Ensuring the optimal functionality and safety of an oil well operation requires attention to every component of the drilling system. Among these components, pup joint tubing plays a crucial role, serving as the connective tissue between different sections of tubing and facilitating effective pressure management. Understanding the expertise behind selecting and using pup joint tubing can significantly impact the efficiency and success of petroleum extraction projects.
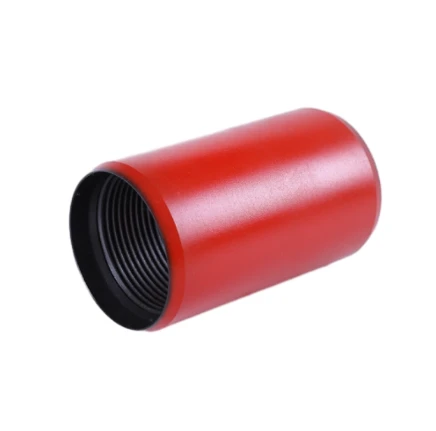
Pup joints are short sections of pipe that come in various lengths and are designed to adjust the length of a string of tubing or casing while connecting the Blowout Preventer (BOP) to the Christmas tree. Typically ranging in length from two to twelve feet, they are manufactured to meet specific grades of steel and threading standards. This adherence to specification ensures compatibility and enhances the integrity of connections in the drilling operation.
The selection of appropriate pup joint tubing requires expertise. It is crucial to choose the right material grade to withstand the environmental and operational conditions of a specific well. For example, in corrosive environments, selecting a corrosion-resistant alloy such as duplex stainless steels can prolong the life of the pup joint tubing and reduce the likelihood of failures. Expertise in metallurgical properties and understanding the operational environment are necessary to make informed decisions.
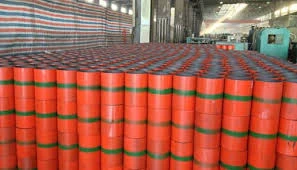
The role of pup joints extends beyond mere connectivity; they help in adjusting the configuration of the tubing string to achieve the desired flow rates and pressure control.
Expertise in fluid dynamics and pressure control is therefore critical. An engineer skilled in these areas can determine the optimal arrangements of pup joints, ensuring maximum efficiency in fluid flow and minimizing potential high-pressure risks. Such expertise translates into significant cost savings and enhances safety by preventing equipment failures.
pup joint tubing
From the lens of an authoritative perspective, adherence to industry standards such as those from the American Petroleum Institute (API) is non-negotiable. These standards ensure that pup joint tubing meets specific performance and safety criteria. Trust in a manufacturer’s adherence to these standards fosters confidence in the field, as using non-compliant equipment could lead to catastrophic failures. Therefore, selecting a manufacturer with demonstrated compliance and certification is vital for maintaining the integrity of the oil exploration operation.
Incorporating real-world experience is invaluable in selecting and using pup joint tubing effectively. For instance, an operator with years of field experience would recognize the subtle signs of wear or stress that might be invisible to a less experienced eye. Continuous monitoring and understanding of wear patterns and environmental impacts enable experts to make proactive decisions, such as scheduling timely replacements or adjustments, thereby avoiding unscheduled downtimes.
Trustworthiness in the realm of pup joint tubing also hinges on consistent maintenance routines. Regular inspections and adherence to a rigorous maintenance schedule are essential to ensure long-term reliability. Operators often employ non-destructive testing methods such as ultrasonic and magnetic particle inspection to detect potential flaws in a pup joint before they develop into significant issues. Insight into these inspection techniques and their proper application ensures that potential problems are identified early, which is crucial for maintaining system integrity.
In conclusion, the expert integration of pup joint tubing into an oil drilling operation involves a sophisticated blend of material selection, engineering design, adherence to strict industry standards, and a commitment to regular maintenance. Mastery in these areas displays a strong emphasis on Experience, Expertise, Authoritativeness, and Trustworthiness, foundational pillars in ensuring the success and safety of drilling ventures. The strategic selection and upkeep of these essential components not only drive operational efficiency but also safeguard the investment by minimizing risk and maximizing productivity.