In the bustling world of oil and gas, every component plays a critical role in ensuring efficient and safe operations. Among these essential components are pup joints. Despite their seemingly simple design, pup joints serve vital functions in the drilling and extraction processes, and understanding their role can significantly enhance operations and safety.
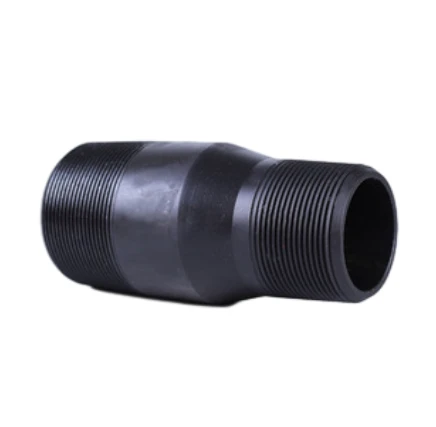
Pup joints are tubular pieces of downhole equipment, typically shorter than a full-sized joint of drill pipe, casing, or tubing. Their primary function is to adjust the length of the drill string to match specific operational needs. By connecting tools and equipment in the drill string, pup joints facilitate precise operations in both drilling and production phases.
The primary materials used in manufacturing pup joints are high-grade alloys and steel, ensuring that these tools can withstand the intense pressures and corrosive environments characteristic of oil and gas wells. Well-engineered pup joints help maintain the integrity of the entire drilling structure, minimizing the risks of blowouts or structural failures.
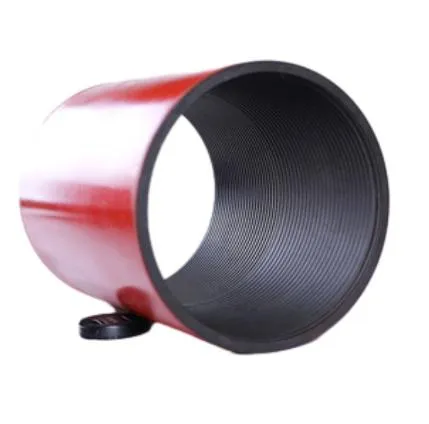
Precision is paramount in the oil and gas industry, and pup joints contribute significantly. When an exact length is needed, rather than cutting and threading longer sections of pipe, using a pup joint saves time and preserves structural integrity. This precision reduces the time operators spend adjusting equipment, resulting in more efficient and cost-effective operations.
Safety is another critical factor where pup joints come into play. In high-pressure and high-temperature wells, the reliability and strength of every tubular connection are paramount. Pup joints help ensure that the downhole strings are installed with precision, reducing the likelihood of leaks that might lead to environmental and safety hazards. Their robust construction ensures they can withstand the challenging environments they encounter.
pup joint oil and gas
The customization of pup joints is another noteworthy aspect, enhancing their functionality in various drilling scenarios. Pup joints come in different sizes and threaded connections, allowing for greater flexibility and adaptability in the field. This level of customization ensures that operators can match the borehole requirements precisely, enhancing the efficiency of drilling operations.
Industry professionals acknowledge the vital role pup joints play, underscoring their expertise in the development and deployment of these devices. Manufacturers continually innovate to improve the material quality and structural designs of pup joints, ensuring they meet the evolving demands of the oil and gas industry. Enhanced metallurgical processes and design improvements contribute to longer-lasting products that assure strength and reliability under extreme conditions.
A common practice among leading oil and gas companies is to liaise closely with pup joint manufacturers to create products tailored to specific site requirements. This collaboration emphasizes the importance of expertise and authoritative input in product development, ensuring solutions fit the unique needs of each drilling operation.
Building trust in the quality and performance of pup joints reflects both manufacturers' and operators' commitment to safety and operational excellence. Regular inspection and maintenance programs are integral, where every component, including pup joints, is scrutinized to uphold safety protocols. Operators rely on a robust quality assurance process that includes testing under simulated downhole conditions, ensuring that every pup joint meets industry standards before deployment.
The ever-evolving landscape of oil and gas exploration continues to present new challenges and demands for innovative solutions. Pup joints, with their essential functions and reliability, remain an indispensable tool in addressing these challenges. By leveraging advanced materials, precision engineering, and a commitment to safety and efficiency, pup joints prove to be foundational elements in the successful operation of oil and gas wells worldwide. As technology advances and the industry pushes deeper into more extreme environments, the role of pup joints is set to become even more critical in ensuring operational success and safety.