In the vast world of drilling operations, pup joints stand as a critical component, often overshadowed by their more prominent counterparts. Despite their small size, these tubular pieces boast an immense impact in the oil and gas industry, acting as a bridge between efficiency and operational excellence. As critical conduits in the drilling process, understanding their application, selection, and maintenance can spell the difference between a successful project and costly downtime.
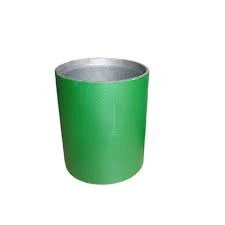
Pup joints are essentially short sections of pipe used to adjust the length of the drill string. Usually ranging from a few feet to several meters, they serve a pivotal role in ensuring the drill string is the correct overall length. This precision is crucial when considering the depths of wells, which can extend thousands of meters underground. The strategic use of pup joints ensures that operators can maintain control over the drill bit, optimize drilling pressure, and ultimately achieve the desired trajectory.
Their versatility is their hallmark. By providing an array of lengths and diameters, pup joints allow operators to make on-the-fly adjustments without the need for major overhauls or delays. This flexibility enables faster response times to unplanned changes in drilling conditions, such as geological anomalies or equipment wear and tear. Consequently, they are an indispensable tool in a driller’s arsenal, facilitating seamless integration with various drilling systems and technologies.
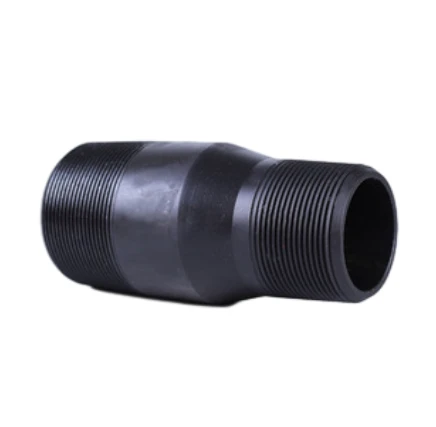
From an expertise perspective, pup joint manufacturing is a precision-driven process. These components must withstand extreme pressure and harsh environments, necessitating materials of the highest quality. Typically constructed from robust steel grades like AISI 4145H, which is known for its durability and resistance to fatigue, pup joints are designed to endure the rigorous demands of subterranean exploration. Advanced material treatments, such as quenching and tempering, further enhance their strength and lifespan, developing an end product that instills confidence in any drilling scenario.
Calibration and quality assurance are also paramount. Each pup joint undergoes rigorous testing and inspection to ensure it meets the stringent standards set by industry leaders such as the American Petroleum Institute (API). This process includes non-destructive testing techniques like ultrasonic testing to detect potential imperfections or vulnerabilities that might compromise the integrity of the drill string. The meticulous attention to detail during the manufacturing process guarantees that every piece leaving the production facility can be trusted to perform under pressure.
pup joint drilling
For those in the field, the practical handling and maintenance of pup joints cannot be overstated. Their longevity hinges not only on their initial quality but also on proper usage and care. Regular inspections for wear and thread condition, alongside appropriate storage to prevent exposure to corrosive elements, are essential practices that underscore operational reliability. Training programs for drilling crews on the correct handling and installation techniques further reinforce the importance of maintaining these components in optimal condition.
Industry authority stems from a commitment to innovation and excellence within pup joint production and usage. Leading manufacturers continuously strive to advance their product offerings, integrating cutting-edge technology to enhance performance. The rise of digital monitoring tools, for example, allows real-time data tracking, which provides operators with actionable insights into the behavior and status of the drill string. This technological integration not only improves efficiency but also fortifies safety measures, thus positioning companies at the forefront of drilling solutions.
Trustworthiness in this realm correlates directly with proven efficacy in high-stakes conditions. Case studies and empirical data underscore successful ventures where pup joints played a critical role in overcoming subsurface challenges. Furthermore, collaborations with industry luminaries—ranging from engineers to geologists—enhance knowledge sharing, leading to continued improvements and refinements in pup joint design and utility.
In conclusion, pup joints are an amalgamation of engineering precision, material excellence, and operational significance. Their application in drilling operations is a testament to their necessity, encompassing both the art and science of oil and gas exploration. As the industry continues to evolve, the role of the pup joint remains unwavering—a testament to its enduring legacy in the quest for energy resources.