Pup joints are an integral component in the oil and gas industry, essential for adjusting the length of drill strings and facilitating efficient drilling operations. These tubular sections of pipes are precision-manufactured to meet industry standards, ensuring reliability and safety in demanding environments. For those deeply entrenched in the nuances of the oil and gas sector, the expertise surrounding pup joints can significantly enhance operational outcomes.
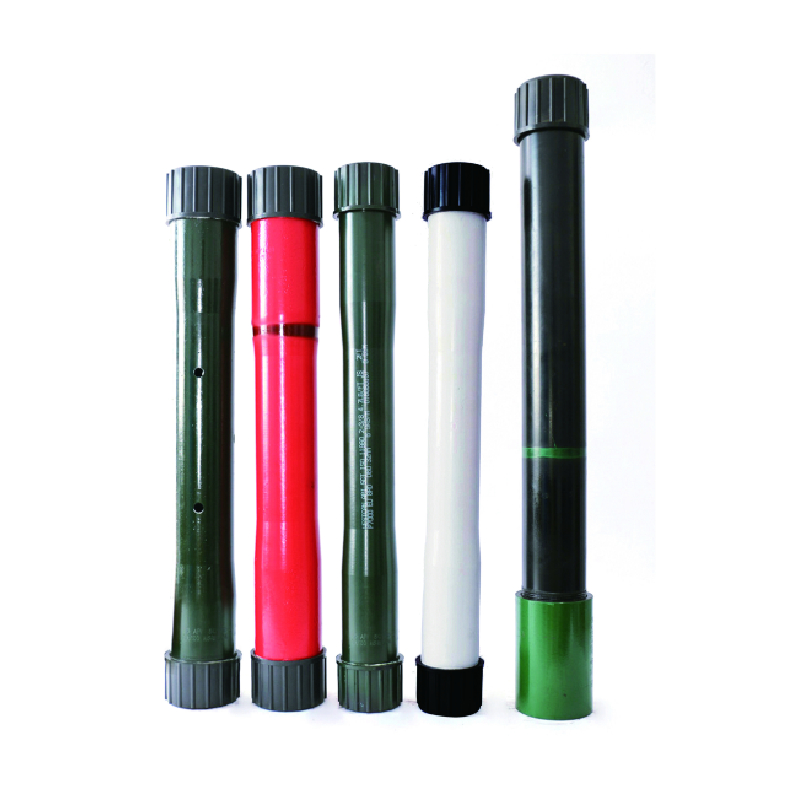
Understanding the specificities of pup joint application and functionality is crucial for optimization. These joints, available in various sizes and thread configurations, are designed to integrate seamlessly with drill pipes, casing, or tubing. This flexibility allows for precise adjustments in the drill string’s length, accommodating for unique drilling conditions or unexpected variations encountered in the field. Such adaptability underscores the pup joint’s role as a linchpin in customizing drilling operations to maximize efficiency and ensure well integrity.
The engineering behind pup joints reflects a depth of expertise dedicated to meeting the rigorous demands of oil and gas exploration. Comprised of high-grade steel or other alloys, these components are built to withstand substantial pressure and stress. This durability is critical in high-stakes drilling environments where equipment failures can lead to costly delays or safety incidents. Therefore, selecting a pup joint involves more than matching dimensions; it requires a nuanced understanding of material properties, tensile strength, and thread integrity to ensure compatibility and performance under extreme conditions.
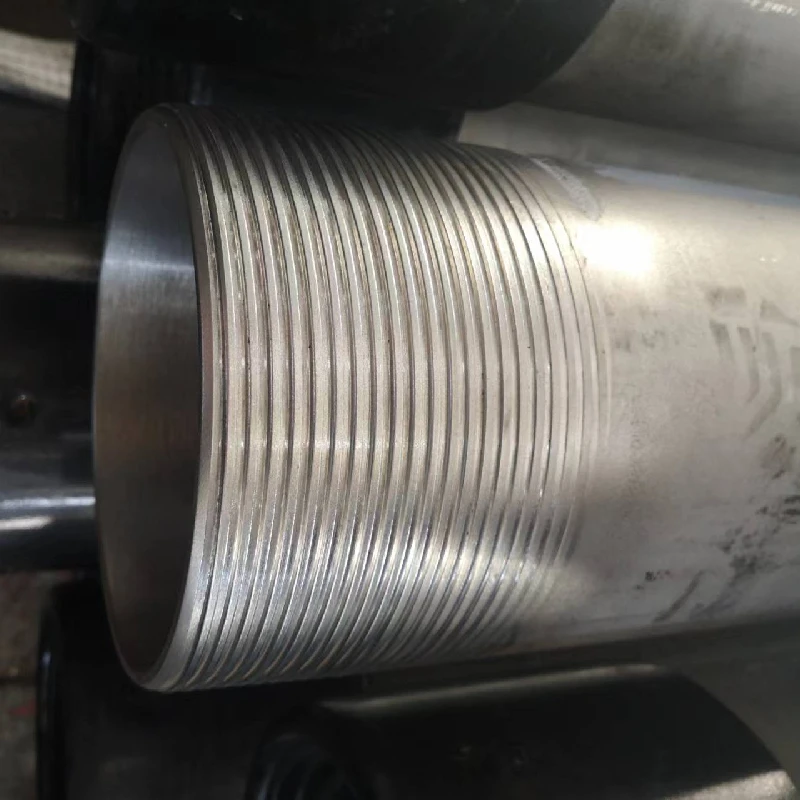
From an authoritative perspective, the selection and maintenance of pup joints are guided by industry standards such as the American Petroleum Institute (API) specifications, which ensure that all components meet consistent quality criteria. Compliance with these standards is non-negotiable for manufacturers aiming to earn the trust of operators and procurement specialists within the oil and gas industry. Having products that adhere to these universally accepted standards not only solidifies a manufacturer’s credibility but also guarantees that the pup joints will perform reliably in the field.
pup joint oil and gas
Trustworthiness in the context of pup joints doesn’t just come from product quality, but also from the reputation of the manufacturers and suppliers. Established companies with a proven track record for delivering high-performance oilfield equipment tend to inspire confidence among users. This confidence is further bolstered when these companies offer extensive testing and quality assurance processes, ensuring that every pup joint distributed is ready to handle the challenges of modern drilling.
For businesses and field operations aiming to optimize their drilling rigs' performance, it is imperative to remain informed about the latest developments and innovations related to pup joints. Engaging with experts and reviewing case studies where specific pup joint configurations led to improved drilling efficiency can serve as practical insights. Furthermore, maintaining a network of reliable suppliers who provide both standard and custom solutions can give operations an edge, facilitating swift adjustments and reducing downtime.
In summary,
pup joints are a fundamental element in the architecture of oil and gas drilling operations. Their role is enhanced by rigorous engineering, adherence to industry standards, and strategic procurement. Mastery of their use is not merely about understanding their physical properties but also involves navigating the broader landscape of industry standards and supplier reliability. Such comprehensive expertise ensures that drilling activities are executed with precision and safety, a testament to the relentless pursuit of excellence within the industry.