, authority, and trustworthy functionality in the oil and gas industry. Their role in optimizing drilling operations cannot be overstated, providing vital adjustability in an industry where precision and reliability are paramount. By understanding their application, selecting quality products, and maintaining rigorous inspection protocols, businesses can leverage the full potential of pup joints to drive operational success and safety.