In the world of oil and gas production, the term seating nipple is often discussed among professionals who understand the importance of ensuring the integrity and efficiency of downhole operations. These small, yet crucial components, play a significant role in the functionality and reliability of well completions. This article delves into the expertise required to understand seating nipples, the authoritative standards they must meet, and the trustworthiness they bring to oil extraction processes.
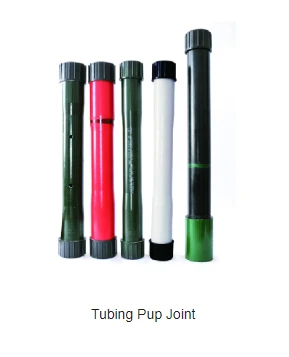
Seating nipples are precision-engineered devices installed in tubulars to facilitate the setting or seating of downhole tools. Designed to withstand the harsh environments encountered in oil and gas wells, these nipples must exhibit exceptional durability and precision.
Expertise in material science and mechanical engineering is paramount in their design and manufacture. The combination of high-strength materials and precise machining ensures that seating nipples can handle high pressures and abrasives found in well conditions.
In achieving expertise in the selection and implementation of seating nipples, understanding the different types available is crucial. There are two primary configurations seating nipples with no-go and those with a selective profile. No-go seating nipples are designed to stop and seal at a particular depth, providing a reliable stopping point for tools within the tubing string. This type of nipple is essential in maintaining control over tool placement, which is critical for effective zonal isolation and enhanced oil recovery.
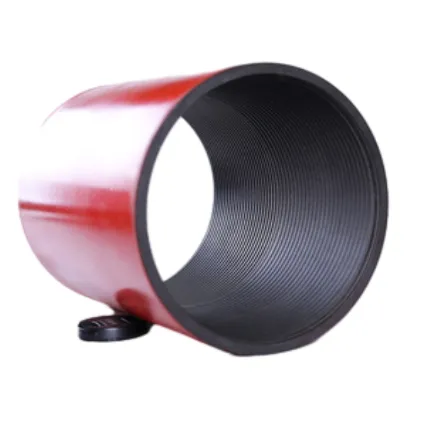
Selective profile seating nipples, on the other hand, allow tools to be landed at different predetermined depths. This versatility is beneficial in complex well architectures where multiple operations must occur at different levels. Having the expertise to identify the appropriate nipple for each specific application ensures optimal performance and service life, significantly affecting the overall efficiency of the well.
In the industry, authoritativeness is garnered by adherence to stringent industry standards and regulations. Recognized bodies such as the American Petroleum Institute (API) provide a set of guidelines and certifications that manufacturers must adhere to. Ensuring that seating nipples comply with these standards guarantees their reliability and performance, reinforcing their authoritative status in oil and gas operations.
seating nipple
The exacting standards that seating nipples must meet are a testament to their trustworthiness. In environments where failure can lead to catastrophic events such as blowouts or production loss, having reliable equipment is non-negotiable. End-users must trust that the equipment they select can withstand extreme conditions, ranging from high pressure and temperature to the corrosive nature of the extracted fluids.
An important aspect in assessing trustworthiness comes from field experiences shared by seasoned engineers and technicians who have leveraged seating nipples in real-world applications. These testimonials provide insights into the long-term performance and adaptability of seating nipples across different production scenarios. Gaining access to such field data and case studies helps operators make informed decisions, selecting solutions tailor-fitted to their unique challenges.
Finally, experience with seating nipples underlines the importance of regular maintenance and inspection. Even the most robust components are subject to wear and tear, and an effective maintenance program ensures their continued reliability. Engineers experienced in the maintenance of seating nipples can prevent unscheduled downtime, maintaining smooth operations and preserving the integrity of the entire well system.
In conclusion, seating nipples are indispensable in the oil and gas industry, providing essential service to ensure smooth and secure downhole operations. The expertise involved in their design and application, the authoritative standards they adhere to, and the proven trustworthiness in field deployments speak to their vital role. For industry professionals managing complex oil extraction landscapes, understanding these components' nuances increases operational efficiency and safety, making them a cornerstone of successful well completion strategies.