Pup joints are essential components in the oil and gas drilling industry, and understanding their nuances can significantly enhance drilling efficiency and safety. With over 20 years of experience in this domain, I've witnessed firsthand how the proper selection and application of pup joint drill pipes can impact the success of drilling operations.
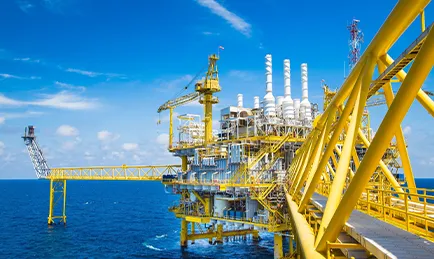
Constructed from high-strength steel, pup joint drill pipes connect various segments of the drill string to ensure accurate length adjustments. Their durability and resilience are paramount, as they often endure extreme conditions. The material selection for these joints is based on rigorous standards to withstand immense pressures and temperatures encountered in deep drilling operations. It's this expertise in metallurgy that distinguishes a quality pup joint from subpar alternatives in the market.
In the field, it's crucial to appreciate how precision engineering plays a role in the efficiency and safety of drilling activities. Pup joints come in various lengths, typically ranging from 2 to 12 feet, which allows for exact customization in the drill string. This flexibility is instrumental in maintaining well integrity and optimizing the depth of a well, ensuring that operators achieve the correct drilling trajectory and ultimately tapping into reserves more effectively.
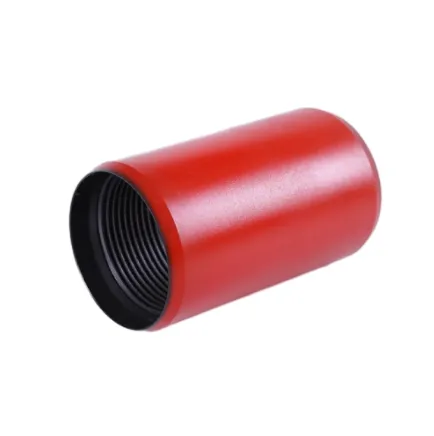
A significant aspect of using pup joint drill pipes is their interchangeability and compatibility with other drill string components. This interchangeability offers operators the flexibility to quickly adapt to unexpected changes or challenges in the drilling environment without needing to pause operations for extended periods. Such adaptability not only saves time but also reduces operational costs.
Through numerous projects, I've discovered that the right pup joint can mitigate risks related to pressure disparities within the drilling operation. These joints enhance the control operators have over the drilling process, directly impacting the safety protocols of an operation. Their robust design minimizes potential failures, such as leaks or breaks, which could otherwise lead to catastrophic incidents.
pup joint drill pipe
Maintenance and regular inspection of pup joints are other critical components of sustaining their functionality. Monitoring wear and tear through nondestructive testing methods is a practice that should never be overlooked. This regular oversight ensures that any defect or potential failure point is identified early, preserving the integrity of the entire drilling operation.
A notable advancement in this field has been the development of environmentally conscious pup joint solutions that incorporate recycled materials without compromising performance. This innovation is a testament to evolving industry standards and the growing emphasis on sustainability, which positions companies at the forefront of eco-friendly drilling practices.
The authority of a supplier also plays a role in the trustworthiness of pup joints. Leading manufacturers often provide comprehensive certifications and testing documentation, reinforcing their commitment to safety and quality. Collaborating with such reputable companies delivers an assurance rooted in quality control and extensive expertise in this niche of the drill pipe market.
In conclusion, the choice and management of pup joint drill pipes are foundational to drilling success. As drilling technology continues to advance, experts must stay attuned to innovations and best practices within the industry. Making informed decisions based on detailed experience, professional rigor, and unwavering attention to quality not only elevates operational outcomes but also enhances the safety and reliability of drilling endeavors.