Pup joints are integral components in the oil and gas industry, often regarded as the unsung heroes of drilling operations. These short pieces of pipe are pivotal in adjusting the length of drill strings, tubing strings, or casing strings to ensure precise alignment and connectivity between other segments. Understanding the significance of pup joints can not only enhance operational efficiency but also optimize equipment performance, ensuring both safety and cost-effectiveness.
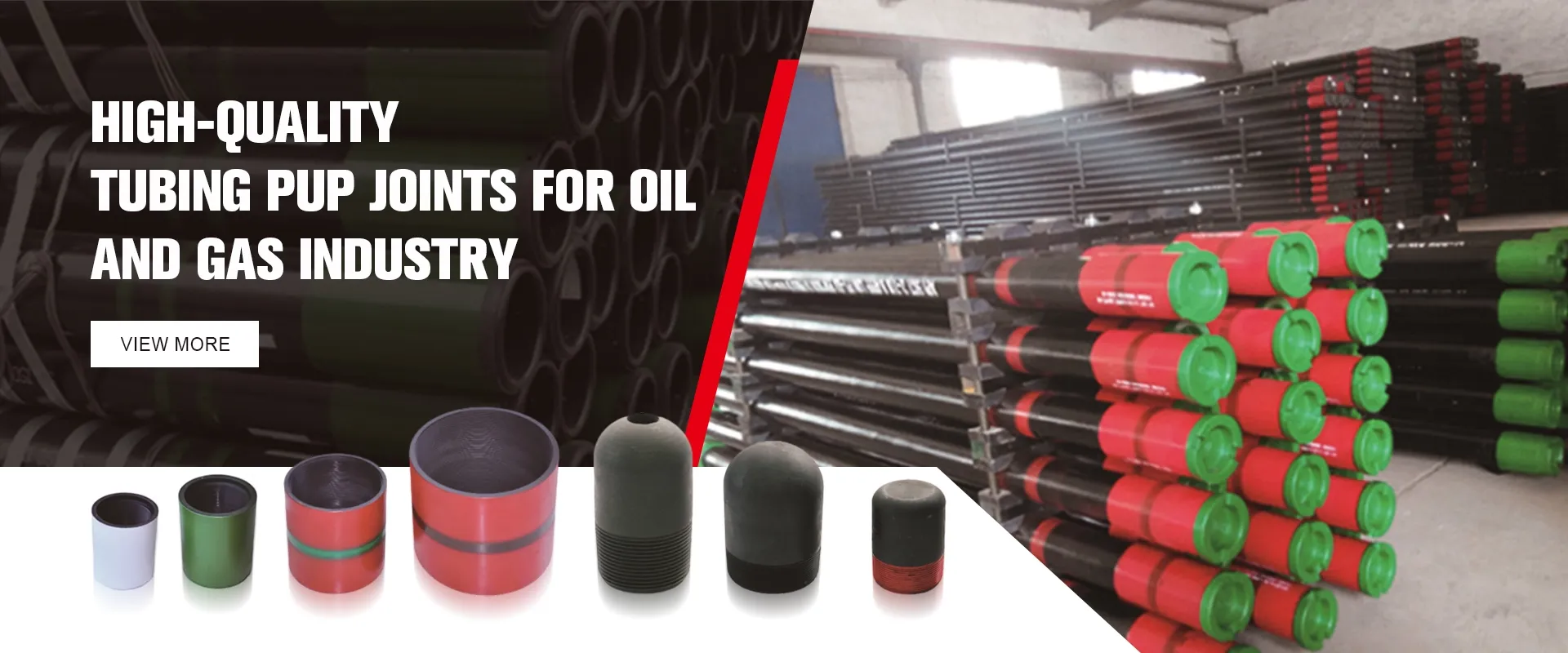
The utility of pup joints lies in their adaptability and their crucial role in fine-tuning the structures within oil and gas wells. Typically manufactured in lengths ranging from two to twelve feet, they facilitate seamless integration with larger piping systems. Pup joints are designed to endure high pressures and temperatures, making them indispensable in the challenging environments encountered in oil and gas extraction.
In terms of expertise, the choice of material for manufacturing pup joints is determined by the specific requirements of the drilling operation. Common materials include carbon steel, alloy steel, and stainless steel, each offering distinct advantages in terms of durability and resistance to corrosion. Carbide-embedded pup joints are gaining popularity due to their exceptional wear resistance, essential in minimizing the risk of equipment failure in abrasive conditions.
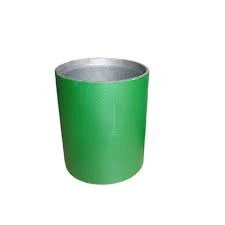
From an authoritative standpoint, standards for pup joints are set by recognized institutions such as the American Petroleum Institute (API). These standards ensure that the joints meet stringent requirements for performance and reliability. Adhering to API specifications not only guarantees compatibility with existing systems but also ensures the safety of the operation, reinforcing the trustworthiness of the equipment used.
Experience in handling pup joints reveals the critical nature of precise sizing and threading. Improper threading can lead to leaks or structural failures, underscoring the necessity of meticulous attention to detail. Technological advancements have ushered in automated threading machines, considerably reducing human error and improving the accuracy of threading operations.
pup joint oil and gas
Authoritative knowledge also highlights the importance of regular inspections and maintenance. Pup joints, like any other equipment, are subject to wear and tear, especially in high-stress environments. Implementing routine inspection protocols can detect potential issues before they escalate into costly failures. Non-destructive testing methods are particularly effective in identifying subsurface flaws that might not be visible to the naked eye.
In terms of trustworthiness, the effectiveness of pup joints is enhanced by comprehensive documentation of their usage history. Maintaining detailed records allows engineers to track the performance of these joints and anticipate potential issues based on historical data. This approach not only increases equipment reliability but also extends the lifecycle of the pup joints, thereby maximizing return on investment.
Operators within the oil and gas industry regard pup joints not merely as components but as critical elements ensuring the operational integrity of their drilling activities. Suppliers who offer comprehensive support, including customization options and technical assistance, are highly valued. Such partnerships contribute significantly to optimizing operations and achieving success in the demanding environments characteristic of the oil and gas sector.
In conclusion, the strategic deployment of pup joints within oil and gas operations underscores their indispensable role in the industry. Their capacity to endure extreme conditions while maintaining structural integrity establishes them as a cornerstone of drilling infrastructure. With advancements in material science and machining technology, pup joints continue to evolve, keeping pace with the ever-increasing demands of modern extraction techniques. Prioritizing their precision manufacturing, adherence to industry standards, and regular maintenance underscores their critical role in ensuring safe, efficient, and cost-effective operations.