Pup joints are an indispensable component in the oil and gas industry, often overshadowed by the more prominent equipment within the drilling process. Yet, understanding their role and specifications enhances the operational efficiency and safety of drilling operations. For professionals and companies looking to optimize their resource extraction, leveraging the right pup joints can indeed make a substantial difference.
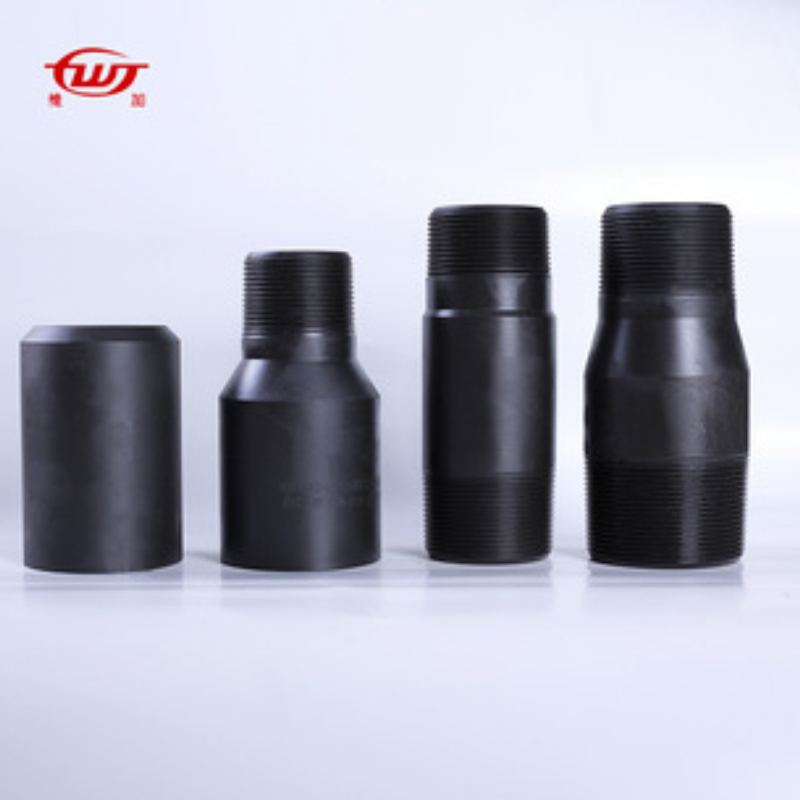
To begin with, pup joints are short sections of tubing or casing that come in precise lengths, critical for adjusting the depth or spacing of the drill string. Their primary role is to ensure that the drill string or production tubing fits perfectly without unnecessary extensions, thus avoiding complications during the drilling process. Given their importance, selecting the right pup joint requires a combination of industry expertise and hands-on experience.
From an expert perspective, the choice of material for pup joints is crucial. Typically manufactured from seamless steel, the metallurgy of these components must align with the environmental conditions they will face, such as pressure and temperature variations. For operations in high-temperature or corrosive environments, opting for materials like stainless steel or advanced high-strength alloys ensures durability and longevity. Moreover, advanced coatings and finishes offer additional protection against the harsh underground elements, further enhancing the joint's reliability.
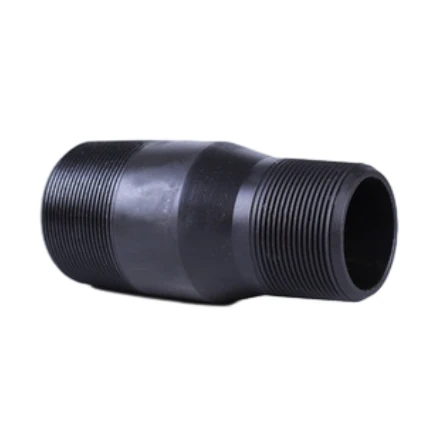
Professionals attest to the importance of precision in the manufacturing of pup joints. The process must adhere to stringent industry standards, such as API specifications, which guarantee their performance under extreme conditions. The threads of a pup joint, for example, require perfect alignment and integrity to prevent failures that could lead to costly downtime or environmental hazards. Therefore, investing in pup joints from reputable manufacturers with a proven track record is not merely advisable but necessary.
pup joint oil and gas
In terms of authority in the industry, manufacturers with ISO certification or those adhering to API standards are considered reliable sources for high-quality pup joints. Such certifications indicate a commitment to quality control and adherence to international safety standards, providing operators with the assurance of performance. Engaging with these manufacturers typically entails a partnership that facilitates continuous improvement and integration of the latest technological advancements in the field.
Trust in pup joints also stems from thorough testing protocols. Reputable suppliers conduct rigorous pressure tests and quality checks to verify each pup joint's capacity to withstand operational demands. This not only ensures compliance with industry standards but also builds trust with clients who depend on consistent performance. Operators can therefore perform their duties with the peace of mind that the equipment will withstand the operational pressures.
Practically speaking, pup joints contribute to substantial cost efficiencies. By enabling precise adjustments in the string length, they reduce the necessity for more extensive, expensive modifications or repairs. Furthermore, with the modularity they provide, operators can swiftly adapt to changes or unexpected conditions in the field, maintaining productivity and safeguarding the well integrity.
In conclusion,
the significance of pup joints in oil and gas extraction cannot be overstated. For those in the industry, a strong understanding of the specifications, materials, and testing protocols associated with pup joints is not only beneficial but essential. Partnering with trusted and expert manufacturers ensures reliability, safety, and efficiency—ultimately influencing the bottom line in the highly competitive oil and gas sector. As drilling environments become more challenging, staying at the forefront of pup joint innovations will be key to maintaining operational excellence and achieving sustainable growth in the field.